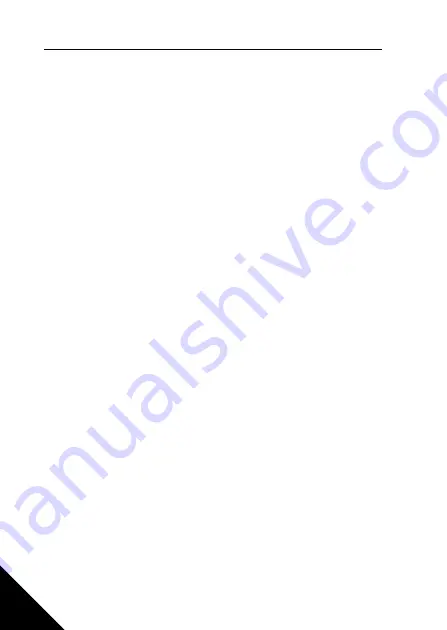
58
Parameter Descriptions
Honeywell
10
1.16
S
WITCHING
FREQUENCY
Motor noise can be minimised using a high switching frequency. Increasing
the switching frequency reduces the capacity of the frequency converter unit.
Switching frequency for SmartVFD COMPACT: 1.5…16 kHz.
1.17
B
RAKE
CHOPPER
Note!
An internal brake chopper is installed in three phase supply MI2 and MI3
size drives
0
= No brake chopper used
1
= Brake chopper used in Run state
2
= Used in Run and Stop state
When the frequency converter is decelerating the motor, the energy stored to
the inertia of the motor and the load are fed into an external brake resistor, if
the brake chopper has been activated. This enables the frequency converter
to decelerate the load with a torque equal to that of acceleration (provided that
the correct brake resistor has been selected). See separate Brake resistor in-
stallation manual.
1.18
M
OTORT
IDENTIFICATION
0
= No action
1
= ID no run
When ID no run is selected, the drive will perform an ID-run when it is started
from selected control place. Drive has to be started within 20 seconds, other-
wise identification is aborted.
The drive does not rotate the motor during ID no run. When ID run is ready the
drive is stopped. Drive will start normally, when the next start command is giv-
en.
The ID run improves the torque calculations and the automatic torque boost
function. It will also result in a better slip compensation in speed control (more
accurate RPM).