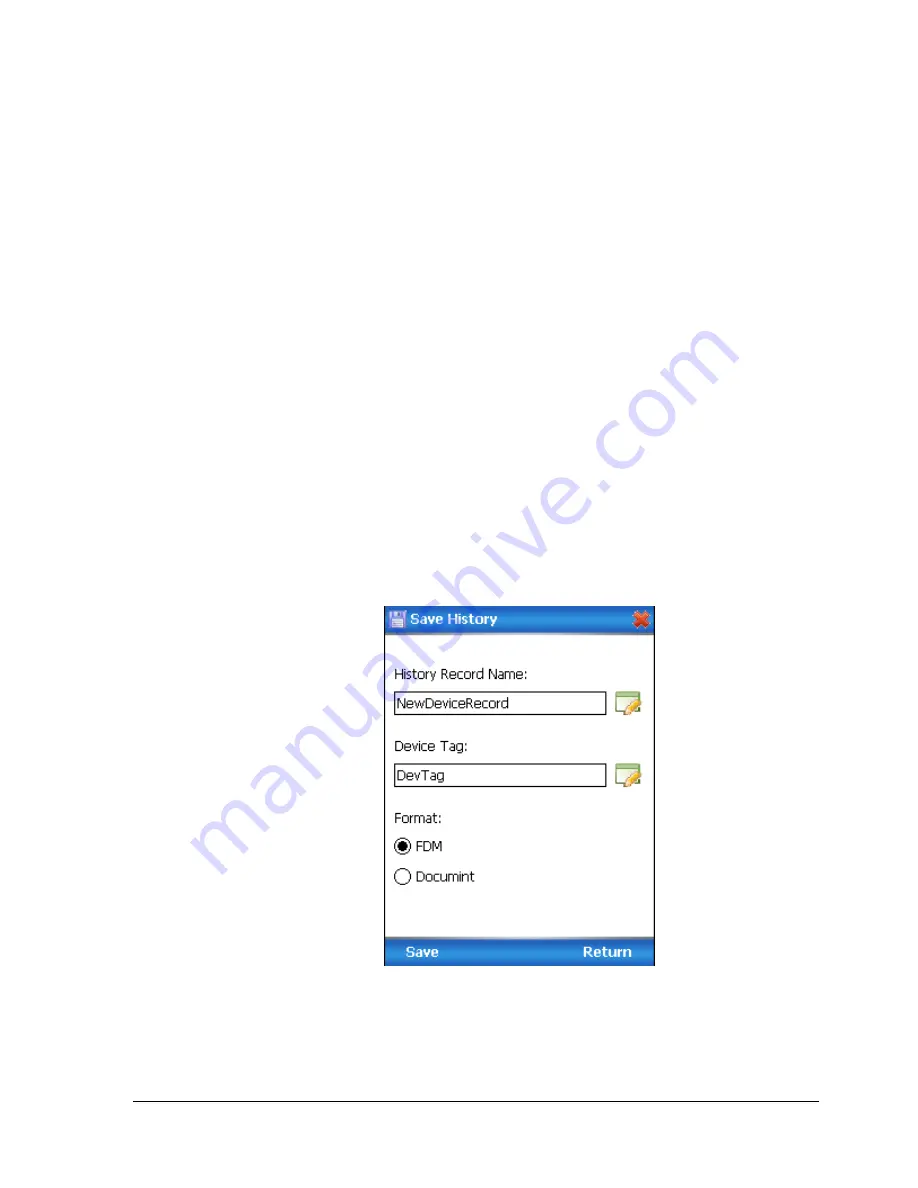
Revision 1
STT700 Series HART/DE Option User’s Manual
Page 59
5.
When the
Current applied process value:
is displayed, choose
Select as 4mA value
, and
click
OK
.
6.
Repeat steps 2 through 4 to set the URV to the applied input temperature for 20 mA output.
7.
Click
Return
to go back to the Calibration menu.
8.
Click
Send
. The Send to Device screen will be displayed.
9.
Select the
Apply Values
check-box.
10.
Click
Send
to download the change to the transmitter, or click
Return
to continue making
changes.
5.2.14 Saving device history
FDC provides you a feature wherein you can save the device configuration snapshot as history. This
history record may then be transferred to a central asset management database such as FDM.
Using this feature you can save the device configuration snapshot as device history of a connected
device at any given time in a predefined location. The following are the features of save device history
option.
Two formats of history are supported: FDM and DocuMint (legacy application).
Only one snapshot per device instance is allowed to be saved and you can save the
snapshot of a device any number of times overwriting the existing one.
To save device history, perform the following steps.
1.
On Device Home page, tap Tools.
2.
Select
Save History
and tap
Select
The
Save History
page appears.
3.
Enter the
History Record Name
using the keypad and tap
OK
. History Name field accepts
alphanumeric characters, underscore, and no other special characters.
4.
Enter the
Device Tag
using the keypad and tap
OK
. Device Tag field accepts alphanumeric
characters, underscore, and no other special characters.