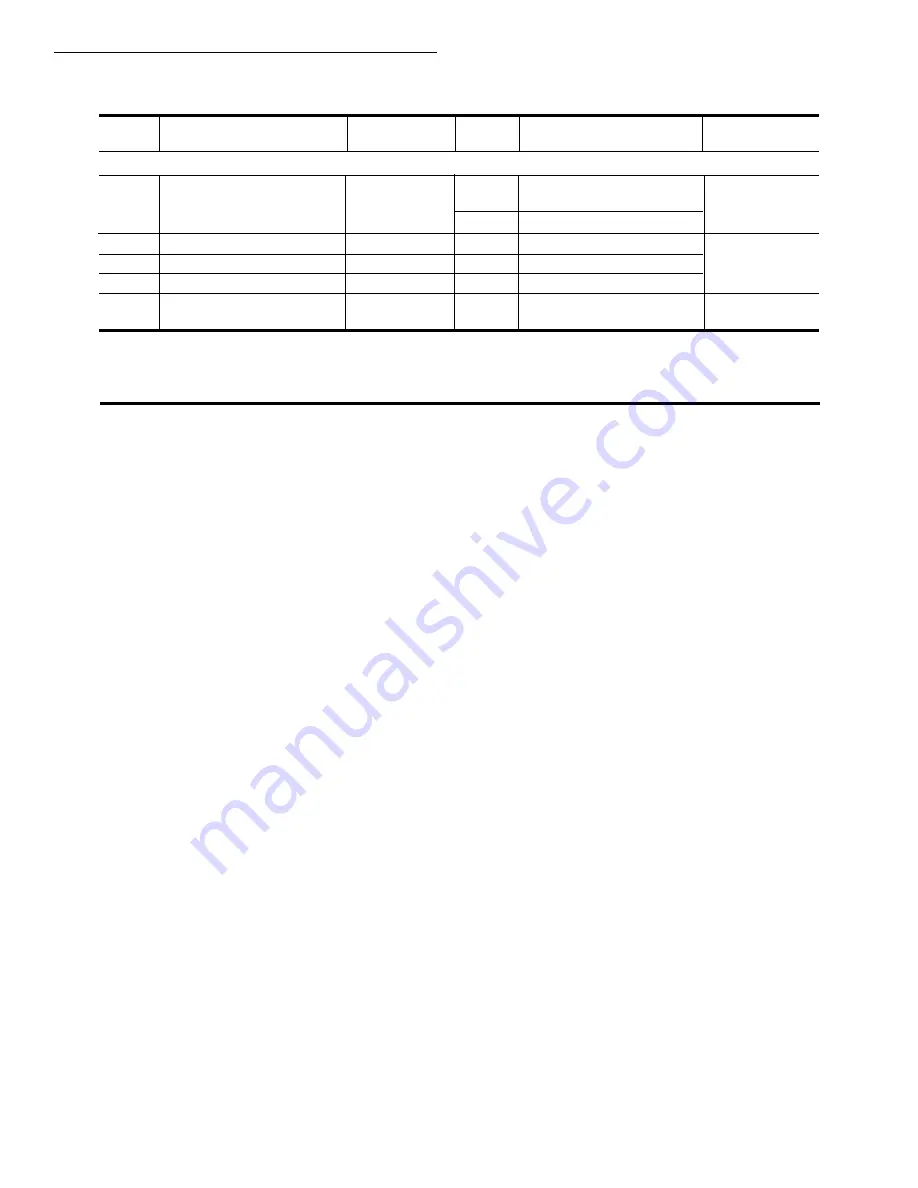
63-4309—2
32
OPTIONAL (continued)
205
[DO] AIR_OK
N/A
157
[DI] AIR_FL or
Must be
configured.
6
[AI] V_PRES
206
[DO] OD_DMP
N/A
None
N/A
209
[DO] VBOX+
N/A
None
215
[DO] OCCUP
N/A
None
216
[DO] DP_VLV
N/A
[DI] FRE_CL
Must be
configured.
VAV CONFIGURATION REQUIREMENTS (continued)
Control
Value
Control
Dependent
Dependent
Number
Variable Required
Required
Number
Variable Required
Value Required
PM7600B
PM7600B INPUT AND OUTPUT OPTIONS • OPERATION
Operation
The W7600 Control Module provides customized soft-
ware to maintain consistent discharge air temperature and
duct static pressure in Variable Air Volume (VAV) sys-
tems. Efficient control of supply fan, economizer, heating
and cooling equipment is essential to the W7600 system.
The system also provides monitoring and alarm for safety
inputs to protect VAV equipment. Control responds to a
Proportional plus Integral plus Derivative (P+I+D) algo-
rithm with specific strategies for heating, cooling and static
pressure. The P+I+D control algorithm eliminates offset
between the setpoint and the sensed temperature for precise
discharge air temperature and static pressure control. The
algorithm allows setpoint control within a specified sensi-
tivity range throughout all load conditions.
The system offers numerous input and output options
including analog outputs for modulating control, and digi-
tal outputs for energizing and de-energizing stages of heat-
ing and cooling. Inputs and outputs are user programmable,
as are control parameters such as number of stages, mini-
mum on/off times, reset type, motor speed, etc. Discharge
air temperature and static pressure setpoints are individu-
ally user programmable. Space or return air temperature is
monitored and heating may be energized when the tem-
perature drops below a programmable setpoint. The system
provides a programmable morning warm-up setpoint that is
monitored for transition from night mode to occupied tem-
perature. This setpoint also enables a changeover to heat
mode during the occupied mode if the temperature drops
below setpoint. The system also provides night setback and
morning warm-up in the heat mode. In cool mode, the
system allows shut-down for the unoccupied period. Out-
door air temperature may be monitored. The W7600 sys-
tem maintains discharge air temperature and duct static
pressure based on user programmable setpoint and control
band parameters. Setpoint is defined as the desired tem-
perature and pressure conditions. Control band is a devia-
tion band around the setpoint that is acceptable in the duct.
Discharge air or duct static conditions that are above the
cooling setpoint or below the heating setpoint generate a
demand signal to control the system as outlined in this
specification.
NOTE: THE W7600 VAV control algorithm reads the
analog inputs every fifteen seconds, with the exception of
analog input 1, which is read every five seconds. The
controlled outputs are updated every fifteen seconds,
with the exception of the pressure output, which is up-
dated every five seconds. Analog outputs (modulating)
change the controlled device at the rate of one percent per
second; i.e., 0 percent requires 100 seconds. The control-
ler determines whether it should change from cooling to
heating or from heating to cooling mode once per minute.
Minimum on and off times for heating and cooling must
be satisfied before the changeover can occur.
CHARACTERISTICS OF PROPORTIONAL,
PROPORTIONAL PLUG INTEGRAL (P+I) AND
PROPORTIONAL PLUS INTEGRAL PLUS DE-
RIVATIVE CONTROL (P+I+D)
The user can configure the proportional, integral and
derivative gains in the control algorithm to adjust the
control to the user’s needs. However,
it is recommended
that the default settings be used whenever possible to
avoid erratic control of temperature and static pres-
sure
. The characteristics of the control options are dis-
cussed below.
PROPORTIONAL CONTROL
In proportional control, the final control element moves
to a position proportional to the deviation of the value of the
controlled variable from the setpoint. The position of the
final control element is a linear function of the value of the
controlled variable.
PROPORTIONAL-INTEGRAL (PI) CONTROL
Proportional-integral (PI) control, also called
propor-
tional-plus-reset
control, virtually eliminates offset and
makes the proportional band nearly invisible. The major