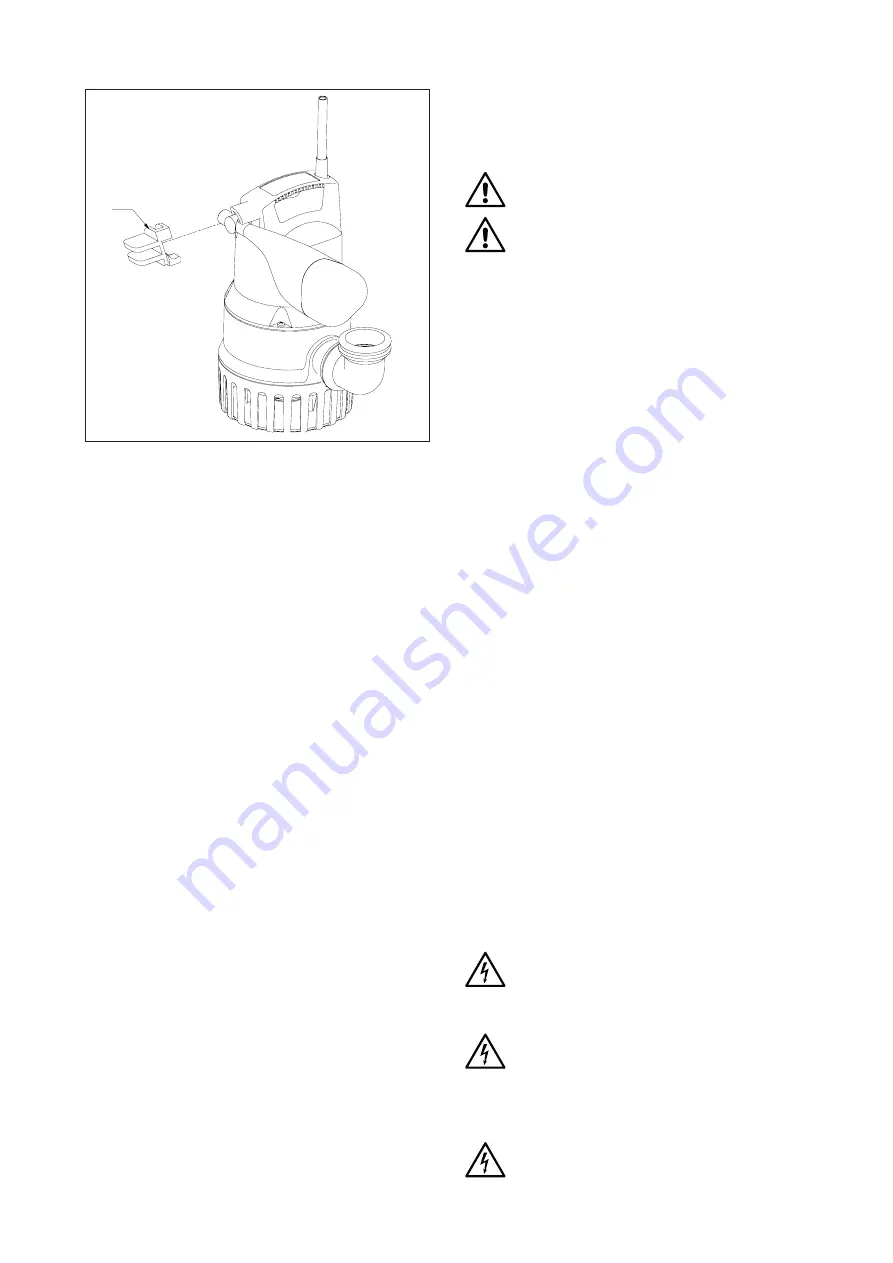
ENGLISH | 31
22
Connection of the pressure sensor for two pumps,
Saniquick UFT
In the Saniquick UFT version (double lifting unit with two
pumps), switching on and off is performed by means of a
pneumatic level switch. When connecting the PA hose to
the nipple of the control unit and to the pitot tube (in the
tank), make sure that there are no leaks. For the control
unit to function properly, it is important that the PA hose
from the pitot tube to the control unit is laid steadily up-
wards without loops, free of kinks and not pinched off. The
function of the control unit is described in chapter 5.5.1.
5.3. Commissioning
This chapter contains all important instructions for oper-
ating personnel for safe commissioning and operation of
the machinery. The following must be complied with and
checked:
• Type of installation
• Operation mode
• Minimal submersion in water / maximum submersion
depth
After a longer downtime these points must also be
checked and detected defaults must be repaired!
The operation and maintenance manual must always be
kept with the machinery, or in a dedicated place where it
is accessible for the entire operating personnel.
The following points must be taken into account to avoid
personal and material damage when troubleshooting ma-
chinery failures:
The commissioning of the machinery must only be
carried out by qualified and trained personnel in com-
pliance with the safety regulations.
• All personnel that is working on the machinery must
have received, read and understood the operating in-
structions.
• Activate all safety equipment and emergency switch-
offs before commissioning.
• Electrotechnical and mechanical settings must only
be carried out by specialists.
• This machinery is only suitable for the use under the
indicated operating conditions.
Never let the pump run dry for longer periods of time
(risk of overheating).
Before commissioning the system, existing pipe
valves or gate valves must be opened.
5.4. Preparatory work
The machinery was constructed and fitted according to
the latest technology, so that it works for a long time and
reliably under normal operating conditions. This requires
however that you comply with all requirements and infor-
mations. Small oil leakages of the floating ring seals on
delivery are not problematic, but they must be removed
before lowering/immersion into the medium.
Please check the following points:
• Cable run - no loops, slightly tightened
• Check temperature of the medium and submersion
depth - see machinery data sheet
• If a tube is used for pressure, this must be rinsed with
clear water so that no deposits lead to obstruction.
• The pump pit must be cleaned for wet installation
• The pressure-sided and suction-sided pipework sys-
tem must be cleaned and all gate valves must be
opened
• The pump casing must be flooded, e.g. it must be
filled completely with the medium and it must not
contain an air. The de-aeration can be carried out by
means of suitable venting devices in the system or, if
available, by air-vent screws on the pressure socket.
• Check accessories, pipework, suspension devices for
firm and correct fitting
• Check available level controls/protection against dry
run
5.5. Electrical system
The respective local and VDE regulations must be com-
plied with when choosing and installing the electrical
leads as well as connecting the motor. The motor must be
protected with a circuit breaker. The motor must be con-
nected according to the wiring diagram. Note the direction
of rotation! In the event of wrong direction of rotation the
machine does not perform as indicated and it can become
damaged under unfavourable circumstances.
Electric shock hazard!
Faulty dealing with current may jeopardize your life!
All pumps with free cable ends must be connected by
a qualified electrician.
A professional inspection prior to commissioning
must ensure that the required electrical protective
measures are available. The grounding, earthing,
isolating transformer, and fault current or voltage
fault protection switch must meet the requirements
of the responsible power plant.
The voltage specified in the Technical Data must cor-
respond to the available mains voltage.