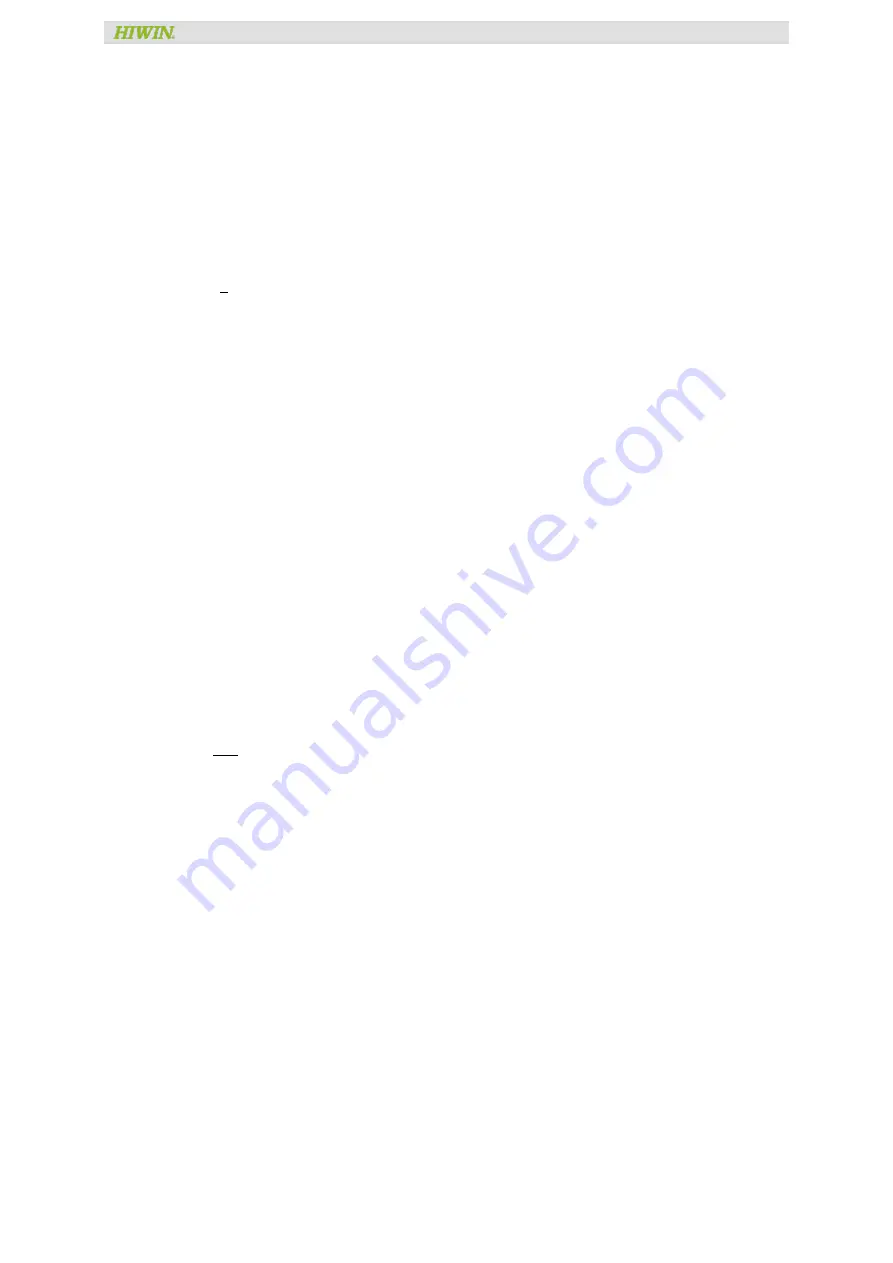
Assembly Instruction
Configuration
Torque Motor
TM-Komponenten-04-0-EN-2108-MA
Page 24 of 84
3.2
Thermal calculation
3.2.1
Heat loss
When the motor converts electric energy into kinetic energy, copper loss, iron loss and mechanical loss are
inevitable. Copper loss is the loss generated by the resistance when the current flows through the stator coil of
the motor. Iron loss, which can be classified into hysteresis loss and eddy current loss, is generated by the
conversion of the magnetic field between stator iron core and rotor magnet. As for mechanical loss, it is
generally much less than copper loss and iron loss; therefore, it can be ignored.
Copper loss under continuous torque is calculated as below.
P
c
=
3
2 R
25
{1 + [0.00393(
θ
c
−
25)]}I
c
2
P
c
=copper loss at coil temperature
θ
c
[W]
R
25
= line-to-line resistance at coil temperature 25
℃
[
Ω
]
I
c
=
continuous current at coil temperature
θ
c
[
A
rms
]
θ
c
= coil temperature [
℃
] (120
℃
for TMRW series, 130
℃
for TM-2/IM-2 series)
Iron loss is mainly caused by the change of magnetic flux during the commutation process and is influenced by
the frequency a lot. Since rotational speed is directly proportional to frequency, iron loss will be larger at high
speed. However, rotational speed for HIWIN torque motor is low, so iron loss is relatively less than copper loss.
Rotational speed value indicated by HIWIN drawing and specification is the maximum peak speed that the motor
can reach. Under the continuous operation of high speed, iron loss must calculate extra heat given to rotor. At
this time, motor loss increases rapidly. To avoid overheating, users need to appropriately adjust operating
conditions or apply heat dissipation on rotor.
Iron loss is mainly generated by eddy current and frequency. The faster the speed is, the more the iron loss will
be.
P
Fe
∝
f
2
P
Fe
=
iron loss [
W
]
f
= frequency [
Hz
]
Definition of frequency
:
f =
n
⋅
p
60
n
= rotational speed [
rpm
]
p
= Number of poles pair
Heat loss mainly transmits the loss of coil and iron core to motor outer casing via heat conduction. Take natural
air cooling for example. Lost heat source will be transmitted from the surface of outer casing contacted by the
air to external environment via heat convection, and from the customer’s installation surface via heat radiation
and heat conduction. As for water cooling, lost heat source will be transmitted from center of heat source to
cooling water via heat conduction. Since the heat-conduction coefficient of cooling water is much higher than
that of air, the effect that heat source transmits to the air via convection can be ignored. TMRW series is
available to either water cooling or air cooling while TM-2 and IM-2 series are mainly available to water cooling.
Ensure parameters you use fit the specification, and keep coil temperature from exceeding 120
℃
. (for
□
M-2 is
130
℃
)
. Please contact HIWIN for other applications.