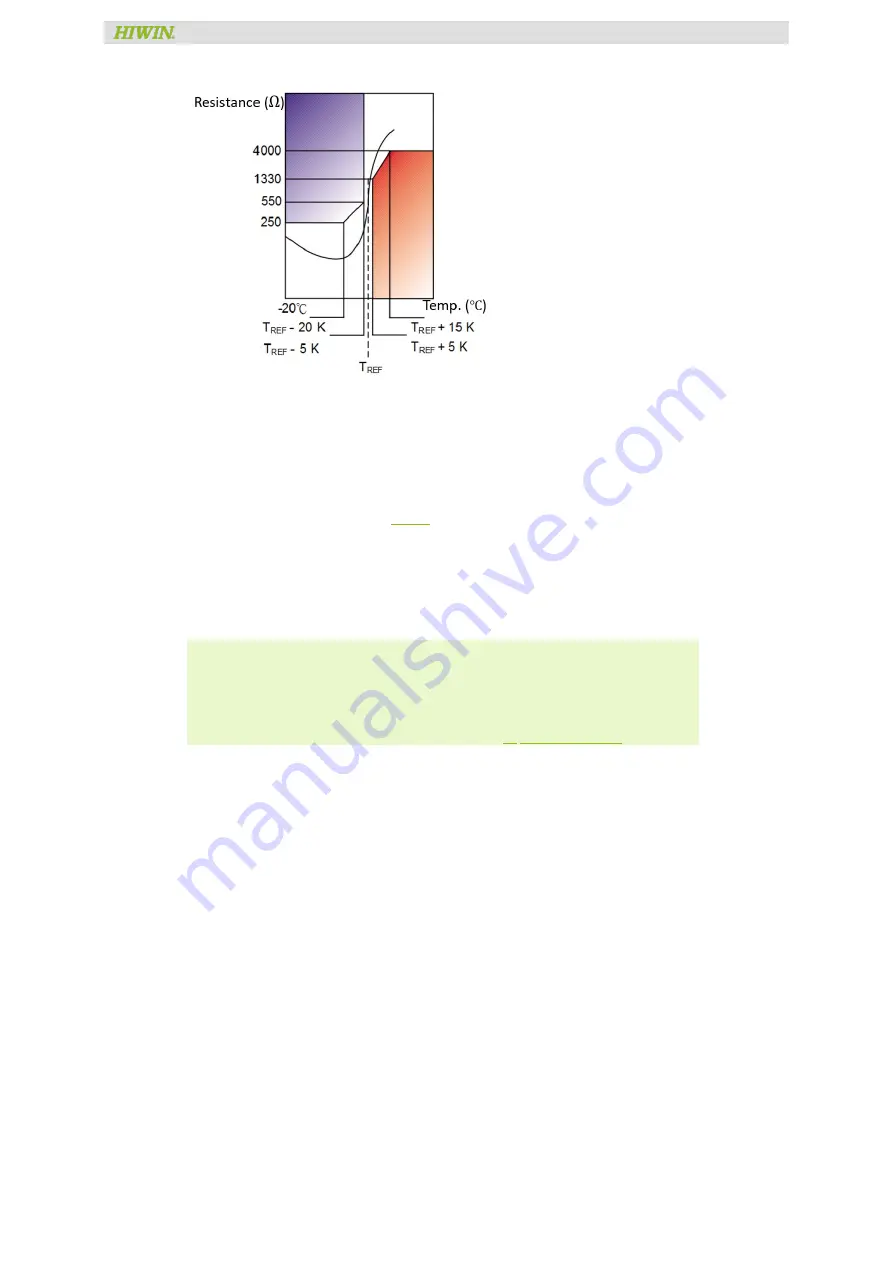
Assembly Instruction
Motor Interface Design
Torque Motor
TM-Komponenten-04-0-EN-2108-MA
Page 59 of 84
Fig. 4.26: Relationship between PTC temperature and resistance
4.10.1
Temperature monitoring and motor protection
To protect the motor windings against thermal damage, every motor is equipped with a triple positive
temperature coefficient (PTC) sensor, type SNM120/130 (in accordance with DIN 44082-M180). Since the degree
of heating of the individual motor phases can be very different, a PTC sensor is fitted in each phase winding (U, V
and W). Each PTC element has a “Quasi-switching” characteristic, i.e. the resistance suddenly increases close to
the rated temperature (switching threshold, Fig. 4.26). Due to its low heat capacity and good thermal contact
with the motor winding, the PTC reacts very quickly to a rise in temperature and, in conjunction with additional
protective mechanisms on the control side, ensures reliable motor protection against overload. The PTC
elements located in every phase winding in HIWIN motors are wired in series; they connect via two wires.
With TMRW/TM-2/IM-2 there is an additional temperature circuit with positive temperature coefficient (PTC),
type SNM100, for redundant use or to distinguish between warning and danger temperatures.
Note:
Motor protection by temperature monitoring alone using PTC elements can be insufficient. This is the case, for
example, if the motor is operated with currents above continuous current.
HIWIN advises the use of additional protective algorithm on the control side. The calculation of max. operating
time with currents above continuous current can be found in Chapter 3.3 Thermal time constant.
4.10.2
Connection to the drive amplifier
The temperature monitoring circuits can normally be connected directly to the drive control. If the protective
separation requirements in accordance with EN61800-5-1 are to be fulfilled, the sensors must be connected to
the decoupling modules provided by the drive manufacturers.