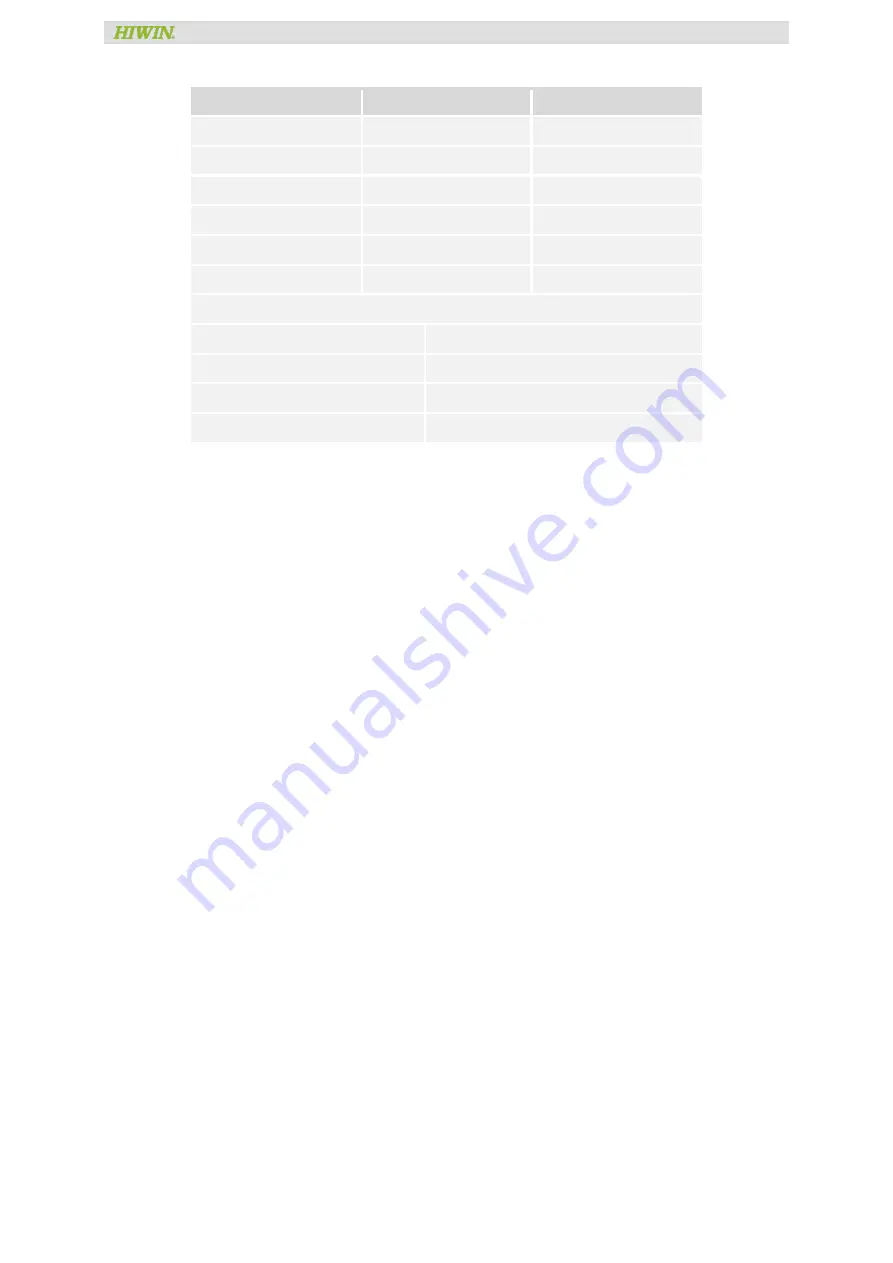
Assembly Instruction
Introduction
Torque Motor
TM-Komponenten-04-0-EN-2108-MA
Page 14 of 84
Table 1.5: Transport conditions
Environmental parameter
Unit
Value
Air temperature
(
℃
)
-5 ~ 40
Relative humidity
(%)
5 ~ 85
Rate of change of temperature
(
℃
/min)
0,5
Condensation
Not allowed
Formation of ice
Not allowed
Transport condition
Class 2K2
Transport the motor in an environment with good weather protection (indoor/factory)
Biological conditions
Class 2B1
Chemically active substances
Class 2C1
Mechanically active substances
Class 2S2
Mechanical conditions
Class 2M2