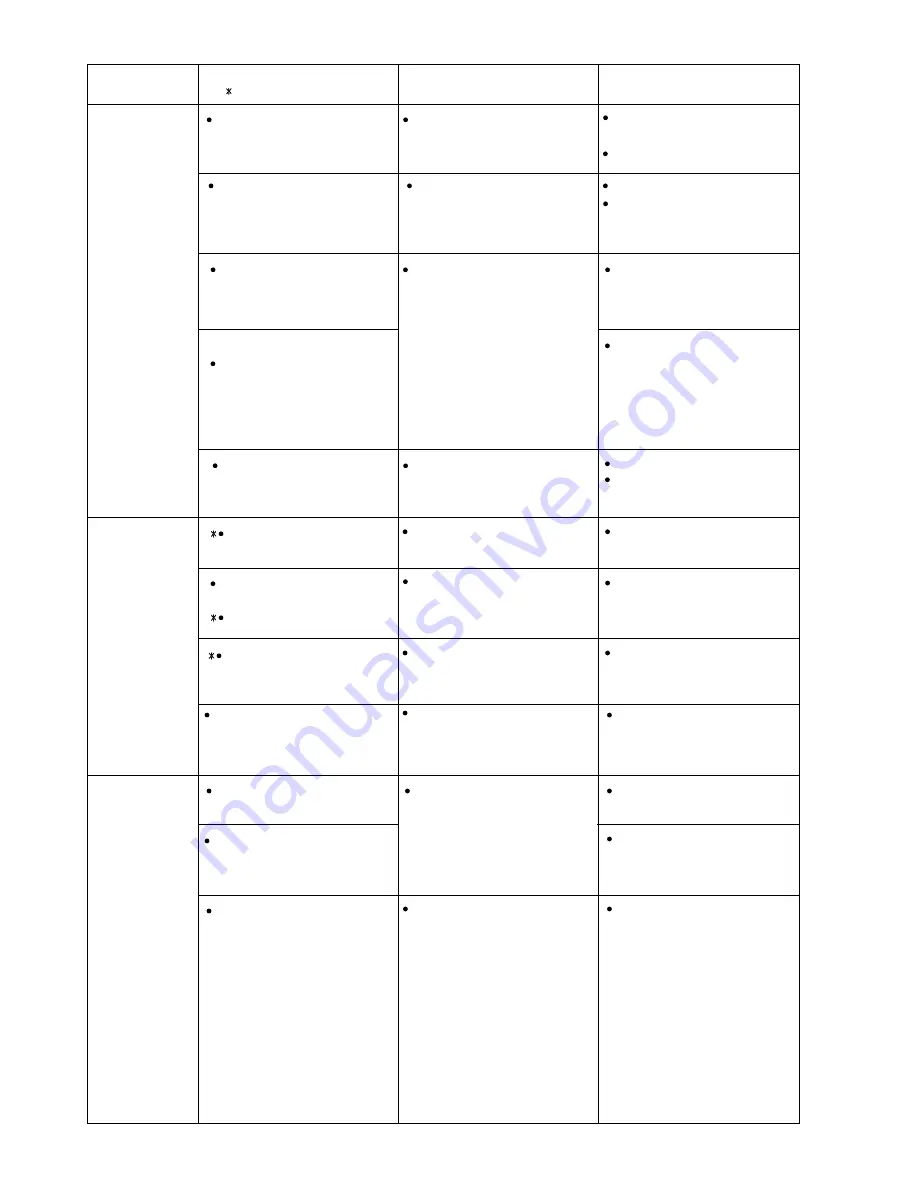
--- 16 ---
Set the adjuster to the
optimum position.
Replace the part.
Cylinder inside surface is
abnormal (packed with
dust, or worn).
Head valve sliding surface
is abnormal (seized or
damaged, or lubrication is
needed).
Head valve spring is
abnormal (fatigued or
damaged).
<Control valve section>
Plunger (A), valve piston
(B), valve bushing (A) or
valve bushing (B) is
abnormal (seized or
damaged).
O-rings or sliding surface
are worn or needs
lubrication.
Adjuster is raised too high
for short nails.
Nails are not completely fed
into the injection port.
Unspecified nails are used.
Remove dust and then
lubricate.
Replace the part.
Replace the part.
Apply grease.
Check that the adjuster is
not raised too high.
See item 1).
Problem
Possible cause
( : Most-common cause)
Inspection method
Remedy
1) Nails cannot
be driven.
(continued)
Workpiece is too hard.
Nailer cannot be used
because the material is
beyond its applicable range.
Check if a nail is bent even
when driven into soft wood.
Check that the driver blade
tip is not abnormally worn.
Replace the abnormal part.
Turn the adjuster lower
(lower the pressure).
See item 1).
Driver blade is worn.
Replace the part.
Adjust the air pressure to
5 --- 8.5 kgf/cm
2
(4.9 --- 8.3
bar, 70 --- 120 psi).
Nailer cannot be used
because the material is
beyond its applicable range.
Check that nails can be
driven at 5 kgf/cm
2
(4.9 bar,
70 psi).
Perform idle driving to
check the driving
operation.
Perform idle driving to check
that the driver blade is not
held in the down position.
Disassemble the control
valve section and check the
O-rings.
Replace the abnormal part.
Apply grease.
2) Nails are
driven but
bent.
3) Nails cannot
be driven into
the workpiece
completely:
the heads
cannot be
made flush.
Adjuster is incorrectly set.
Air pressure is too low.
Workpiece is too hard.
Turn the adjuster to the
lowest position and then
drive nails.
Check if a nail is bent even
when driven into soft wood.
Summary of Contents for NV 75AG
Page 45: ......