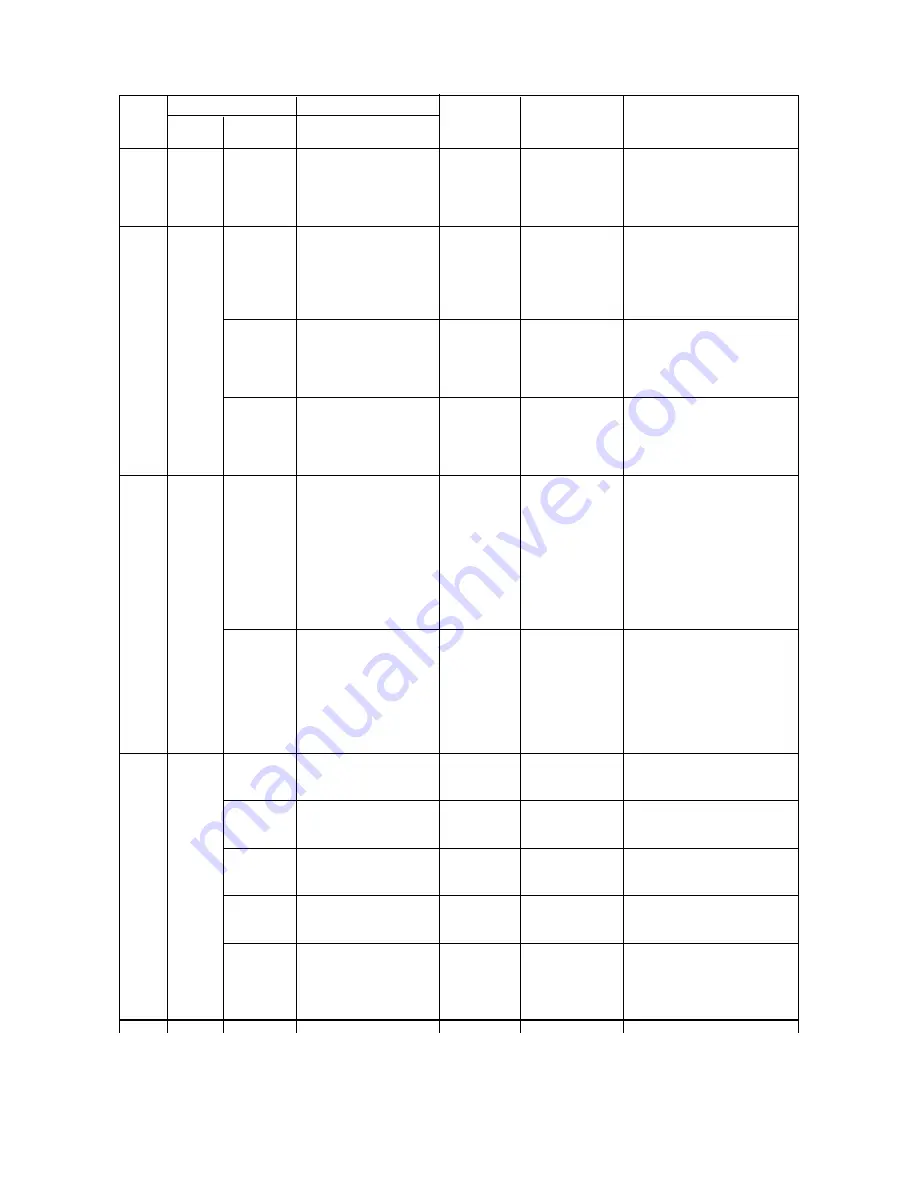
12-11
Display
(Function mode 1)
(Function mode 2)
Setting, change
sequence
Function
Function
Initialization display
Initialization
contents
Setting contents
No.
name
contents
Frequency
IN F-SAMP
8
8
1 to 8
command
sampling
frequency
setting
25
F-32
Arrival
ARV PTN
CST
CST
CST/PAT/ANY
CST: Output at constant
Frequency signal output
frequency arrival
arrival
pattern
PAT: Output of more than
output
selection
set frequency
signal
ANY: Output of only set
frequency
Arrival
ARV ACC
0.0 Hz
0 Hz
0 to 400.0
frequency
rate setting
for
acceleration
Arrival
ARV DEC
0.0 Hz
0 Hz
0 to 400.0
frequency
rate setting
for
deceleration
26
F-33
Overtorque
OV-TRQ V
100%
100%
0 to 250
• During control of SLV
Over-
signal rate
and V2: Power running
torque
setting
overtorque level
signal
(for power
• During control of VC
(NOTE 1) running)
and VP1 to VP3:
Warning level for power
running regenerative
overload
• When 0 is set: Any signal
is not output.
Overtorque
OV-TRQ R
100%
100%
0 to 250
• During control of SLV
signal rate
and V2: Regenerative
setting
overtorque level
(for regen-
• During control of VC
eration)
and VP1 to VP3: No
effect
• When 0 is set: Any signal
is not output.
27
F-34
Input
IN-TM 1
RS
RS reset
RS and 17
Intelligent terminal 1
terminal
other terminals
terminal
setting
input
Input
IN-TM 2
AT
AT current
AT and 17
terminal
terminal 2
input selection other terminals
setting
setting
terminal
Input
IN-TM 3
JG
JG jogging
JG and17
terminal 3
terminal
other terminals
setting
Input
IN-TM 4
FRS
FRS free
FRS and 17
terminal 4
run
other terminals
setting
terminal
Input
IN TM 5
CH1
CH1 2-stage
CH1 and 17
terminal 5
acceleration
other terminals
setting
and
deceleration
terminal
NOTE 1: When setting 20% or less, the error will increase (± 20% or more).
Therefore, set 20% or more.