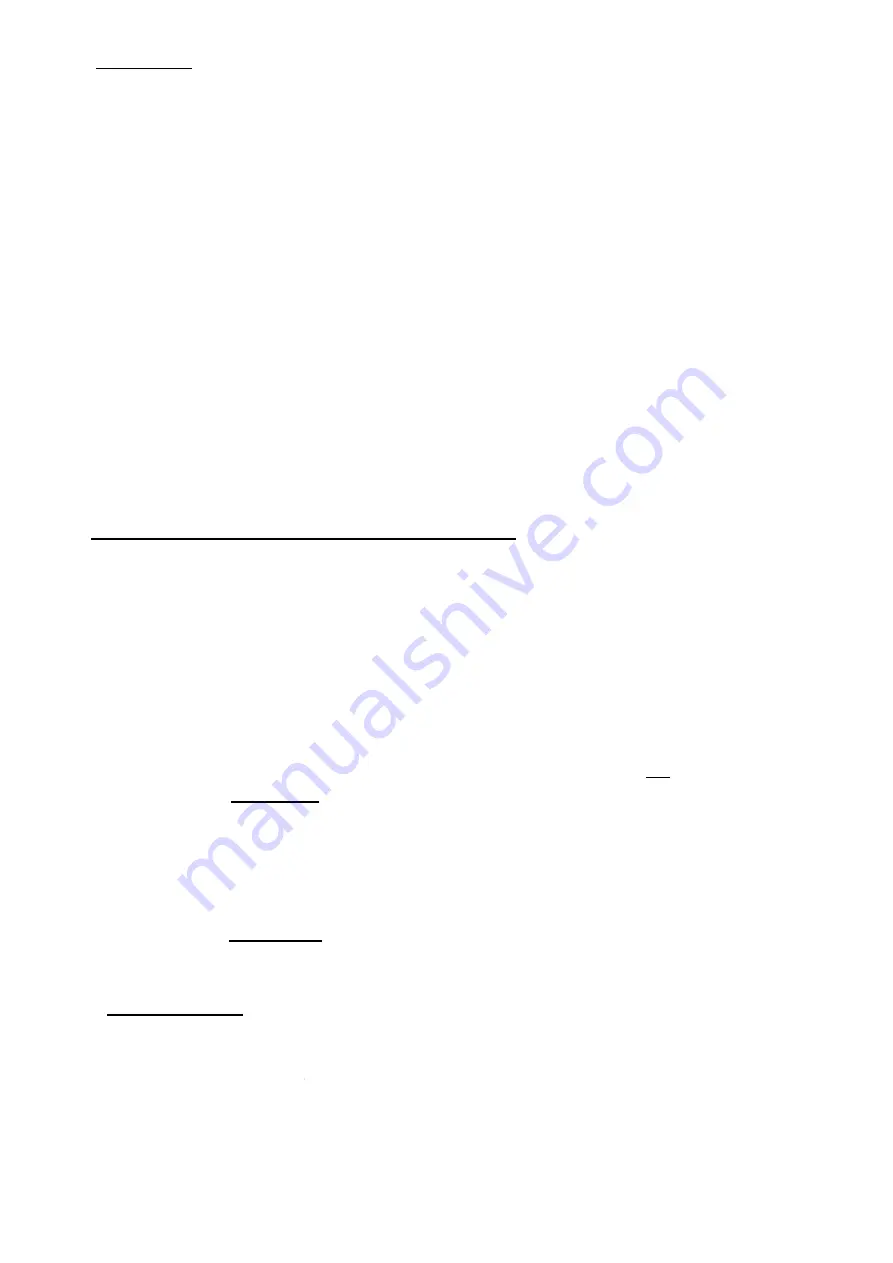
3/2
8
OVERVIEW
•
The Hevac ENDEAVOUR is a fully programmable microprocessor based Temperature
(+ CO2)
controller, with optional use of a
n
internal 365 day Time Switch, an independent Auxiliary
Time Switch and a Run Timer all in the one model. The controller has 7 analogue inputs, 4 digital
inputs, 5 relay
outputs
and 2 analogue (0-10vDC) outputs. Controller I/O
,
time & date etc. is
displayed via a backlit LCD screen giving plain English status information together with 5
dedicated
LED’s showing the relays
on/off
stat
e
. The controller is primarily intended for Air Conditioning
t
emperature control applications where On/Off
control
of Heating
and
Cooling
stages
and /or
modulating
P+I
control of actuators
/
devices requiring a variable 0-10vdc control signal is
required.
Typically
used to control
DX Air Conditioning units, Electric heating stages, modulating
Heating &
Cooling Valves, VSD’s & Economy Cycle Damper sets etc. Note with this latest software
version, the
Endeavour can now
also
be set
to
"Time Switch only" mode with all other none timer
capabilities
disabled allowing this module to be used as a
2 channel
365 day
T
ime
S
witch
o
r
R
un
Ti
mer
only
.
•
Four of the five relays are programmable for their mode of operation ie :Heat,
Cool or
Both
(both
means the relay operates as both a heating and cooling stage
)
, and also new to
this
version,
relays
can now be programmed as On/Off CO2 stages
or
as an extra independent
A
uxiliary
Time
Switch.
The relay program menu allows individual settings of
mode,
deadbands, switching
differentials &
time
delays. The 5th relay is dedicated as a System Run (Fan / Main Time Switch)
relay which
can
now also be set to operate continuously whilst the controller is enabled or to
cycle
on & off
with
the
compressor (which is typical
for
domestic A/C systems). The two available
Analogue
0-
10vDC
output signals can be
individually
programmed for Mode of operation (heat /cool
or both),
start point
(deadband)
,
range (proportional band) & method of control (P or P+I)
plus
a
lso
new to
this
version
the
minimum & maximum "
Y
"
output 0-10vdc
signals can now be range limited,
with
any
minimum
value
setting
automatically
overridden to zero when the system is off
, which is
perfect for EC fan time
switch control with a minimum speed requirement.
EXTERNAL OVERRIDES & OPTIONAL CONNECTIONS
•
The controller has
Modbus
communications capability for connecting of up to 32 controllers to our
HMI colour wall
display
panel for zone status, individual setpoint adjustment & system
Auto/Off/On
override
. Alternatively upto 247 controllers can be connected to a 3rd party BMS
system for remote
control & monitoring.
For added BMS monitoring, analogue input "X4" can be used to measure
an
auxiliary
temperature (typically the supply air temperature)
, "D3"
is a dedicated A/C fault
monitoring
input & "D4" is a general purpose on/off status input that
could
be used for
example
to
monitor
&
prove
supply air fan running operation
via a mechanical pressure switch.
•
Remote System
AUTO
/OFF & AHR
operation can be easily added by simply connecting a
normally
open (N/O) switch anywhere convenient in parallel with the main temperature sensor
wires
X1 & M.
Momentarily shorting X1 & M results in triggering a run timer function (typically as
an
after hours
timer function) or
/ &
constant shorting of X1 & M results in a system
OFF
function.
These
functions
are also duplicated on the controller terminals "D1 & M" for AUTO/OFF &
AHR operation,
plus
connecting a switch to "D2 & M"
sets
a forced manual Time switch
"24/7
ON
"
override.
•
With an optional
O/A sensor
connected, the Economy cycle damper operation (Y1 output) for
temperature control can be interlocked for free heating, cooling or both when the outside air
temperature conditions are favorable. The fresh air sensor (X3) is compared to the room (or return
air) temperature sensor (X1),
&
if the outside air temperature is measured to be more suitable for
free
temperature control the motorized damper output signal (Y1) will modulate to F/A mode per
room
temperature demand. The use of outside air for temperature control can also be inhibited if the
outside air temperature falls below an adjustable minimum O/A temperature (factory set at 16C for
DX or FCU coil protection ).
•
With an optional
CO2 sensor
connected, economy cycle dampers can also be proportionally driven
to the fresh air mode to reduce high CO2 levels. The maximum damper output signal for CO2
control can be restricted in extreme O/A temperatures so as not to lose temperature control, all
settings are user adjustable. The CO2 input can now also control relays for on/off CO2 control.
•
Remote Set Point
devices
(either passive or active)
can be connected to the controller. If a passive
adjuster is connected (default setting), the controller will automatically detect and hand over set
point
adjustment authority to the remote device (then ignoring the controllers UP & DOWN buttons
for set
point adjustment). The remote set point potentiometer can be built into a room
temperature
sensor
(SRT-DSP) or as a separate stand alone device giving remote setpoint control
only (SPA-D).
The
range of the passive remote setpoint is fixed at 18 to 25 degrees over 0 to 10K
. I
f
an active
remote
setpoint device is used the 0-10vDC is +/-5c adjustable for 0v & the top end range
adjustable upto
100c.
Also new
:
Any remote setpoint
device can now be
temporarily virtually disconnect
ed
by
holding the UP &
DOWN buttons together for 5 seconds which hands
conventional setpoint control
back to the
controller to aid in commissioning & testing
,
but will
automatically reset to remote control
after 10
minutes or can be canceled anytime by again
pushing the UP & DOWN buttons together.
HEVAC Control Agencies Pty Ltd
www.hevac.com.au
Ph +613 95627888
28
/11
/19