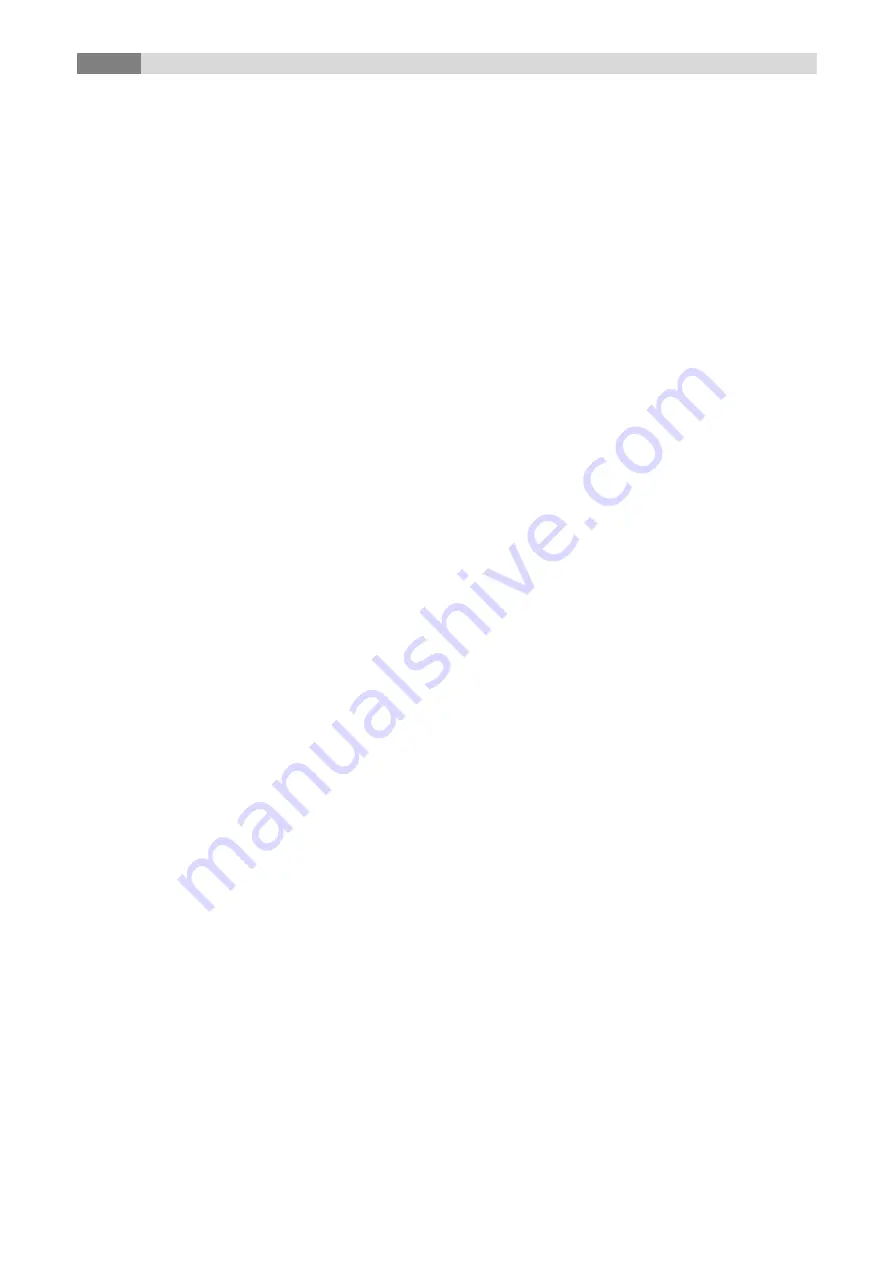
6
Mode of operation
12
6
MODE OF OPERATION
6.1
Feeding system
The fuel is fed from the fuel storage room by the
room discharge system to the burn back
protection device (BFP). Fuel passes the hopper
first, afterwards the back burn flap. The back burn
flap gets steered by a spring loaded servo motor.
If the servo motor operates current less, the back
burn flap will close independently. Next the fuel is
fed towards the burning chamber by the feeding
screw. The achieved fuel level is a crucial factor of
the boiler heat output and operating mode.
6.2
Feeding type
The operation of the BioFire is based on a pulse-
no-pulse ratio, which controls the feeding system.
All the values are to be set via the menu “Fuel
values” (only available in the service area). These
feed values are corrected by the combustion
control system.
6.3
Combustion air control
The supplied combustion air is differentiated
between primary and secondary air. The primary
air is initiated directly into the embers. The
secondary air gets used to actuate the developed
flame to a completely. The air supply is piped via
vents on the burner side (underneath side cover).
The ID-fan is time-controlled by the variable-
speed electronic control. The ID-fan speed is
controlled according to the boiler temperature and
rectified by the lambda control.
6.4
Boiler operation
The boiler starts up automatically with its built-in
automatic ignition, when heat is required.
The boiler can also be started up by the
requirement of a hot water tank.
The boiler output can be controlled by set up
values and adjusted to local conditions.
The boiler control prevents too low boiler
temperatures to avoid effect on the durability of
the system. Too high boiler temperatures are not
permissible.
Expansion cracks at insulating plates, respectively
burning chamber stones, don´t affect their
capacities and don´t represent warranty claim.
6.5
Commissioning
The commissioning must be carried out by HERZ
factory customer service or an authorised
specialist.
A
pressure
measurement
is
conducted
additionally after boiler has been operated with
the actual fuel for > 1 hour and a flow temperature
of 70-85 °C.
The result of the pressure measurement
represents a characterisation of the draught
during normal operation and shows, if the required
draught has been reached. If a deviation occurs,
the existing chimney has not been dimensioned
correctly or dimensioning underlying installations
have not been carried out correctly (e.g.: faulty
connections, false air inflow, too long connection
pipe) and the boiler does not operate properly.
During initial operation and commissioning the
system controls and safety devices must be
checked and the handling of the boiler as well as
the system maintenance schedule must be
explained to the operator.
The hydraulic balancing of the equipment (pipe
installation) must be carried out by an authorised
specialist company (installer). The installer is also
obliged (according to Draft documentation for all
the equipment (according to ÖNORM EN 12170),
which must be kept in the boiler room.
Summary of Contents for BioFire 1000
Page 1: ...OPERATING INSTRUCTIONS Wood chips pellets heating system BioFire 500 600 800 1000 1250 1500 ...
Page 89: ...Annex 14 89 14 ANNEX 14 1 Additional boiler module Hydraulic recommendation 1 ...
Page 90: ...14 Annex 90 Hydraulic recommendation 2 ...
Page 91: ...Annex 14 91 14 2 Solar module Program 1 ...
Page 92: ...14 Annex 92 Program 2 ...
Page 93: ...Annex 14 93 Program 3 ...
Page 94: ...14 Annex 94 Program 4 ...
Page 95: ...Annex 14 95 Program 5 ...
Page 96: ...14 Annex 96 Program 6 ...
Page 97: ...Notes 15 97 15 NOTES ...