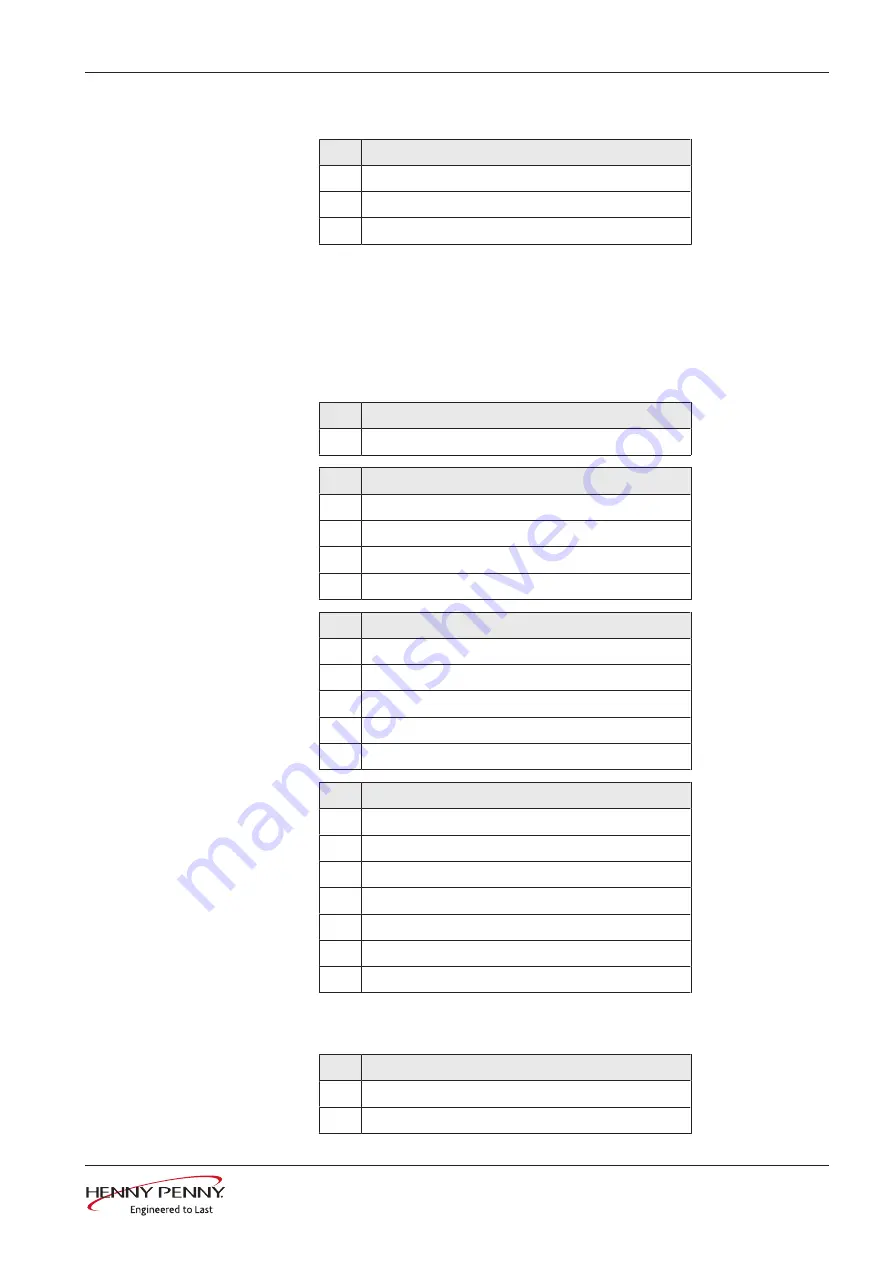
Electronics
53
Service-instructions
10.2.2 Configuration
Connector X1
No.
Description
1
Input 10.7 V AC for lighting
2
3/4
Power supply I/O board 18V AC
Connector X2, X3, X4
Not assigned
Connector X5
CAN bus line to the motor M10
Connector X6
Not assigned
Connector X7
MMI communication
Connector X8
Digital key contains device-specific information.
Connector X9 (24V DC)
No.
Description
1/2
Supply for control panel (MMI)
Connector X10 (208V AC)
No.
Description
1
Supply voltage for relay
2
Output K1, main contactor Q1
3
-
4/5
N
Connector X11 (208V AC)
optional
No.
Description
1
Output K1, POS A
2
Output K2, POS B
3
Input 208V, POS C
4
-
5
N
Connector X12 (208V AC)
No.
Description
1
Output K17, WaveClean pump G16
2
Output K3, magnetic valve K23
3
Output K4, solenoid valve K12
4
Output K5, siphon pump G24
5
Output K6, backup relay
6
-
7
N
Connector X13 (potential-
free)
Not assigned
Connector X14 (potential-
free)
No.
Description
1
Input K11, cooling fan G7 (208V AC)
2
Output K11, cooling fan G7 (208V AC)
3727002-0B-AE-12/15/2022
Summary of Contents for FlexFusion ELECTRIC SPACESAVER FSE-610
Page 6: ...Directory of contents 6 Service instructions 3727002 0B AE 12 15 2022...
Page 49: ...Software 49 Service instructions Exiting selection Tap the Back field 3727002 0B AE 12 15 2022...
Page 52: ...Electronics 52 Service instructions 10 2 Control board 10 2 1 Layout 3727002 0B AE 12 15 2022...
Page 76: ...Error messages 76 Service instructions 3727002 0B AE 12 15 2022...
Page 77: ......
Page 78: ......
Page 79: ......