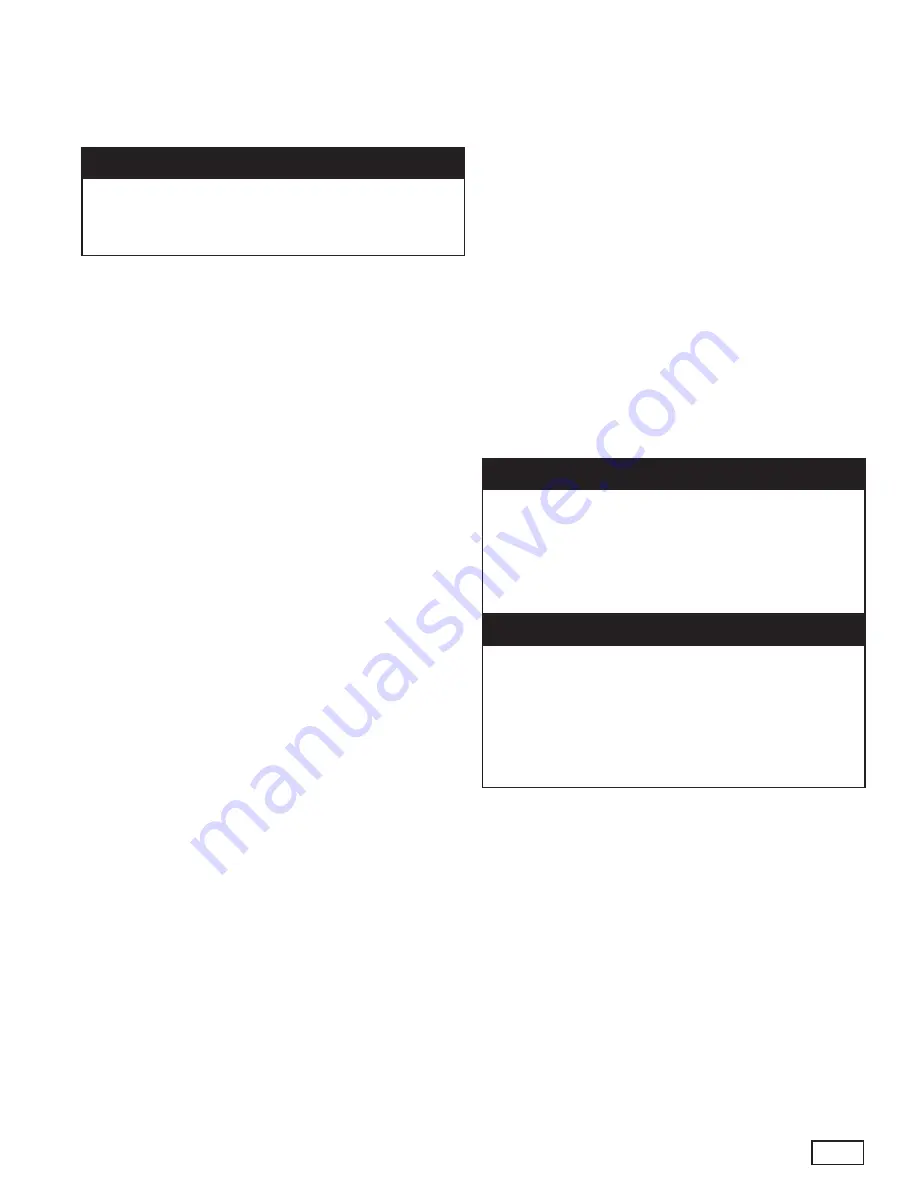
5
DO NOT use “Stop Leak” or similar chemical agent in this
system. Addition of chemicals of this type to the loop water
will foul the heat exchanger and inhibit unit operation.
CAUTION!
To avoid possible damage to a
plastic (PVC) piping system, do not allow
temperatures to exceed 11°F [45°C].
Unit and System Checkout
BEFORE POWERING SYSTEM, please check the following:
UNIT CHECKOUT
�
Balancing/shutoff valves: Insure that all isolation
valves are open and water control valves are wired.
�
Line voltage and wiring: Verify that voltage is within an
acceptable range for the unit and wiring and fuses/
breakers are properly sized. Verify that low voltage
wiring is complete.
�
Unit control transformer: Insure that transformer
has the properly selected voltage tap. Commercial
08-0V units are factory wired for 08V operation
unless specified otherwise.
�
Entering water and air: Insure that entering water and
air temperatures are within operating limits of Table 7.
�
Unit fan: Manually rotate fan to verify free rotation and
insure that blower wheel is secured to the motor shaft.
Be sure to remove any shipping supports if needed.
DO NOT oil motors upon start-up. Fan motors are
pre-oiled at the factory. Check unit fan speed selection
and compare to design requirements.
�
Condensate line: Verify that condensate line is open
and properly pitched toward drain.
�
Water flow balancing: Record inlet and outlet water
temperatures for each heat pump upon startup. This
check can eliminate nuisance trip outs and high
velocity water flow that could erode heat exchangers.
�
Unit air coil and filters: Insure that filter is clean and
accessible. Clean air coil of all manufacturing oils.
�
Unit controls: Verify that CXM field selection options
are properly set.
SYSTEM CHECKOUT
�
System water temperature: Check water temperature
for proper range and also verify heating and cooling
set points for proper operation.
�
System pH: Check and adjust water pH if necessary
to maintain a level between 6 and 8.5. Proper pH
promotes longevity of hoses and fittings (see table ).
�
System flushing: Verify that all hoses are connected
end to end when flushing to insure that debris
bypasses the unit heat exchanger, water valves and
other components. Water used in the system must be
potable quality initially and clean of dirt, piping slag,
and strong chemical cleaning agents. Verify that all
air is purged from the system. Air in the system can
cause poor operation or system corrosion.
�
Cooling tower/boiler: Check equipment for proper set
points and operation.
�
Standby pumps: Verify that the standby pump is
properly installed and in operating condition.
�
System controls: Verify that system controls function
and operate in the proper sequence.
�
Low water temperature cutout: Verify that low water
temperature cut-out controls are provided for the
outdoor portion of the loop. Otherwise, operating
problems may occur.
�
System control center: Verify that the control center
and alarm panel have appropriate set points and are
operating as designed.
�
Miscellaneous: Note any questionable aspects of
the installation.
CAUTION!
Verify that ALL water control
valves are open and allow water flow prior
to engaging the compressor. Freezing of the
coax or water lines can permanently dam-
age the heat pump.
CAUTION!
To avoid equipment damage, DO
NOT leave system filled in a building without
heat during the winter unless antifreeze is
added to the water loop. Heat exchangers
never fully drain by themselves and will
freeze unless winterized with antifreeze.
UNIT AND SYSTEM CHECKOUT
Unit Start-up Procedure
1. Turn the thermostat fan position to “ON.” Blower
should start.
. Balance air flow at registers.
. Adjust all valves to their full open position. Turn on the
line power to all heat pump units.
4. Room temperature should be within the minimum-
maximum ranges of table 7. During start-up checks,
loop water temperature entering the heat pump
should be between 60°F [16°C] and 5°F [5°C].
UNIT START-UP
UNIT STARTING AND OPERATING CONDITIONS
�
CAUTION!
�
�
CAUTION!
�
�
CAUTION!
�