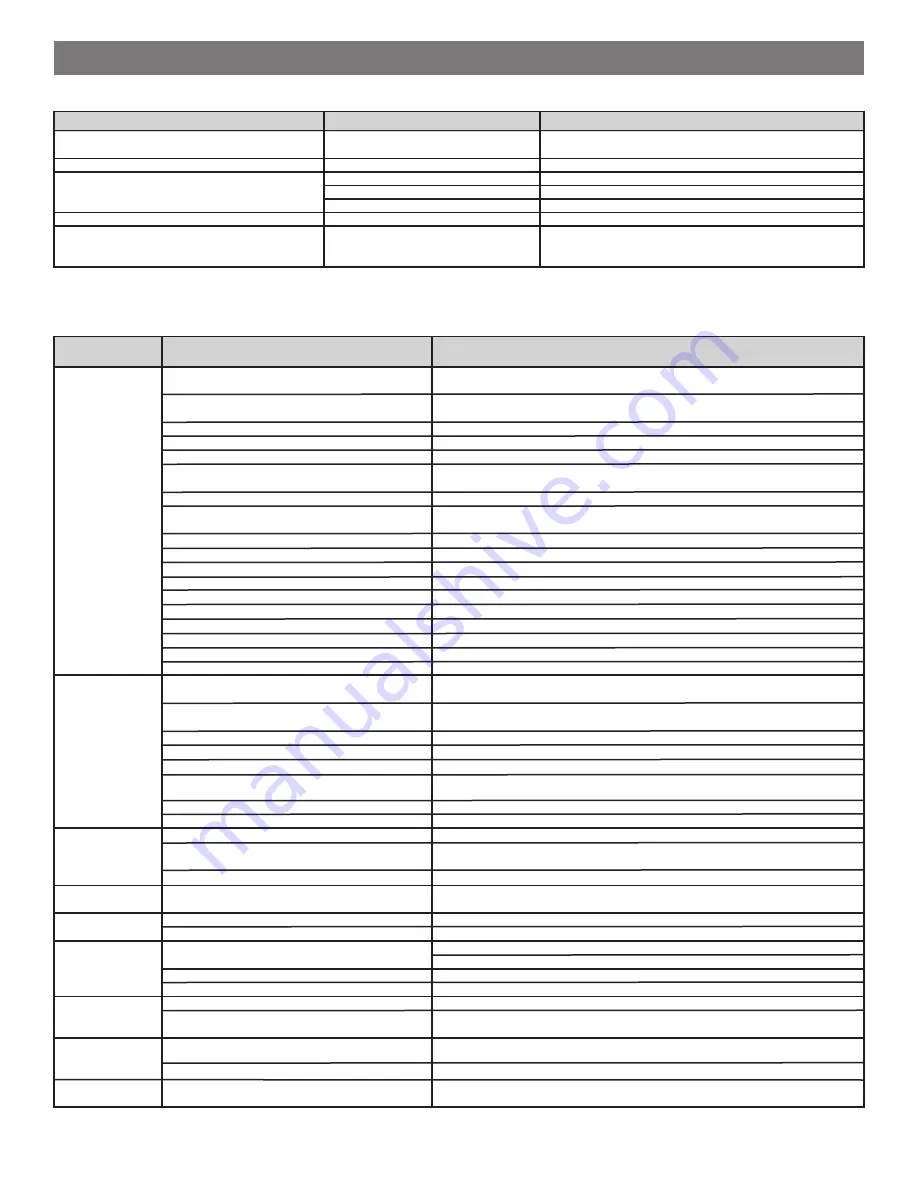
Troubleshooting Guide
36
Unit 2 MKIII
November 2005
Problem
Connector Missing
Probable Cause
Piece was not secured at stud and was car-
ried up inside of a foil.
Solution
Check for missing connector inside of foil extrusions. If connector is
not inside extrusion call Harken for a special split top connector.
Too many strung on wire.
Leave extra connector loose inside last 7’ (2.13 m) foil.
Swage stud is bent
Dirt or burrs in foil or on connector.
Return stay to distributor.
Do not attempt to straighten swage.
Clean connector and foil. Deburr as needed.
Dirt or burrs in foil or on connector
Connectors too tight on wire.
Clean connector and foil. Deburr as needed.
Tape connectors again leaving 1" (25 mm) between connectors.
Stay is too short.
Add a toggle to the headstay to increase length.
Do not sail
with
colored portion or more than 2
1
/
4
" (57 mm) of threads exposed.
Warning color shows on threads at turnbuckle when rig
is tuned or more than 2" (51 mm) of thread is exposed at
the top or bottom of the turnbuckle.
Connector will not fit into foil extrusions.
Foil will not slip past threaded stud.
Too many connectors
Sail will not go up.
Sail will not
come down.
Ultravoilet cover rolls
up inside of sail.
Sail will not raise
completely or luff
will not tension.
Sail does not stay
furled.
Headstay rotates in
jerks or elliptically.
Sail will not furl
completely.
Sail will not unfurl or
will not unfurl com-
pletely.
Sail will not furl or is
difficult to furl.
Rerun line.
Luff completely before furling or reefing.
Secure spare halyards away from the furling headstay, possibly by flipping halyards behind
spreaders
Solution
Probable Cause
Problem
Angle between headstay and halyard is too shallow and must be optimized per the installation
instructions.
Clean groove.
Check luff tape size.
Flake sail more loosely on deck.
Check luff tape for fraying.
Foil is too short or low and must be lengthened or raised.
Luff of sail is too long and must be recut.
Maintain drag on sheets while furling.
Remove sheets. Pull line to remove all furling line from drum. Turn stay to rewind line on
drum in opposite direction. Line guard and cowling alignment may need to be adjusted.
Halyard must be routed from a point higher on the mast. This may require that any halyard
turning blocks aloft be replaced or the sail shortened.
Secure furling line.
Tighten headstay and/or backstay to eliminate sag in headstay.
Move halyards away from furling headsail as above.
Adjust amount of line on drum or change position of forward block to allow line to roll evenly
on drum.
Remove sheets. Rotate stay, wrapping as much furling line on drum as possible.
Free furling line.
Lower until 2" (51 mm) from pin or until clear.
Secure spare halyards away from the furling headstay, possibly by flipping halyards behind
spreaders
See installation instructions regarding optimal halyard angle.
Flush bearings with fresh water and lubricate with dry spray lubricant such as McLube®.
Raise foils per Assembly Step 9.
Ease jib halyard.
See installation instructions regarding optimal halyard angle. It may be necessary to mount a
halyard restrainer on the front of your mast to hold the halyard to the rear.
Remount swivel corretly.
Free jib sheets.
Reinstall foil in torque tube and tighten clamp.
Flush bearings with fresh water and lubricate with dry spray lubricant such as McLube®.
Halyard is wrapping on headstay.
Sail catching at prefeeder.
Dirt in groove.
Luff tape will not go into groove.
Halyard swivel off foil.
Halyard swivel is hitting end stop.
Sail not furled tightly on stay.
Furling line is wrapped on drum in wrong direction.
Angle between halyard and mast is too sharp and
halyard is pulling too much to the rear.
Furling line not secure.
Insufficient tension on headstay.
Spare halyard catching in sail as it furls.
Too much line on drum.
Insufficient furling line on drum.
Furling line is not free.
Foils too high, binding on swage eye.
Spare halyard is wrapping in sail as it furls.
Jib halyard is wrapping around the headstay because the
halyard swivel is too low.
Salt or dirt in bearings.
Foils riding on locking collar.
Jib halyard is too tight.
Jib halyard is wrapping around headstay because angle
between mast and halyard is too shallow.
Halyard swivel installed upside down.
Jib sheets are not free.
Foil out of torque tube.
Salt or dirt in bearings.
Line through 019 backwards.
Sail full of wind.
Spare halyard is wrapping in sail as it furls.
Tighten line guard assembly screws securely.
Consult professional rigger.
Lower until 2" (51 mm) from pin or until clear.
Lineguard assembly has slipped down.
Bent or “banana" swage stud.
Foils too high, binding on swage eye.
Remove sheets. Rotate stay wrapping as much furling line on the drum as possible.
Make sure knot is pushed up inside drum.
Raise foils per Assembly Step 9.
Replace three screws holding torque tube to drum.
Overrides are best prevented by using a 019 Little Hexaratchet block as the last furling line
lead to maintain proper drag on line while unfurling.
Ease jib halyard.
Torque tube loose from drum.
Furling line tangled in drum.
Jib halyard is too tight.
No wraps of furling line on drum.
Stop knot catching.
Foils riding on locking collar.
See installation instructions regarding optimal halyard swivel height. A wire pendant may be
needed at the head of the sail to raise the halyard swivel to the proper height.
Jib halyard is wrapping around the headstay because the
halyard swivel is too low.
See installation instructions regarding optimal halyard angle. It may be necessary to mount a
halyard restrainer on the front of your mast to hold the halyard to the rear.
Jib halyard is wrapping around headstay because angle
between mast and and halyard is too shallow
Operation
Assembly