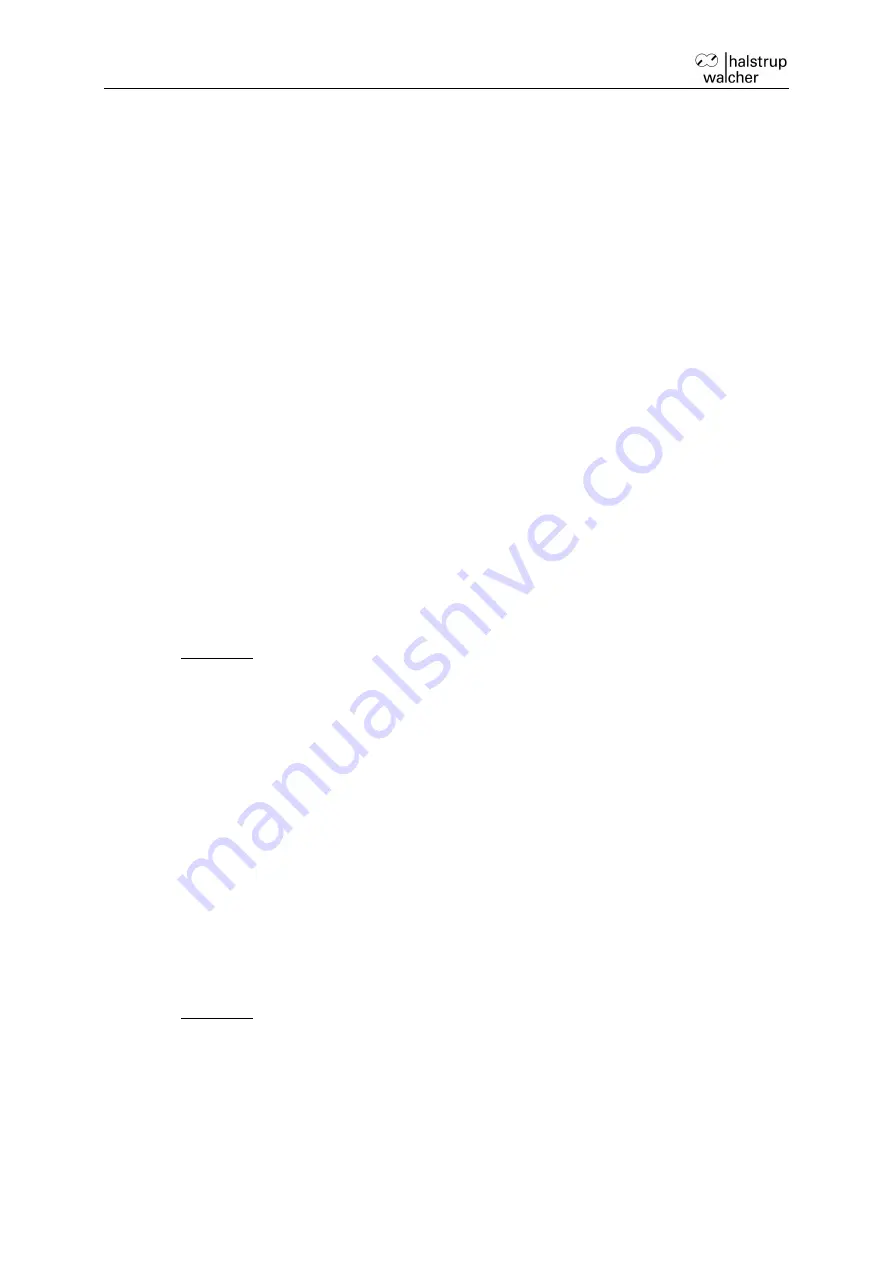
Instruction Manual PSE2xxDN
26
1) Directly, by writing the referencing value to attr. 4.
2) Indirectly, by writing an actual value to attr. 3. This makes it possible to assign any
“true” actual value to the current, physical actual value. The resulting difference is
then the referencing value. This value will immediately be included in calculations
for each transferred value and can also be read via attr. 4.
When changing the referencing value, automatically the target value, the actual value
and and the upper and lower limit are re-calculated.
d) Internal measuring system (applys fo
r “multiturn” variants)
The multiturn variants of the PSE2xxDN actuator include an absolute measuring
system with measurement range of 68 rotations. This allows the user to determine the
direction of rotation for any desired portion of these 68 rotations.
The mapping of the desired positioning range to the physical positioning range is
done with the help of the parameter ‘upper mapping end’ (attr. 40).
In the delivery state, the drive is at position 13600, the upper limit switch is set to
26400 and the lower limit switch is set to 800, yielding a positioning range of ±32
rotations (±128
00 increments). So if the desired positioning range doesn’t exceed ±32
rotations, in delivery state none of the following actions to adjust the positioning range
have to be taken.
For the realization of any desired positioning range independent of the possible
positioning range which is defined by the mounting situation (physical positioning
range) there are the following two possibilities:
1) Move the axle (for example a spindle) to the desired position, then move the drive
(with opened collar) to the position value which belongs to the physical position of
the axle, only then close the collar.
Examples:
a) Move the axle in middle position, then move the drive at no-load (with opened
collar) also to middle position (position 13600), then close the collar. The drive
is now capable of moving 32 rotations (±12800 increments by default) in each
direction.
b) Move the axle completely to the left (resp. bottom), then move the drive at no-
load (with opened collar) without loop to the lowest position (position 800), then
close the collar. The drive is now capable of moving 64 rotations (±25600
increments by default) to the right (resp. top).
c) Move the axle completely to the right (resp. top), then move the drive at no-load
(with opened collar) to the highest position (position 26400), then close the
collar. The drive is now capable of moving 64 rotations (±25600 increments by
default) to the left (resp. bottom).
2) Mount the drive in any position on the axle, close the collar, then adjust the
positioning range with the help of attr. 40. Attr. 40 defines the upper end of the
positioning range. By default, the upper end is at +68 rotations (position 27200). If
the positioning range doesn
’t suit to the actual displayed position after mounting
the drive, the upper end of the positioning range can be adjusted between -68
rotations and +136 rotations.
Examples:
a) After mounting the drive, the displayed position is 13600 (which corresponds
the delivery state). But the positioning range shall solely spread to the right
(resp. top)
Set attr. 40 to 40000.
b) After mounting the drive, the displayed position is 26400. But the positioning
range shall solely spread to the right (resp. top)
Set attr. 40 to 52800.
c) After mounting the drive, the displayed position is 800. But the positioning range
shall solely spread to the left (resp. bottom)
Set attr. 40 to 1600.