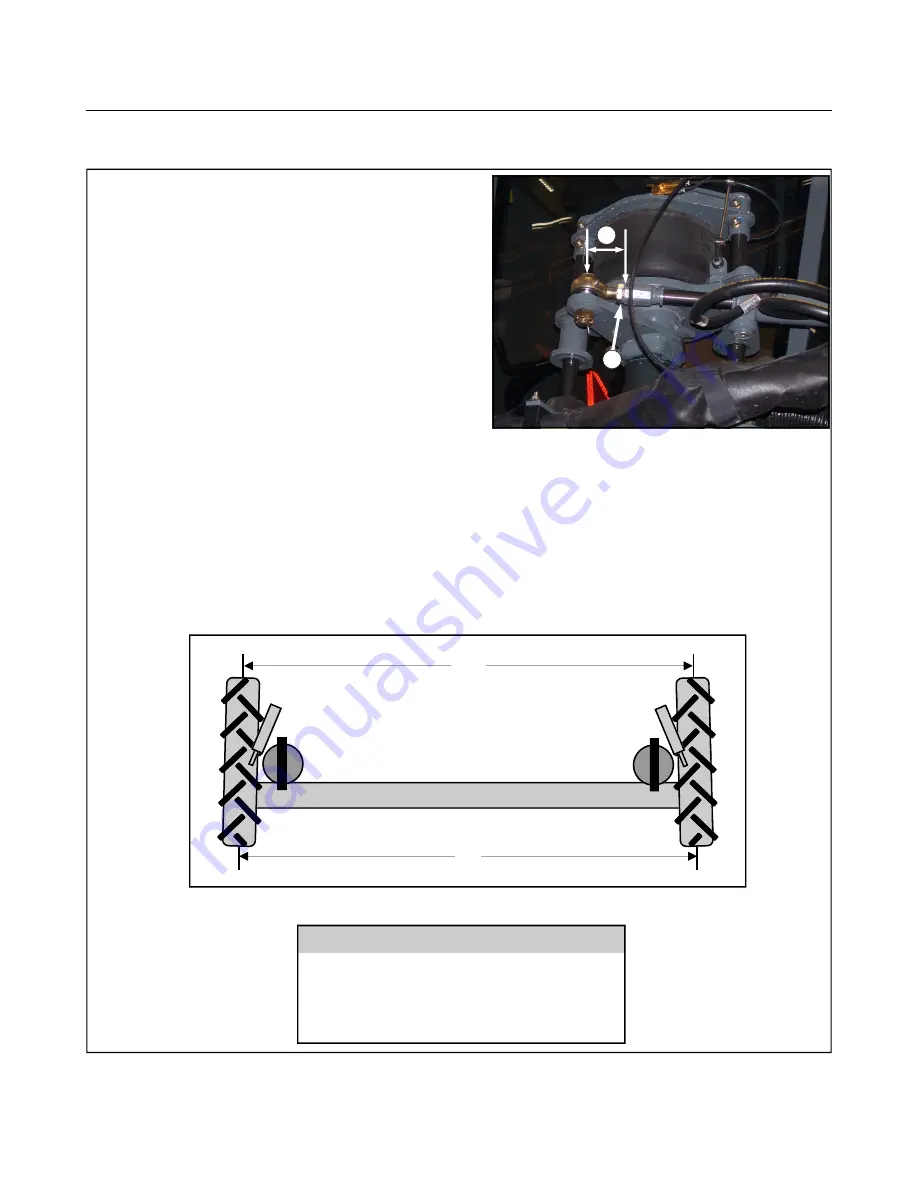
VII.
SERVICE AND MAINTENANCE
H. TOE– IN
130
TOE-IN ADJUSTMENT–
To adjust toe-in of the front
tires follow these instructions for both front steering cylin-
ders carefully:
1. Phase the cylinders (page 41), stopping at “center” .
2. Loosen jam nut (fig. 130-A).
3. Screw swivel assembly in or out on steering cylinder
until the measurement from the center of the rod end to
the collar (fig. 130-1, item B) is the same on both of the
front steering cylinders.
4. Tighten jam nut.
5. Phase cylinders again, re-check toe-in measurement. The cylinders must be phased anytime an adjust-
ment is made to the cylinders.
6. Drive forward 30 to 50 feet and re-measure toe-in.
7. Repeat steps 2-6 until a correct toe-in measurement is reached.
FIG 130-2
A
B
NOTE:
Dimension “A” should be ½" to ¾" less than
dimension “B.” For more information
regarding toe-in, see page 129.
FIG 130-1
A
B