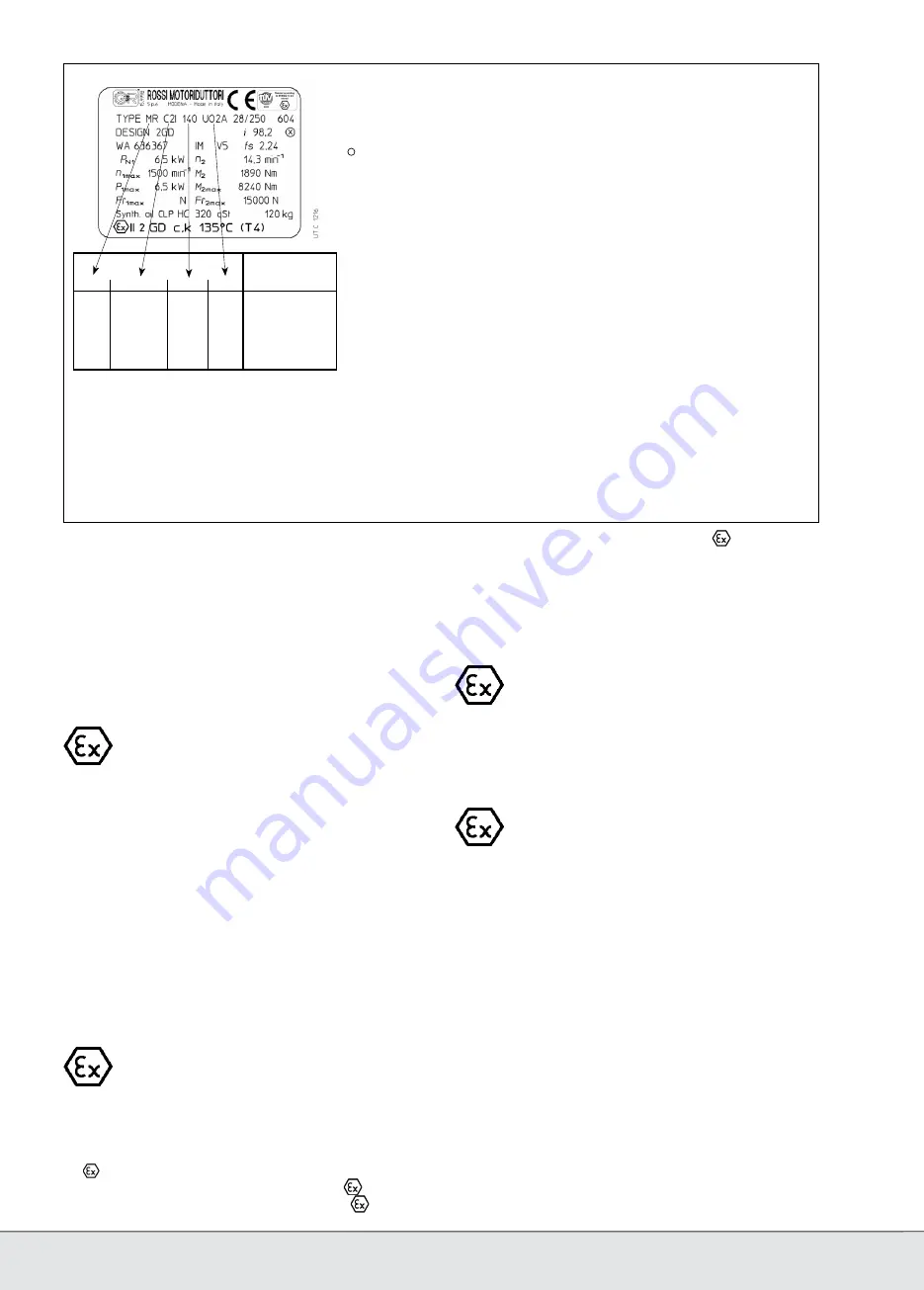
22
ROSSI
GEARMOTORS
UT.D 123 rev. 3
motor
(standard, brake or non-standard motor) consult the attached
specific documentation. If necessary, require it.
When operating on gear reducer (gearmotor) or on components con-
nected to it
the machine must be at rest:
disconnect motor (including
auxiliary equipments) from power supply, gear reducer from load, be
sure that safety systems are on against any accidental starting and,
if necessary, pre-arrange mechanical locking devices (to be removed
before commissioning).
For whatever operation (assembling, disassembling, cleanness, main-
tenance) use tools and procedures which will not cause explosion
(e.g.: sparks). When using electric equipment (portable working lights,
vacuum cleaner, etc.) be sure that they are cer tified according to ATEX
directive and suitable to the area.
Attention!
Always wait that the gear reducer or the gearmotor to cool
before carrying out any operations.
If deviations from normal operation occur (temperature
increase, unusual noise, etc.) immediately switch off the
machine.
Whenever the gear reducer/gearmotor is disassembled, moved and
mounted to another installation, check whether it is compatible with the
new installation and classification of the area, as well as its suitability
for the envisaged service as indicated by the service specifications (
f
s,
radial loads, etc.): the requested
f
s must be determined basing on par.
5.6.
When a bearing lubrication pump is present ("P" code stated on name
plate, see DESIGN) it is necessary
to avoid
input speeds lower than n
1
=
355 min
-1
, consult us if need may be.
Important:
the products relevant to this handbook correspond to the
technical level reached at the moment the handbook is printed. ROSSI
MOTORIDUTTORI reserves the right to introduce, without notice, any
necessary changes which improve product performance.
This handbook of
«Installation and maintenance instructions for gear
reducers and gearmotors according to the directive ATEX 94/9/EC»,
and its enclosures, if any, must be kept close to the gear reducer or
gearmotor in order to be easily consulted.
2 - Operating conditions
Gear reducers are designed according to name plate
data, for industrial applications with no vibration (permis-
sible vibration speed: see ch. 5), nuclear radiation and
magnetic field at ambient temperature -20
+40 °C, air
speed
1,25 [m/s], maximum altitude 1 000 [m], max humidity 80%
and can be used in aggressive environments having explosion danger
classifiable according to the definition given by the directive ATEX 99/92/
EC:
– for zone 1, 2, 21, 22 gear reducer (gearmotor without motor)
II 2 GD c, k
;
– for zone 2, 22 gear reducer (gearmotor without motor)
II 3 GD c, k;
– for zone 1, 2 gear reducer (gearmotor without motor)
II 2 G c, k
In case of different ambient conditions, consult us.
The specific mark relevant to explosion protection
is to be comple-
ted with following data:
–
maximum surface temperature and temperature class
;
or
–
maximum surface temperature;
or
– symbol
“X”
followed by
the identification code of technical docu-
ment
to be referred to concerning running conditions.
Running conditions must not exceed the limits stated on
the name plate and those of the documentation enclo-
sed, if any.
3 - How supplied
3.1 - Receipt
At receipt
verify
that the unit corresponds to the one ordered and
has
not been damaged during the transport
; in case of non-correspon-
dence (error) damages, report them immediately to the carrier.
Do not commission gear reducers and gearmotors that
are
even slightly
damaged or not suitable
for the intended
use: in this case consult ROSSI MOTORIDUTTORI.
3.2 - Name plate
Every gear reducer presents a name plate in anodised aluminium con-
taining main technical information relevant to operating and constructive
specifications and defining, according to contractual agreements, the
application limits (see fig. 1); the name plate must not be removed and
must be kept integral and readable. All name plate data must be speci-
fied on eventual spare part orders.
Attention!
For the mass stated on name plate remind that:
– it does not consider the lubricant mass;
– it is the maximum one for the gear reducer size, therefore the actual
one can be lower as it depends from train of gears and transmission
ratio;
– for the gearmotors the mass is always the same of gearmotor without
motor, therefore consider also the mass of motor stated on relevant
name plate in order to know the total mass.
In view of above mentioned points, if it is necessary to know the
exact
mass
, consult ROSSI MOTORIDUTTORI.
3.3 - Painting
Products are painted according to the painting table (see ch. 10)
including also specification as to resistance to chemical agents.
In order not to affect the protection coat of external paint, avoid dama-
ges to it both from a mechanical (ex. scratch), chemical (ex. aggressive
acids) a thermal point of view (ex. sparks).
3.4 - Protections and packing
Overhanging free shaft ends and hollow shafts are treated with pro-
tective anti-rust long life oil and protected with a plastic (polyethyl ene)
NOTE
:
F
r1max
and F
r2max
have been determined for life L
H10
according to
ISO 281.
Depending on the direction of rotation and the angular position
of the load, F
r1
and F
r2
radial loads may be much higher than the
values of F
r1max
and F
r2max
stated on the name plate; if necessary
consult ROSSI MOTORIDUTTORI.
An axial load up to 0,2 times the radial load is admitted; for higher
values consult ROSSI MOTORIDUTTORI.
Fig. 1: for more information, consult ROSSI MOTORIDUTTORI.
Designation
Series
Machine
Train of gears
Sizes Design
R, MR
V, IV, 2IV
0
32 ... 250 UO ...
A04 - worm
R, MR
2I, 3I
0
50 ... 180 UC ...
E04 - coaxial
R, MR
I, 2I, 3I, 4I
0
40 ... 360 UP ...
G05 - parallel shaft
R, MR
CI, ICI, C2I, C3I
0
40 ... 360 UO ...
G05 - right angle shaft
R,
2I, 3I, 4I
400 ... 631 UP ...
H02 - parallel shaft
R,
CI, C2I, C3I
400 ... 631 UO ...
H02 - right angle shaft
Legend
TYPE:
designation of gear reducer or gearmotor - Ø motor shaft Ø flange gear motor-
two months period and year of manufacturing;
DESIGN: ATEX codes and non-standard designs or accessories; the letter "P" states the
presence of bearing lubrication pump;
:
if marked with X install the necessary probes and/or thermostats
:
mounting position as per SPT scheme attached to UT.D 123. Connections as
indicated in ch.16, 17 and 18.
WA:
ROSSI MOTORIDUTTORI code (work assembly number);
IM:
mounting position (when "spec." is present, it means that it concerns a gear
reducer with plugs for special (inclined) mounting position
P
N1
:
nominal power relating to high speed shaft (input) at n
1max
.
n
2
:
speed at low speed shaft (gearmotor): stated only when supplying gear-
motor with motor.
n
1max
:
maximum permissible input speed (always
1 500 min
-1
);
fs:
service factor fs= P
N1
/P
motor
stated only when a complete gearmotor with motor is supplied;
M
2
:
low speed shaft torque of gearmotor stated only when a complete gearmotor
with motor is supplied;
i:
transmission ratio;
P
1max
:
maximum permissible power at the high speed shaft, with working and effi-
cacious cooling systems, if any;
the real power to be applied is to be
determined basing on the service (overloads, running time, etc);
M
2max
:
maximum permissible momentary torque at the low speed shaft as overload
(duration
15 s);
F
r1max
:
maximum radial load permissible at the centre line of the high speed shaft end
taking into account the direction of rotation, the most unfavourable direction
of the load and n
1max
;
F
r2max
:
maximum radial load permissible at the centre line of the low speed shaft end taking
into account the direction of rotation, the most unfavourable direction of the load and
n
2max
(=n
1max
/i ).