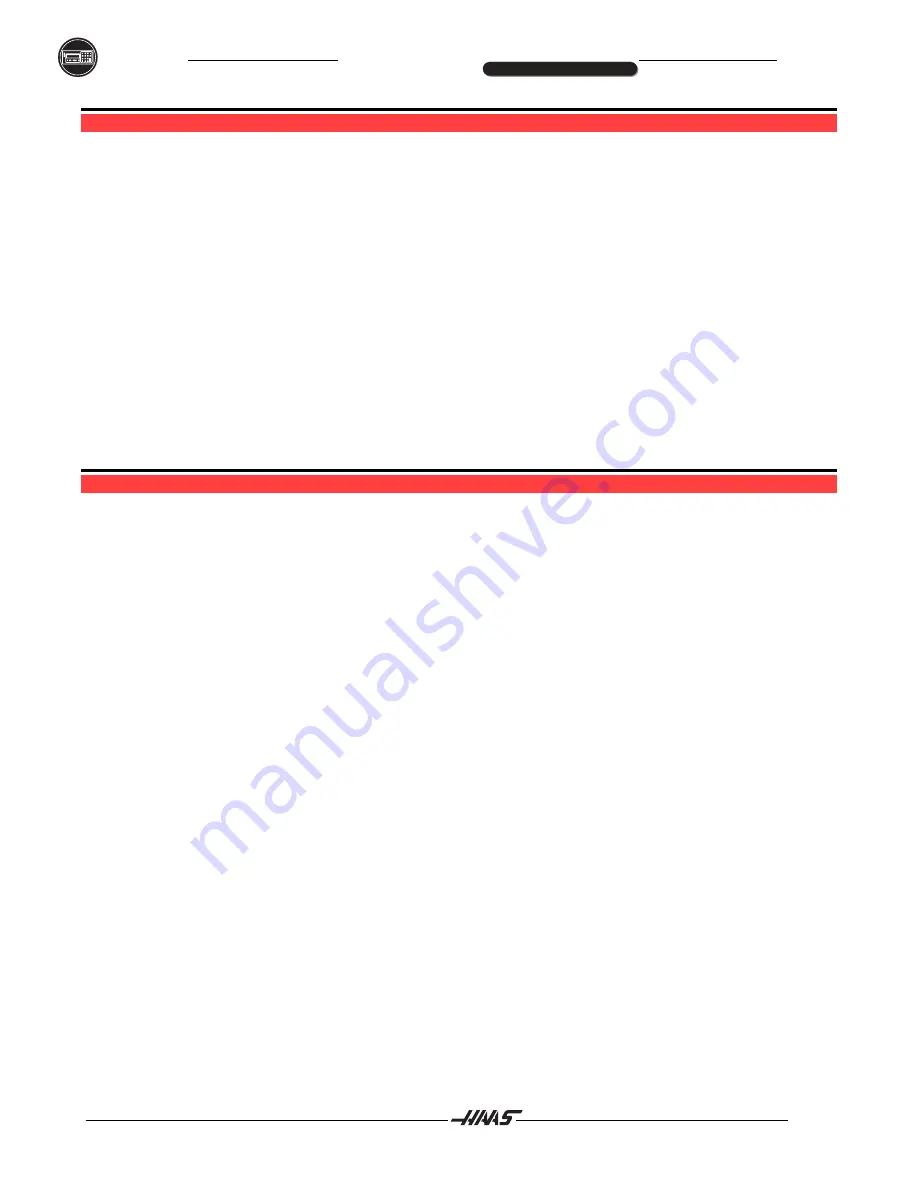
TRT
TILTING ROTARY
TABLE
TRT
O
M
PERATOR’S
ANUAL
TILTING ROTARY
TABLE
96-5048 rev E
28
June 2002
3.5 O
FFSETTING
THE
Z
ERO
P
OSITION
Use the left/right JOG switch to position the tilt indexer to the position which you want to use as zero and then
press and hold the CLR key for 3 seconds. Press the
right
arrow key to select the
B
(rotary) axis and repeat
for that axis. The displays will now show:
01
P000.000
P000.000
This indicates that the zero position is established and the controller is ready to begin normal operations. If a
different position is to be used as zero, jog the indexer to the new position and press the CLR key for 3 sec-
onds. The displays will again indicate:
01
P000.000
P000.000
If there is a zero offset defined for the indexer, the display will show a non-zero number. In this case, press the
ZERO RETURN button once more and the indexer will move forward to the predefined zero position. Press the
right
arrow key to select the
B
(rotary) axis and repeat for that axis and the lower display.
3.6 J
OGGING
Jogging of the motors can be done with the front panel JOG switch. Select which axis you wish to jog using the
right
arrow button. The selected axis,
A
or
B
, is shown by the two LED's on the front panel. The jog speed is
selected with the front panel number keys and is a fraction of the maximum feed rate set by the parameters.
The jog speeds are:
TRT 210
TRT 160
# pressed Speed % of max.
Jog speed (deg./sec.)
Jog speed (deg./sec.)
Tilt
Rotary
Tilt
Rotary
0
0.008
0.004 0.005
0.005 0.006
1
0.015
0.007 0.009
0.009 0.012
2
0.031
0.015 0.019
0.019 0.025
3
0.062
0.031 0.038
0.038 0.050
4
0.125
0.062 0.075
0.075 0.100
5
0.25 (default)
0.125 0.150
0.150 0.200
6
0.5
0.250 0.300
0.300 0.400
7
1.0
0.500 0.600
0.600 0.800
8
4.0*
2.000 2.400
2.400 3.200
9
16.0*
8.000 9.600
9.600 12.800
*
Feed rates listed are for single axis servo controls.
Last two feed rates for dual axis controls are 2% and 4% respectively.
If the control is set up for linear motion, there are both positive and negative travel limits possible. If a step is
started which would have caused the control to exceed the travel limits, the following message is shown:
2 FAr
and the control will not execute the step (See parameter 13 and 14, travel range).
OPERATION
Summary of Contents for TRT210
Page 2: ...Haas Technical Publications Manual_Archive_Safety_Pages Rev A June 6 2013...
Page 6: ...MILL WARNING DECALS Haas Technical Publications Manual_Archive_Safety_Pages Rev A June 6 2013...
Page 7: ...LATHE WARNING DECALS Haas Technical Publications Manual_Archive_Safety_Pages Rev A June 6 2013...