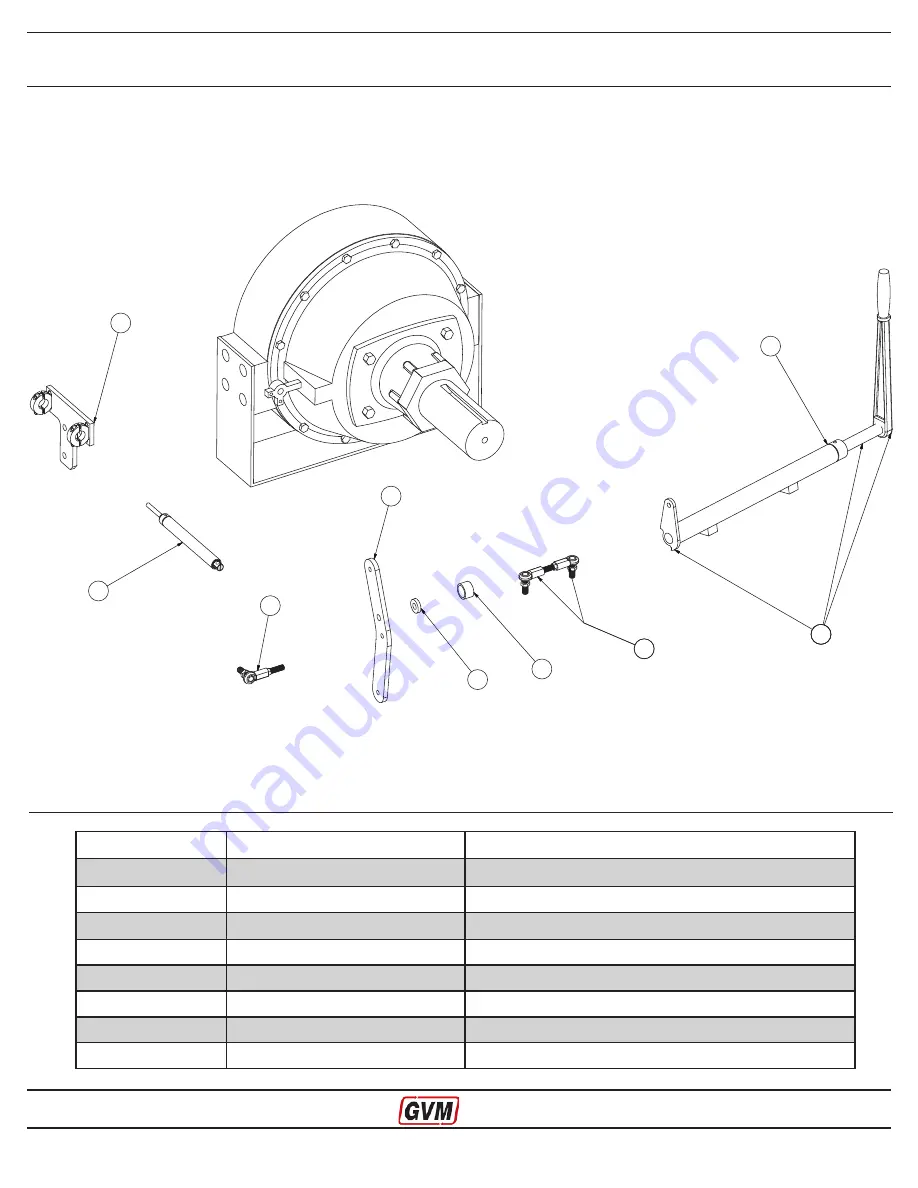
100
GVM-VAC
www.gvm-vac.com
7.4 Clutch Assist Group
Auto PTO-Cummins
ITEM #
PART NUMBER
DESCRIPTION
1
400050.A
Clutch Cylinder
2
B3.3.3164
Cylinder Support Bracket, JD
3
B3.3.3165
Clutch Bracket Arm
4
41500019
Linkage, Rod end
41500019A
Linkage, Threaded insert
5
400050.C1
Bearing
6
41500102
Pivot Shaft tube, Auto HD
7
4150041A.HD
Pivot Shaft
1
2
4
3
8
5
44
6
777
Summary of Contents for GVM6600-CM
Page 15: ...15 GVM VAC www gvm vac com SAFETY PRECAUTIONS 1 4 Safety Decals ...
Page 72: ...72 GVM VAC www gvm vac com Service Section 5 10 5 Engine Wiring Harness Detail D ...
Page 77: ...77 GVM VAC www gvm vac com Service Section 5 20 1 Hoist Hydraulic Diagram ...
Page 101: ...101 GVM VAC www gvm vac com 7 5 Kraft Fluid Drive Group Optional Fluid Drive Coupler Optional ...