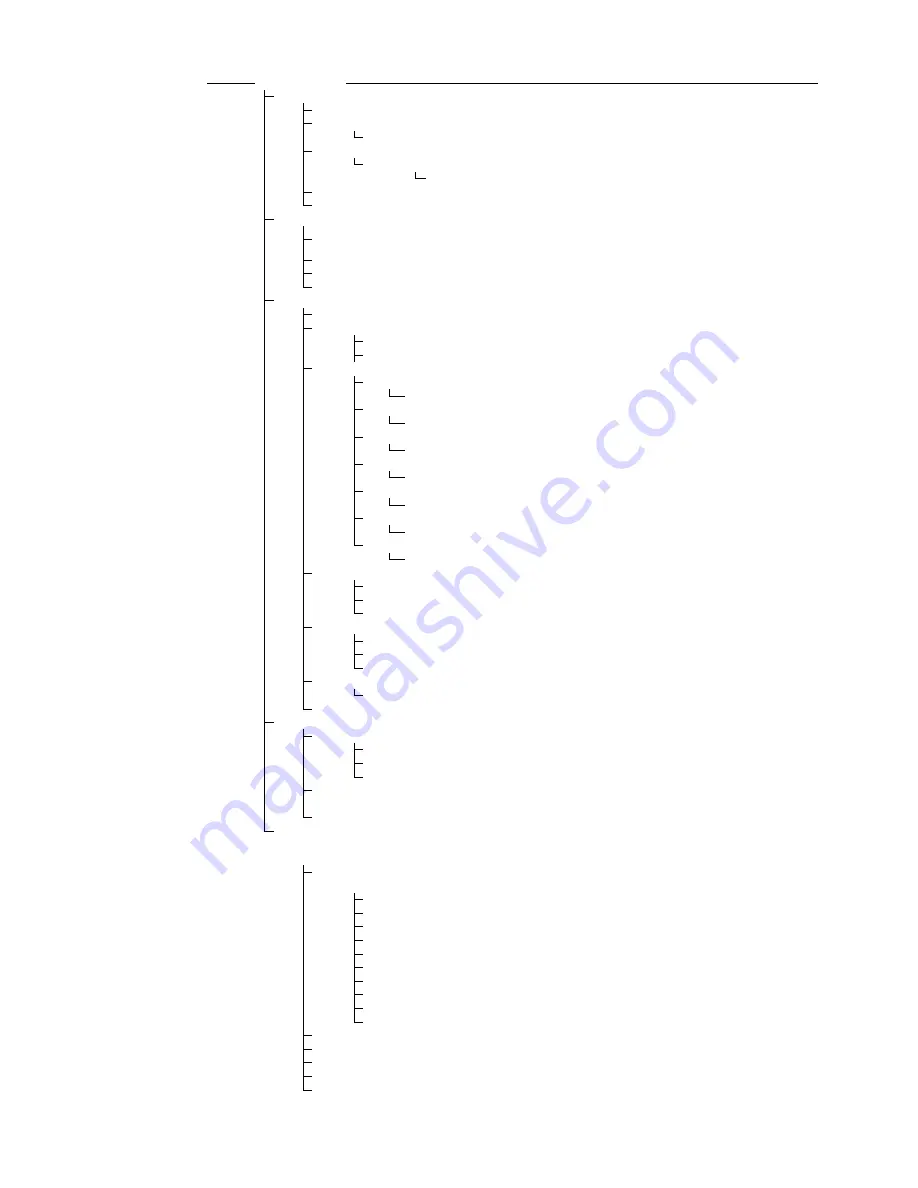
16
10.2 Overview
Continued from page 15
4. Settings
4.
Primary controller
4.1.1 PI controller
4.1.2 Alternative setpoints
4.1.2.1...4.1.2. Alternative setpoints 2...7
4.1.3 Setpoint influence
4.1.3.1 External setpoint influence
4.1.3.1 Influence function
4.1.4 Primary sensor
4.1.5 Redundant primary sensor
4.
Pump cascade control
4.2.1 Min. time between start/stop
Max. number of starts/hour
4.2.3 Standby pumps
4.2.4 Forced pump changeover
4.2.5 Test run
4.
Secondary functions
4.3.1 Low flow estimation/stop function
4.3.7 Overview of digital inputs
4.3.7.1...4.3.7. Function, DI1..DI3 (CU 351), [10, 12, 14]
4.3.7.4...4.3.7. Function, DI1..DI9 (IO 351-41), [10...46]
4.3.8 Overview of analog inputs
4.3.8.1 Setting, analog input AI1 (CU 351), [51]
4.3.8.1.
Function, AI1 (CU 351), [51]
4.3.8.2 Setting, AI2 (CU 351), [54]
4.3.8.2.
Function, AI2 (CU 351), [54]
4.3.8.3 Setting, AI3 (CU 351), [57]
4.3.8.3.
Function, AI3 (CU 351), [57]
4.3.8.4 Setting, AI1 (IO 351-41), [57]
4.3.8.4.
Function, AI1 (IO 351-41), [57]
4.3.8.5 Setting, AI2 (IO 351-41), [60]
4.3.8.5.
Function, AI2 (IO 351-41), [60]
4.3.8.6 Setting, AI1 (IO 351-42), [57]
4.3.8.6.
Function, AI1 (IO 351-42), [57]
4.3.8.7 Setting, AI2 (IO 351-42), [60]
4.3.8.7.
Function, AI2 (IO 351-42), [60]
4.3.9 Overview of digital outputs
4.3.9.1...4.3.9. Function, DO1 and DO2 (CU 351), [72, 75]
4.3.9.3...4.3.9. Function, DO1...DO7 (IO 351-41), [77...88]
4.3.9.10..4.3.9 Function, DO1...DO7 (IO 351-42), [77...88]
4.3.1 Min., max. and user-defined duty
4.3.14.1
Min. duty
4.3.14.2
Max. duty
4.3.14.3
User-defined duty
4.3.1 Pump curve data
4.3.19.1
Data, main pumps
4.3.2 Control source
4.
Monitoring functions
4.4.1 Dry-running protection
4.4.1.1 Pressure/level switch
4.4.1.2 Measurement, inlet pressure
4.4.1.3 Measurement, tank level
4.4.2 Min. pressure
4.4.3 Max. pressure
4.4.4 External fault
4.
Functions, CU 351
Change to service language (GB)
Run wizard again
4.5.1 Display language
4.5.2 Display units
4.5.2.1 Units for pressure
4.5.2.2 Units for differential pressure
4.5.2.3 Units for head
4.5.2.4 Units for level
4.5.2.5 Units for flow rate
4.5.2.6 Units for volume
4.5.2.7 Units for specific energy
4.5.2.8 Units for temperature
4.5.2.9 Units for power
4.5.2.1 Units for energy
4.5.3 Date and time
4.5.4 Password
4.5.5 Ethernet
4.5.6 GENIbus number
4.5.9 Software status
www.motralec.com / [email protected] / 01.39.97.65.10