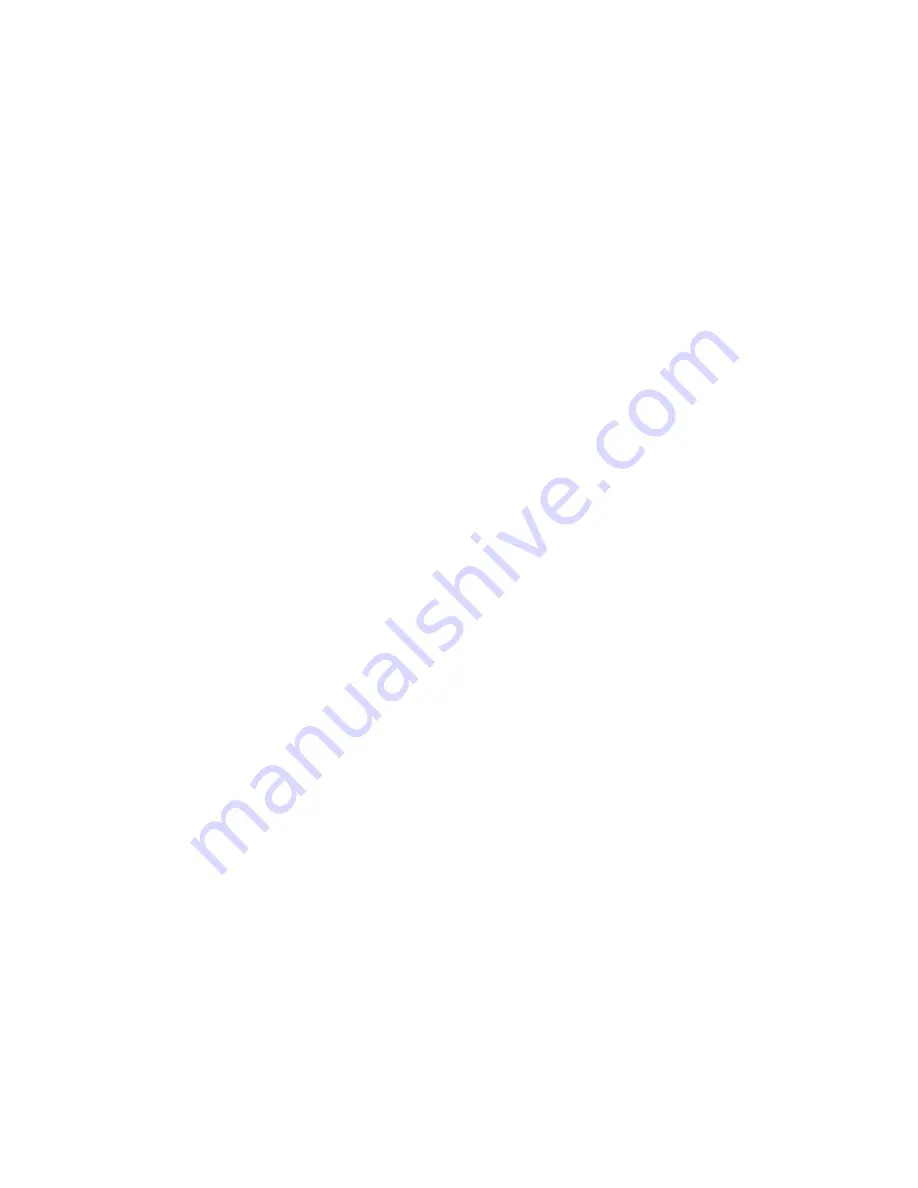
13 - 73
13.14 992000 ELECTRICAL
Promaster 200 Kohler
Installation checkout: Make sure that all switches are in
their proper position: PTO switch off, Neutral switches
activated. (T-levers centered).
Step 1:
Check out the battery. Use a hydrometer on all the
battery cells to see if one or more is bad. Also use a
voltmeter to check for proper voltage. Replace the
battery if necessary and/or charge to proper level.
Step 2:
Use a voltmeter to make sure you have power to
terminal I in the off position on the back of the key
switch. If you don’t have power to terminal I, check the
25-amp fuse or the ammeter connections, verify power
at pin 30 of your start relay.
Step 3:
With the key switch in the RUN position see that power
has been transferred to terminals A, R, and B on the
backside of the key switch. Terminal A supplies power
to hourmeter, PTO switch, and oil pressure sensor.
Terminal R brings in the charge power from the engine
to the battery. Terminal B brings in power to the
interlock relay and on to the seat switch for the holding
circuit for the time delay.
Step 4:
With the key in the START position, power is
transferred from terminal I to terminal S and on to the
start relay pin 86. Pin 85 will find ground through the
PTO switch and neutral switches allowing the relay to
activate, making power travel from pin 87 to the start
solenoid for starting. Power will also travel from pin 85
to energize the time delay module.
NOTE: The engine kill circuit is connected to pin 87A of
the interlock relay so as to kill the engine when power
is removed from the relay.
Summary of Contents for 991001-008
Page 38: ...12 38 Figure 23 LP Low Pressure HP High Pressure FFBW Fluid Both Ways ...
Page 40: ...12 40 Models 992013 014 015 016 PF2020 Figure 25 ...
Page 54: ...13 54 Promaster 100 Kohler Command 50 Deck with Lift Models 991006 ...
Page 59: ...13 59 Promaster 100 Kohler 16 18 HP ...
Page 63: ...13 63 Promaster 100 Briggs Stratton ...
Page 68: ...13 68 Model 992010 011 Briggs Stratton ...
Page 75: ...13 75 Model 992015 016 Kohler 20 HP ...