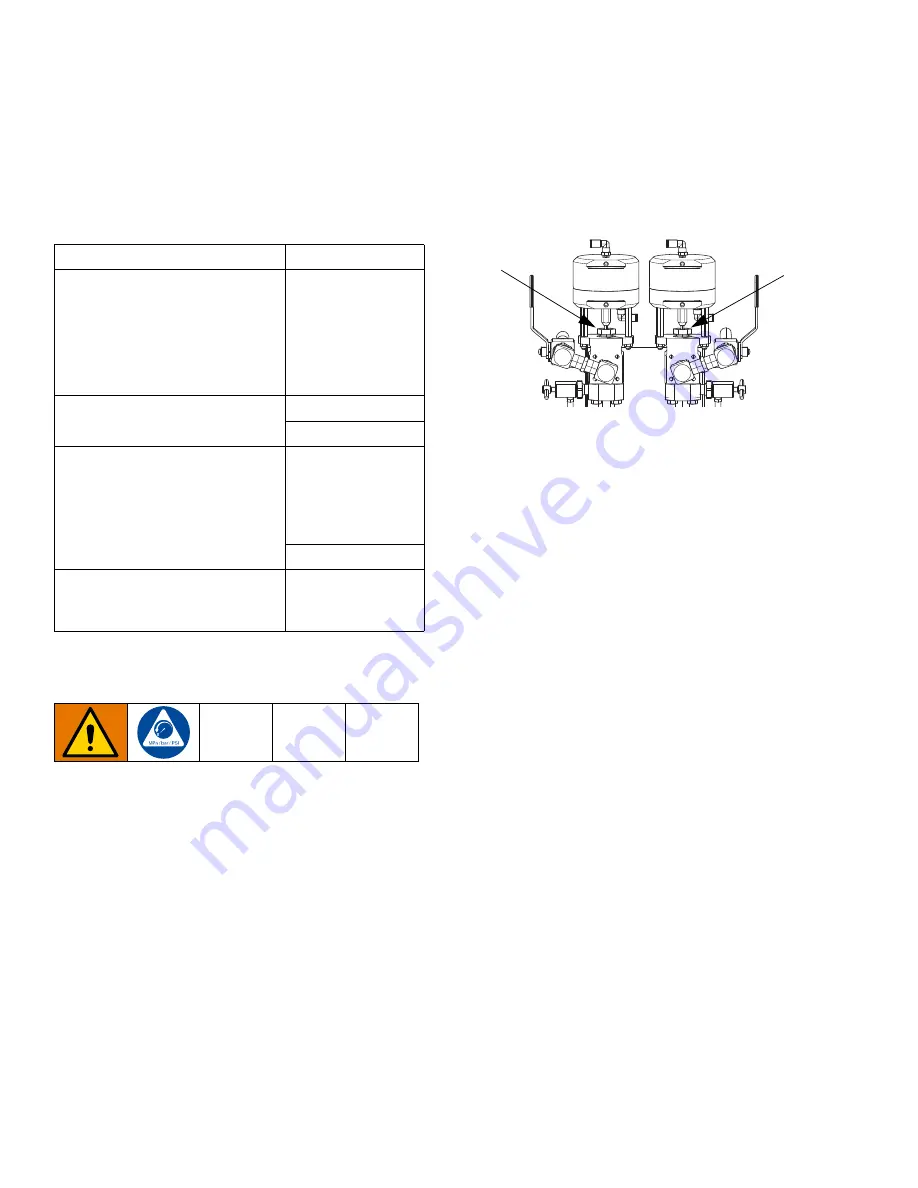
Maintenance
60
3A2776K
Maintenance
See the following table for maintenance tasks and
frequency. See the following sections for details for
each task.
Adjust Packing Nuts
NOTE:
There must be no pressure when adjusting the
packing nuts.
1.
including relieving air pressure in the tanks.
2.
Fill A and B metering pump packing nuts with throat
seal liquid (TSL
™
).
3.
After TSL is added, torque metering pump packing
nuts to 50 ft-lb (67.5 N•m). Follow instructions in
Xtreme Lowers manual 311762.
4.
Fill A and B dosing valves packing nuts with throat
seal liquid (TSL).
5.
After TSL is added, tighten dosing valve packing
nuts 1/4 turn after nut contacts packings; about
145-155 in-lb (16-18 N•m).
Filters
Once a week check, clean, and replace (if needed) the
following filters.
•
Main air inlet manifold filter; see XM PFP Repair -
Parts manual 3A2989, Replace Air Filter Element
section, for instructions.
•
Air regulator filter (5 micron) on air control
assembly; see XM PFP Repair - Parts manual
3A2989, Replace Air Filter Element section, for
instructions.
Seals
Once a week, check and tighten throat seals on
metering pumps and dosing valves. Be sure to follow
the
, page 44, prior to tightening
seals.
Battery
The front display battery must be changed in a
nonhazardous location only. See XM PFP repair manual
for instructions.
Use only Panasonic
®
CR2032 batteries for
replacement.
Frequency
Task
•
Before first use
•
After first hour of operation
•
After first day of operation
•
Whenever TSL is discolored
or has seeped over the
packing nut, and after sprayer
has been transported
Adjust packing
nuts
Weekly
Filters
Seals
As Needed
Add oil to agitator
motor lubricators.
Use 10W or
10W-30 detergent
oil.
Clean the system
Yearly or When Changing
Materials
Disassemble and
clean the A and B
material heaters.
TSL
TSL
ti20107a