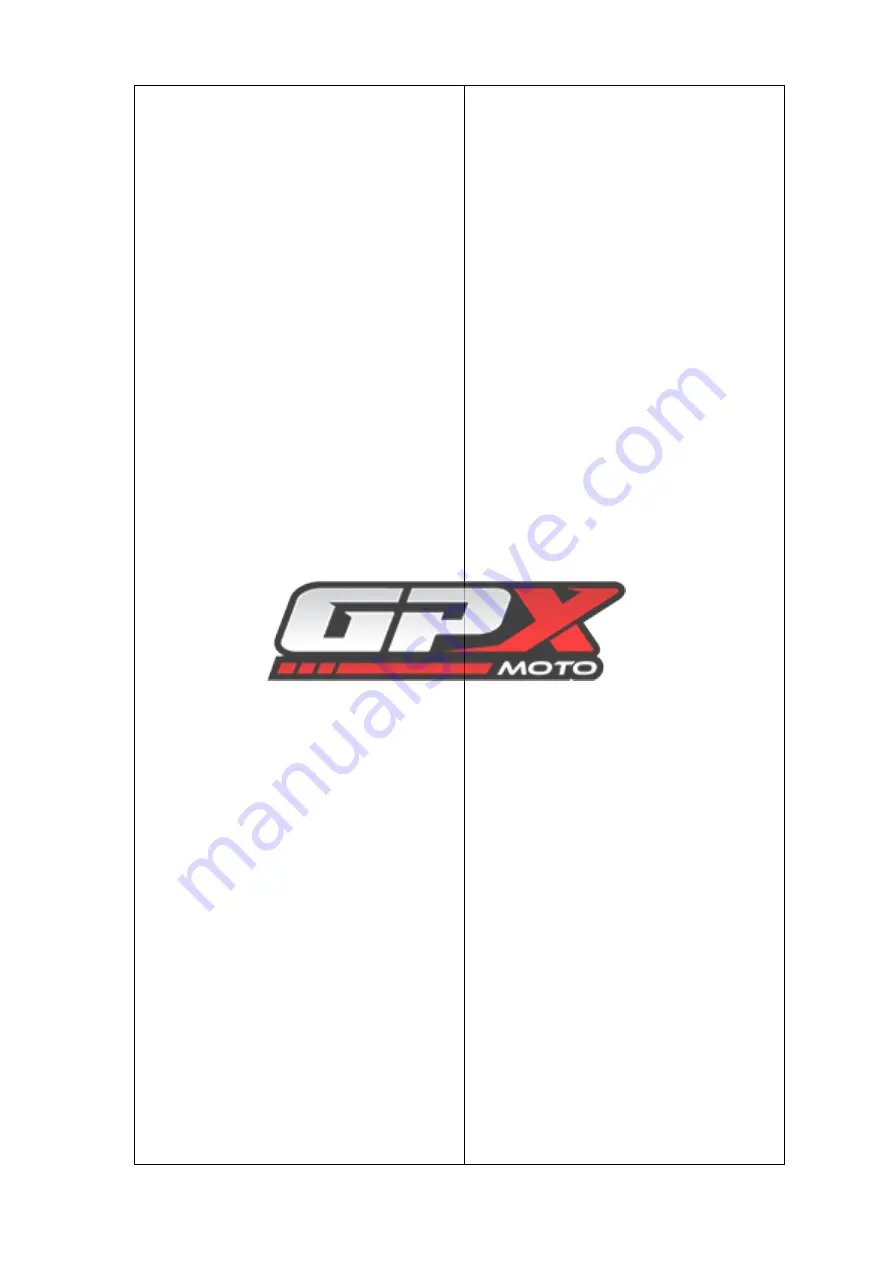
Page 1131
of the NC250 rocker shaft positioning plate to the
left front cover;
6. Take 2 pieces of bolts M6
×
10, and
fasten the NC450 timing driven sprocket on the
camshaft;
take 1 piece of the camshaft
pressure reducing valve throwing block
combination and the pressure reducing
valve
return
spring,
and
throw
the
pressure
reducing
valve
block
The
combination and pressure reducing valve
return spring is assembled on the camshaft
through the timing driven sprocket;
take
the bolt M6 × 16 and put it
into the
flat
washer, install it into the corresponding
threaded hole of the camshaft, and fasten it.
Tightening torque: 11 to 13N
·
m
.
7. Adjust the gap between the intake and
exhaust valves, the gap value of the valve: 0.07
±
0.01mm