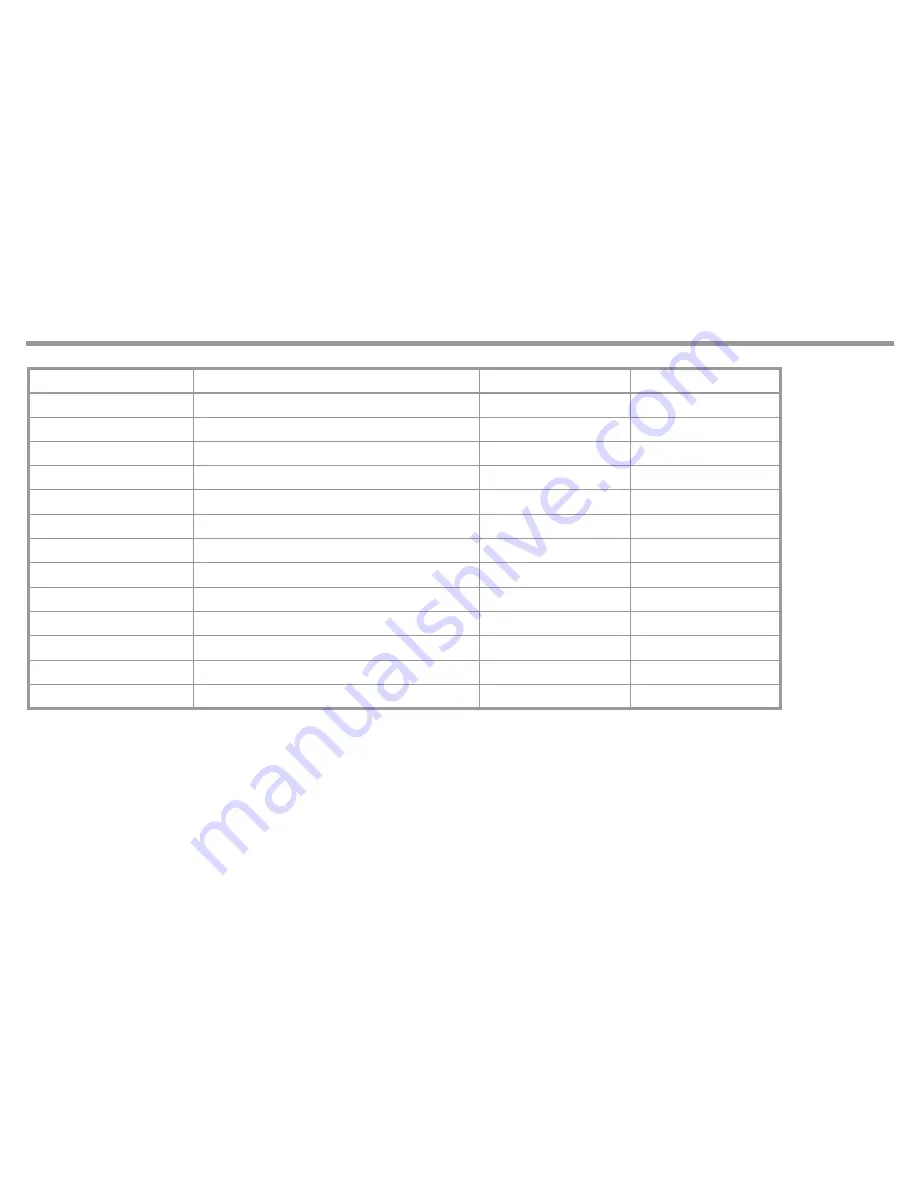
GMC-I Messtechnik GmbH
R2500–46
Channel error mask (A1M1 and A2M1)
Wert
Meaning
Display
default
0001
Broken sensor, 2
nd
input
SE H
A1
0002
Reversed polarity, 2
nd
input
SE L
A1
0004
Analog error
AE
A1
0008
Broken sensor
SE H
A1
0010
Reversed polarity
SE L
A1
0020
1
st
Lower limit value fallen short of
Blinks
A1
0040
2
nd
lower limit value fallen short of
A2
0080
1
st
upper limit value exceeded
Blinks
A1
0100
2
nd
upper limit value exceeded
A2
0200
Parameter impermissible for entry via interface
–
0800
Heating circuit error
LE
A1
1000
Self-tuning start-up error
no t
–
2000
Self-tuning error or abort
tE X
A1
Summary of Contents for R2500
Page 2: ......