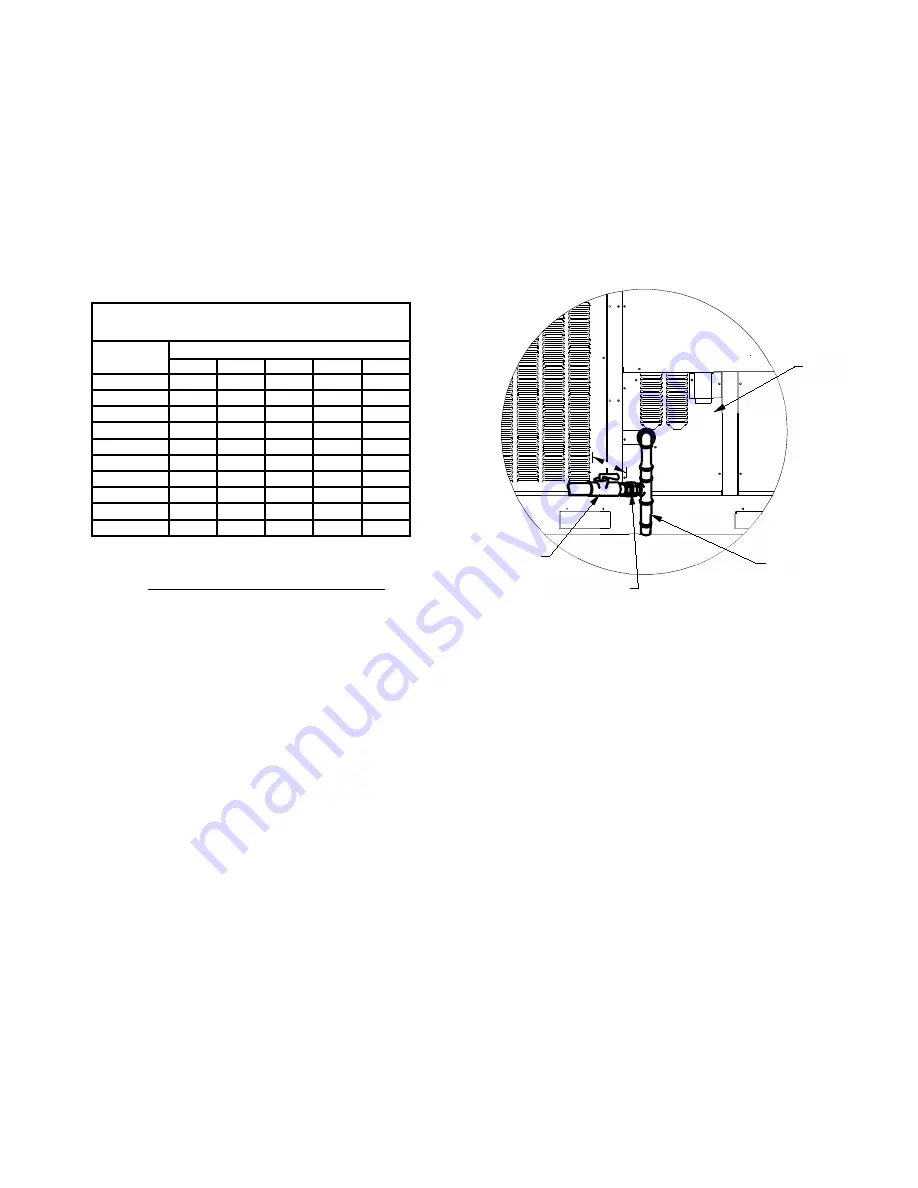
11
P
IPInG
IMPoRtant notE: t
o
avoId
PoSSIblE
UnSatISfactoRy
oPERatIon
oR
EqUIPMEnt
daMaGE
dUE
to
UndER
fIRInG
of
EqUIPMEnt
,
do
not
UndERSIZE
tHE
natURal
/
PRoPanE
GaS
PIPInG
fRoM
tHE
MEtER
/
tank
to
tHE
UnIt
.
W
HEn
SIZInG
a
tRUnk
lInE
,
InclUdE
all
aPPlIancES
on
tHat
lInE
tHat
coUld
bE
oPERatEd
SIMUltanEoUSly
.
The gas line installation must comply with local codes, or
in the absence of local codes, with the latest edition of the
National Fuel Gas Code NFPA 54 / ANSI Z223.1.
n
atURal
G
aS
c
onnEctIon
1/2
3/4
1
1 1/4
1 1 /2
10
132
278
520
1050
1600
20
92
190
350
730
1100
30
73
152
285
590
980
40
63
130
245
500
760
50
56
115
215
440
670
60
50
105
195
400
610
70
46
96
180
370
560
80
43
90
170
350
530
90
40
84
160
320
490
100
38
79
150
305
460
Pressure= .50 PSIG or less and Pressure Drop of 0.3" W.C.
(Based on 0.60 Specific Gravity Gas)
Natural Gas Capacity of Pipe
in Cubic Feet of Gas Per Hour (CFH)
Nominal Black Pipe Size (inches)
Length of
Pipe in Feet
Heating Value of Gas (BTU/Cubic Foot
CFH =
BTUH Furnace Input
Refer to the Proper Piping Practice drawing for the general
layout at the unit. The following rules apply:
1.
Use black iron pipe and fittings for the supply piping.
The use of a flex connector and/or copper piping is
permitted as long as it is in agreement with local
codes.
2. Use pipe joint compound on male threads only. Pipe
joint compound must be resistant to the action of the
fuel used.
3. Use ground joint unions.
4. Install a drip leg to trap dirt and moisture before it can
enter the gas valve. The drip leg must be a minimum
of three inches long.
5. Use two pipe wrenches when making connection to
the gas valve to keep it from turning.
6. Install a manual shut-off valve in a convenient location
(within six feet of unit) between the meter and the unit.
7. Tighten all joints securely.
8. The unit must be connected to the building piping by
one of the following methods:
•
Rigid metallic pipe and fittings
•
Semirigid metallic tubing and metallic fittings
(Aluminum alloy tubing must not be used in
exterior locations).
• Listed gas appliance connectors used in
accordance with the terms of their listing
that are completely in the same room as the
equipment. Always use a new listed connector.
• In the prior two methods above the connector
or tubing must be protected from physical
and thermal damage. Aluminum alloy tubing
and connectors must be coated to protect
against external corrosion when in contact with
masonry, plaster or insulation or are subject to
repeated wettings by liquids (water - not rain
water, detergents or sewage).
BURNER
DOOR
DRIP
LEG
MANUAL
SHUT-OFF
GROUND JOINT
UNION
TBD
P
RoPER
PIPInG
PRactIcE
notE: t
HE
UnIt
GaS
SUPPly
EntRancE
IS
factoRy
SEalEd
WItH
PlUGS
. k
EEP
PlUGS
In
PlacE
UntIl
GaS
SUPPly
IS
REady
to
bE
InStallEd
. o
ncE
REady
,
REPlacE
tHE
PlUGS
WItH
tHE
SUPPlIEd
GRoMMEtS
and
InStall
GaS
SUPPly
lInE
.