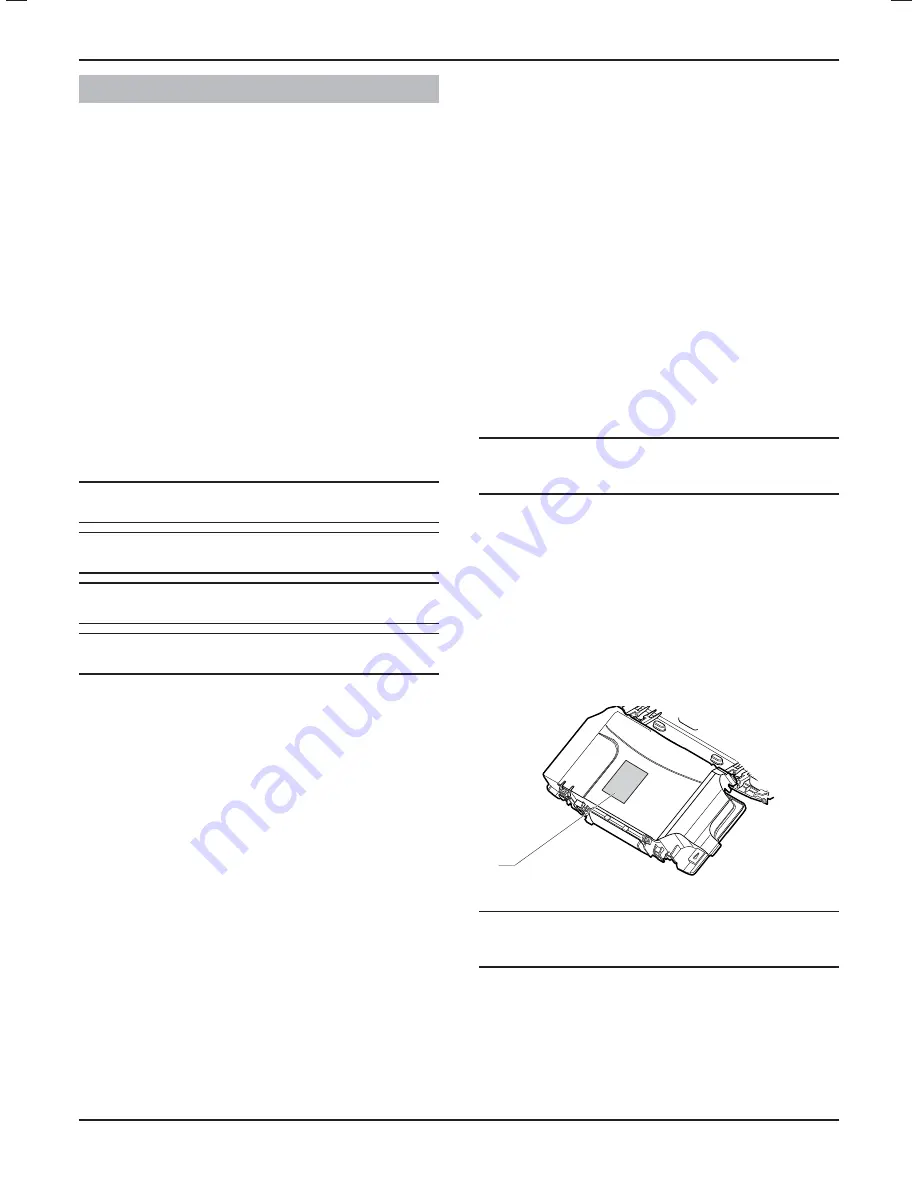
0020167175_01 - 02/13 - Glow-worm
INTRODUCTION
1 Instructions
guidance
1.1 Product
documentation
The instructions are an integral part of the appliance and must be
handed to the user on completion of the installation in order to
comply with the current regulation.
•
Carefully read the manual, to understand all the information
to enable safe installation, use and servicing. No liability can
be accepted in the event of damage for not complying with the
guidance in this instruction manual.
These instructions consist of, Installation, Servicing, Fault Finding,
Replacement of Parts and Spares. The instructions are an integral
part of the appliance and must, to comply with the current issue of
the Gas Safety (Installation and Use) Regulations, be handed to the
user on completion of the installation.
1.2
Explanation of symbols
a
DANGER:
Risk of injuries.
e
DANGER:
Risk of electric shock.
b
ATTENTION:
Risk of damage to the appliance or to its surroundings.
i
IMPORTANT:
Important information.
1.3 Guarantee
registration
Thank you for installing a new Glow-worm appliance in your home.
Glow-worm appliances are manufactured to the very
highest standard so we are pleased to o
ff
er our customers a
Comprehensive 5 years Guarantee.
We recommend you complete and return as soon as possible
your guarantee registration card. If your guarantee registration
card is missing you can obtain a copy or record your registration
by telephoning the Glow-worm Customer Service number 01773
828100.
2 Appliance
description
2.1 Safety
devices
2.1.1 Overheating
safety
The appliance is designed to recognise the potential for an
overheat lockout and will shutdown before this happens.
2.1.2 Safety
discharge
valve
A safety discharge valve and discharge pipe are
fi
tted to the
boiler. This valve must not be touched.
- The heating safety valve opens when the pressure in the
heating circuit exceeds 3 bars.
•
Should there be any discharge from the pipe, isolate the boiler
electrical supply and call your installer or Glow-worm’s own
service organisation.
2.1.3 Frost
protection
The frost protection system operates the pump to start as soon
as the temperature in the heating circuit falls below 12°C. The
pump stops as soon as the temperature of the water contained
in the heating circuit reaches 15°C. If the temperature in the
heating system falls below 7°C, the burner ignites until it reaches
35°C. The frost-protection system is active when the appliance is
switched on. The system alone cannot ensure that the installation
is protected against frost. An separate frost thermostat is
necessary to control the temperature of the system.
a
DANGER:
Your domestic water circuit (hot or cold) is not protected
by the boiler.
2.1.4
Condensate drain blockage
During freezing conditions this may be due to the forming of ice
in the condense drain external to the house. In this case, a safety
device shuts down the appliance.
2.2 Data
label
The data label certi
fi
es the country where the appliance is
intended to be installed.
Data label location:
1
Key
1 Data
label
a
DANGER:
The appliance shall only be connected to the gas type(s)
indicated on the data label.
•
Refer to chapter "Technical Data" in the technical data section
to see the de
fi
nition of the abbreviations used on the data
label.
INTRODUCTION
- 3 -
Summary of Contents for ULTIMATE 30c
Page 1: ...condens Installation and Servicing ULTIMATE 30c G C No 47 044 48 ULTIMATE 35c G C No 47 044 49...
Page 2: ......
Page 51: ...Declaration of Conformity Installation Commissioning and Service Record...
Page 52: ...a...
Page 54: ......
Page 55: ......