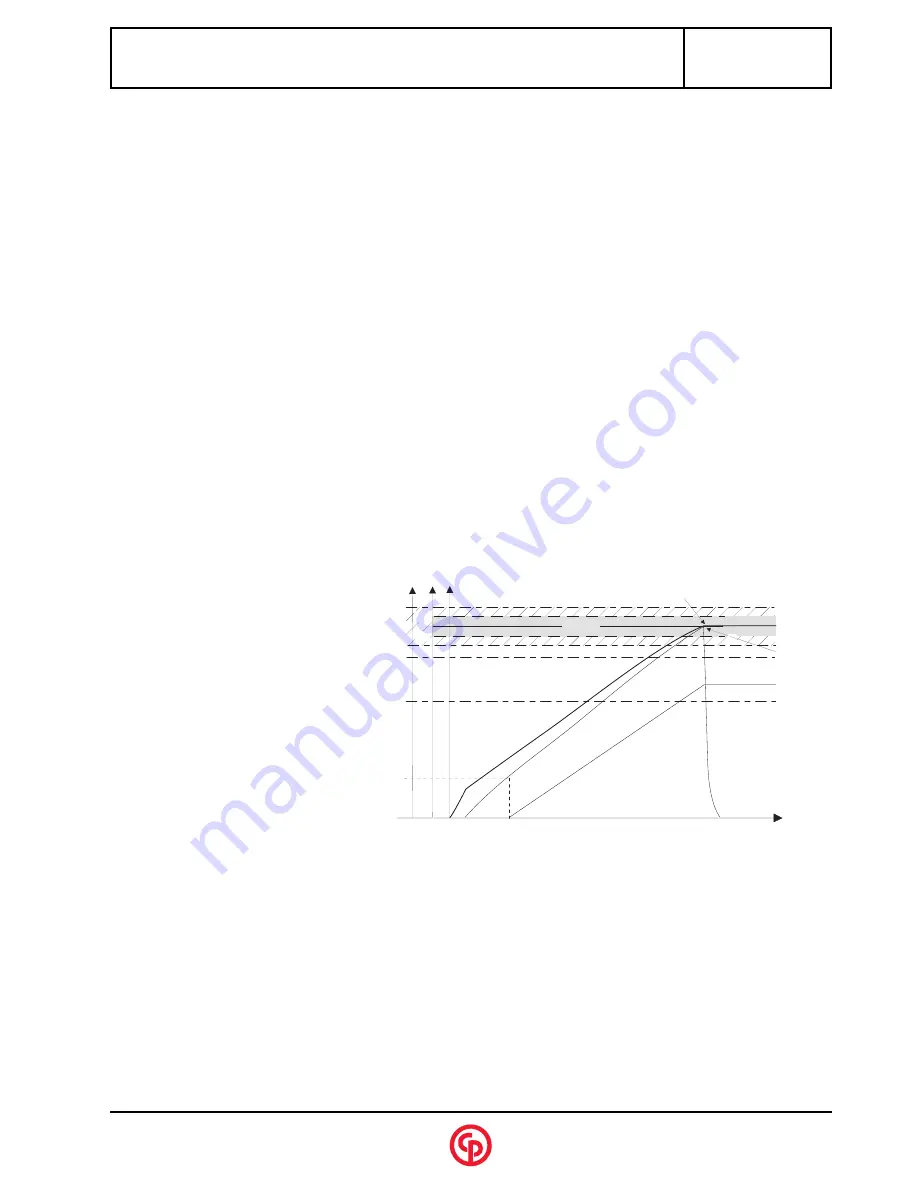
6159932410-02
English
51 / 76
TIGHTENING STRATEGIES
5 - ANGLE + TORQUE RATE CONTROLLED TIGHTENING
6 - STRATEGY INCLUDING ADDITIONAL CONTROL (CURRENT)
To make the fastening task even more reliable, it is possible to add a current control to most tightening strategies (torque,
angle, angle+torque, etc.).
This additional control enables you to check the coherence between the value of the torque measured by the torque transducer,
and the current consumed by the motor.
This "current" information varies from one tool to another and is not calibrated against the torque. It is thus necessary to establish
a similarity on an experimental basis for each tool: you must read the value of the maximum current reached at the end of a cycle
and then execute that cycle at least 3 times to define the "minimum current" and "maximum current" value to be programmed.
Spindle stop
IF
angle
≥
target angle
OR
torque > max. torque
OR
torque rate < min. torque rate
OR
torque rate > max. torque rate
Accept report
IF
min. torque < final torque < max. torque
IF
min. angle < final angle < max. angle
IF
min. torque rate < final torque rate < max. torque rate
according to the option selected (mean torque or min./max. torque)
Spindle stop
Stop condition for the tightening strategy
selected
OR
current
≥
max. current
Accept report
Accept report condition for the tightening
strategy selected
AND
min. current < current < max. current
O b j e c t i v e
P e a k
t o r q u e
F i n a l a n g l e
T i m e
A n g l e
t h r e s h o l d
A
ng
le
To
rq
ue
M a x
M i n
M a x
M i n
In
te
ns
ity
P e a k
c u r r e n t
M a x
M i n
Summary of Contents for CVIS II
Page 8: ...6159932410 02 English 8 76 SAFETY INSTRUCTIONS...
Page 12: ...6159932410 02 English 12 76 DESCRIPTION AND OPERATION...
Page 18: ...6159932410 02 English 18 76 INITIAL START UP...
Page 28: ...6159932410 02 English 28 76 RESULTS...
Page 48: ...6159932410 02 English 48 76 CONNECTIONS AND INSTALLATION...
Page 66: ...6159932410 02 English 66 76 CYCLE FLOWCHART AND TIMING CHART...