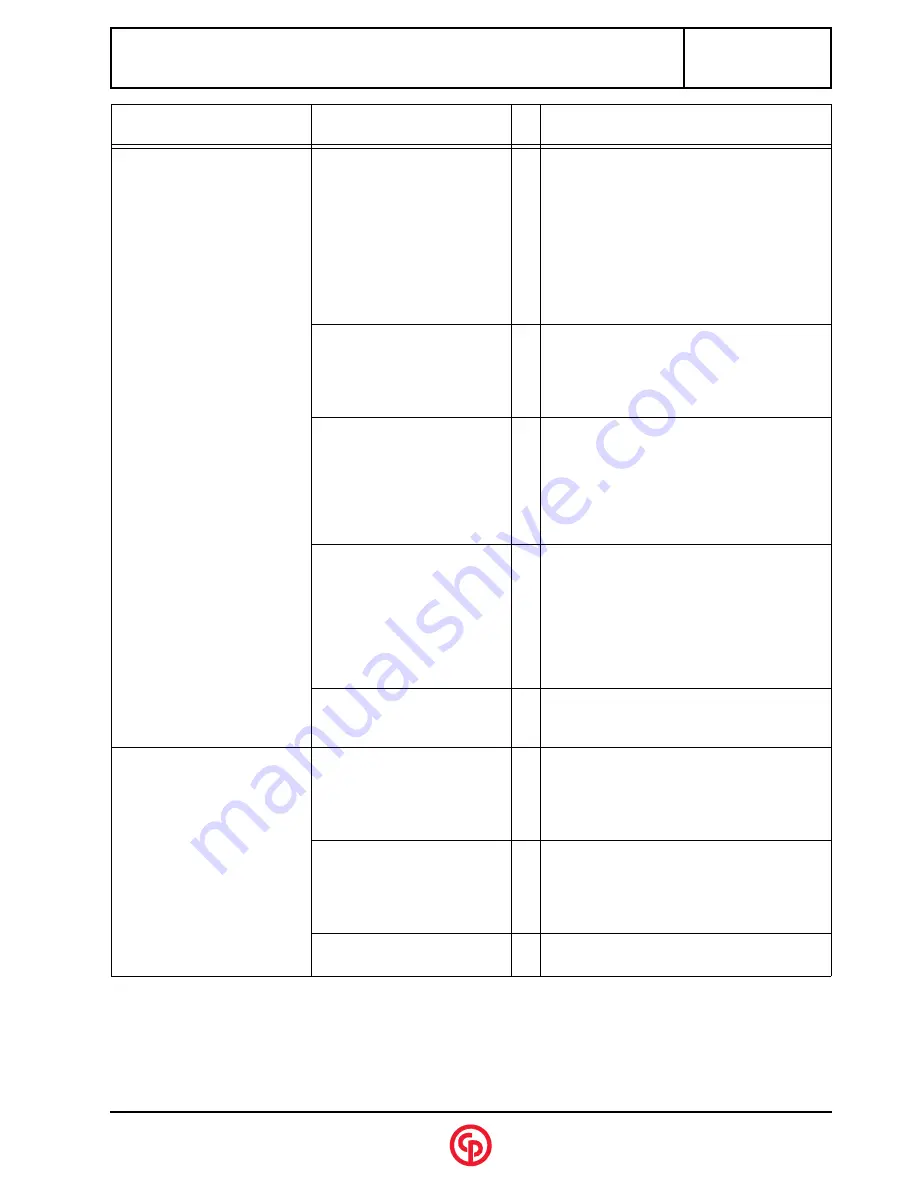
6159932410-02
English
39 / 76
MAINTENANCE
Seen from the controller side, the
tool does not reach the program-
med torque or hardly reaches it.
The motor overheats.
The tool is stopped by the "maxi-
mum current" instruction.
The sensitivity programmed in
the tool is incorrect. In that case,
the actual torque is much higher
than the one given by the control-
ler:
If the tool transducer is faulty, the
cycle will not start because the
"compensation" and "unbalance"
measurements detect the fault at
every cycle start.
22 When the controller is switched on, it reads the
sensitivity saved in the tool memory.
To check the sensitivity, connect a standard tor-
que measuring line in series with the tool. Check
if the results between the 2 measuring lines are
consistent.
To modify the sensitivity, refer to the Operator's
Manual.
To check the tranducer, refer to No. 18.
The angle-head efficiency has
deteriorated to a large extent.
23 Check the torque ripple of the "torque versus
time" curve saved in the unit.
Disconnect the tool angle-head and check
manually for any hard spot.
Change the angle-head.
The "memory" board is faulty.
24 Check the data in the tool memory, and especially
the sensitivity and the associated load compared
to the calibration certificate issued with the tool.
Change the memory board: in that case, it will be
necessary to program the tool memory again.
This operation can only be performed in "superu-
ser" mode by authorized operators (access code).
One of the three phases is not
activated. The possible causes
are:
• Damaged winding in the
motor.
• Faulty cable.
• Faulty speed servodrive.
25 Check the impedances between AB/BC/CA The
values are equal to a few ohms and should be
balanced. Refer to No. 19.
Test the AA;BB;CC links
Check that the contacts are neither twisted nor
pushed back.
If the former points are correct, change the servo-
drive, (a phase changeover can be idle).
The tuning of the resolver is dis-
turbed.
26 No check is possible. Rule out every other possi-
ble cause. Change the motor and send it back to
GEORGES RENAULT for maintenance.
Dispersion or abnormal deviation
in the tightening results.
The angle head is faulty.
27 Check the torque ripple of the "torque versus
time" curve saved in the unit.
Disconnect the tool angle-head and check
manually there is no any hard spot.
Change the angle-head.
Faulty welding in the torque
transducer. An electrical link is
disrupted when the transducer is
under stress.
28 Measure the impedances of the transducer when
stress-free then apply torque stress and make sure
the impedances remain identical.
After having ruled out every other possible cause,
change the transducer.
Abnormal noise. Damaged or cut
shielding.
29 Check the position of the strands of wire in the
tool handle. Change the cables.
Symptoms
Possible causes
No
.
Check
Summary of Contents for CVIS II
Page 8: ...6159932410 02 English 8 76 SAFETY INSTRUCTIONS...
Page 12: ...6159932410 02 English 12 76 DESCRIPTION AND OPERATION...
Page 18: ...6159932410 02 English 18 76 INITIAL START UP...
Page 28: ...6159932410 02 English 28 76 RESULTS...
Page 48: ...6159932410 02 English 48 76 CONNECTIONS AND INSTALLATION...
Page 66: ...6159932410 02 English 66 76 CYCLE FLOWCHART AND TIMING CHART...