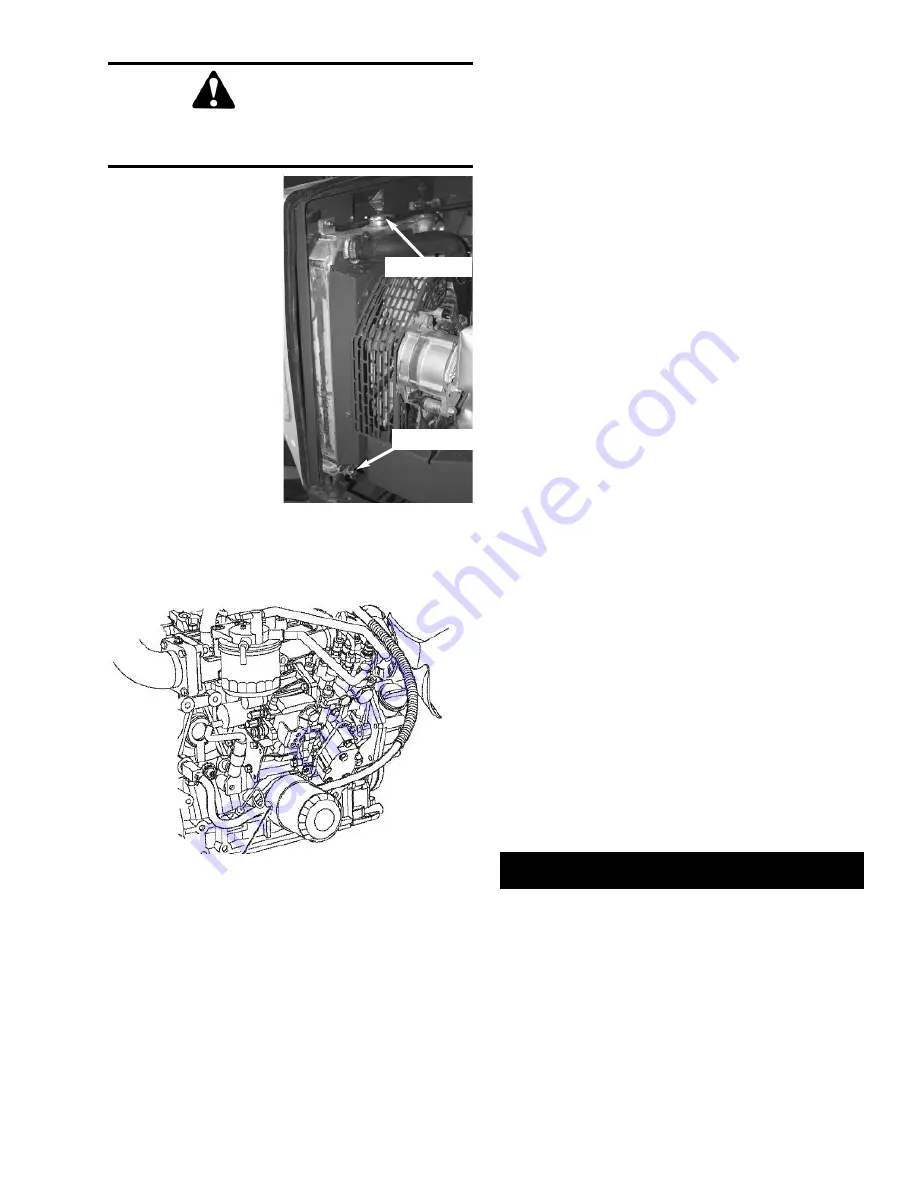
PRINTED IN U.S.A.
59
50960066/AP0813
1. Remove the engine
belly pan.
2. Loosen the radiator
cap to its stop. This
will release any sys-
tem pressure.
Remove the cap
when all pressure is
bled off.
3. Attach a 3/8” hose to
the drain cock and
route it through the
belly pan opening to
a collection contain-
er positioned below
the radiator.
4. Loosen the radiator drain cock to drain the radia-
tor.
5. Remove the coolant hose from the engine oil cool-
er to allow coolant to drain from the engine block.
6. When all coolant is drained, flush the system with
clean fresh water to remove any rust, scale and
contaminants. Allow the radiator and engine block
to drain completely.
7. Replace all drain plugs and tighten the radiator
drain cock. Clean the cooling fins in the radiator
with compressed air or water pressure.
IMPORTANT:
Fill the cooling system with a low-
silicate ethylene glycol based coolant mixed with
quality water and supplemental coolant additives
(SCAs) suitable for heavy-duty diesel engines.
See the engine manual for additional information.
8. Pour the coolant slowly into the radiator until the
coolant is at the bottom of the filler neck. Remove
the cap of the expansion tank and add coolant to
the full mark.
9. Inspect the radiator cap seal before installing it.
Replace it if it appears to be damaged.
10. Run the engine until it reaches operating tempera-
ture. Check the coolant level in the expansion tank.
Add coolant to the expansion tank to bring the
level up to the full mark.
NOTE:
Check the engine temperature gauge
every minute or two after coolant has been
changed. Air pockets can form and it may be nec-
essary to refill the cooling system after a short
period of use, as the air bleeds out of the system.
CHECKING ALTERNATOR AND FAN
BELT CONDITION
Refer to the engine manual for proper belt tension
adjustment and replacement procedures. If the belt
shows wear or cuts, or cracks, it should be replaced.
Order replacement belt from your engine dealer.
CHECKING EXHAUST SYSTEM
Examine the muffler and tail pipe for possible holes.
Re-tighten any loose clamps and make sure the mani-
fold outlet gasket is not leaking. Examine the exhaust
insulating blanket for holes or tears. To prevent exces-
sive heat build up in the engine compartment the insu-
lating blanket should be replaced when it is damaged.
IMPORTANT:
To prevent damaging the insulating
blanket, do not spray it with high pressure water
blast when cleaning the engine.
Perform all other service requirements up to this point,
as well as the following.
CHECKING HYDRAULIC SYSTEM
RELIEF PRESSURES
Pressure settings for relief valves are pre-set at the fac-
tory. A test port is provided under the engine cover.
Service Every 2000 Hours or Two Years
Oil Cooler
Coolant Hose
WARNING
Remove the radiator cap only when the engine
is cool, or painful burns could result.
Radiator Cap
Drain Cock
Summary of Contents for RS5-19
Page 8: ...50960066 AP0813 6 PRINTED IN U S A INTENTIONALLY BLANK To be removed as Dealer s file copy...
Page 69: ...PRINTED IN U S A 67 50960066 AP0813 Date Hours Service Procedure MAINTENANCE LOG...
Page 70: ...50960066 AP0813 68 PRINTED IN U S A Date Hours Service Procedure MAINTENANCE LOG...
Page 73: ...PRINTED IN U S A 71 50960066 AP0813 Electrical Schematic...
Page 74: ...50960066 AP0813 72 PRINTED IN U S A Hydraulic Schematic...