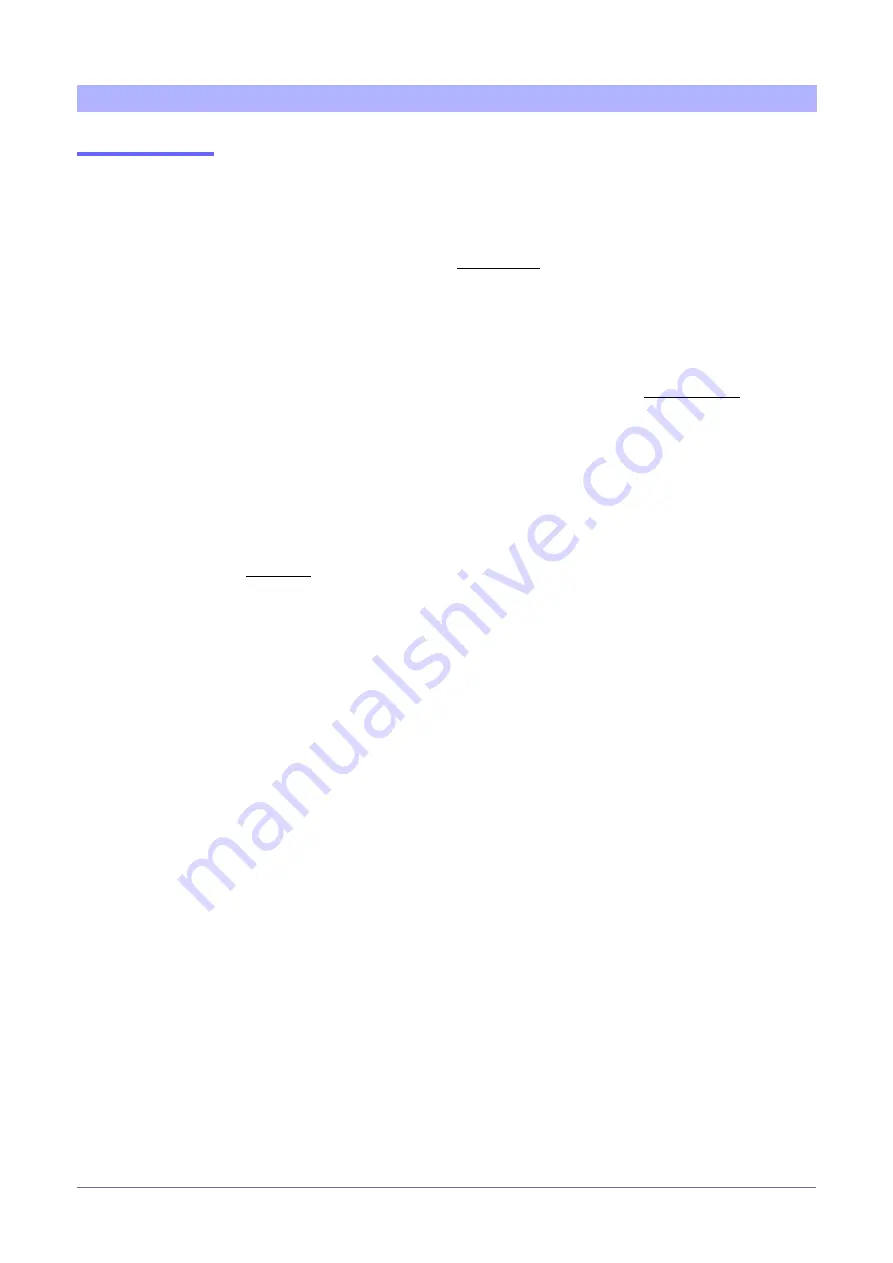
10
80415F_MSW_GFX4-IR_05-2019_ENG
INPUTS
MAIN INPUT
The modular power controller has 4 main inputs to control 4 temperature zones, to which you can connect temperature
sensors (thermocouples and RTD), linear sensors or custom sensors to acquire process variable (PV) values.
To configure, you always have to define the type of probe or sensor (tYP), the maximum and minimum scale limit (Hi.
S – Lo.S) for the process variable value, and the position of the
decimal point
(dP.S).
If the sensor is a thermocouple or resistance thermometer, the minimum and maximum limits can be defined on the specific
scale of the sensor. These limits define the width of the proportional control band and the range of values settable for the
setpoint and alarm setpoints.
There is a parameter to correct the offset of the input signal (oF.S): the set value is algebraically added to the read of
the process variable.
You can read the state of the main input (Err) in which an input error is reported: when the
process variable
goes beyond
the upper or lower scale limit, it assumes the value of the limit and the corresponding state reports the error condition:
Lo = process variable < minimum scale limit
Hi = process variable > maximum scale limit
Err = Pt100 in short circuit and input value below minimum limit,
4...20mA transmitter interrupted or not powered
Sbr = Tc probe interrupted or input value above maximum limit
If noise on the main input causes instability of the acquired value, you can reduce its effect by setting a low pass
digital filter (Flt). The default setting of 0.1sec is usually sufficient.
You can also use a
digital filter
(Fld) to increase the apparent stability of the process variable PV; the filter introduces
a hysteresis on its value: if the input variation remains within the set value, the DPV value is considered unchanged.