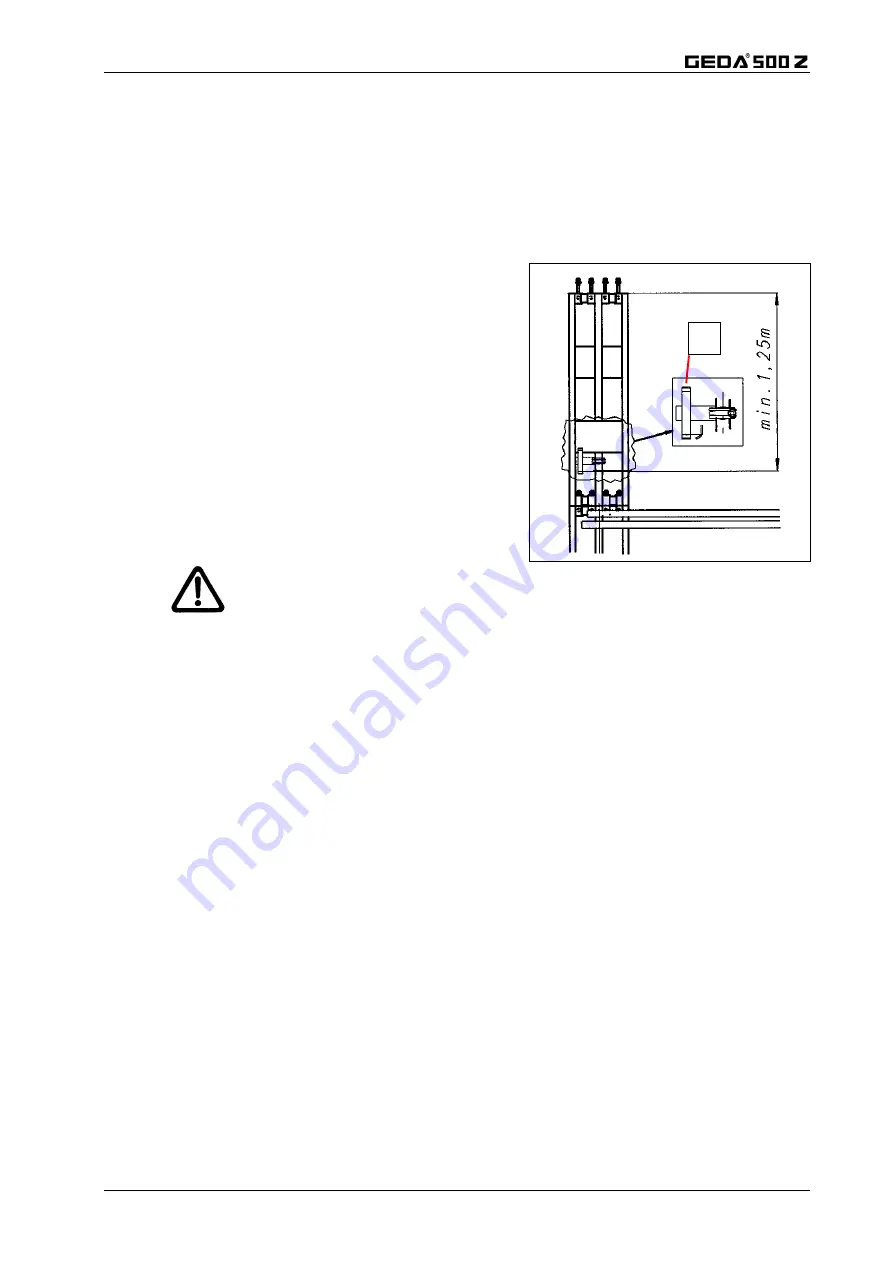
Rack and pinion hoist
Assembly and Operating Manual
53 / 92
BL054 GB Edition 08.2015
6.3.2
Emergency limit switch approach bar
An approach bar (1) must be installed at the top stop point, before the
drive pinion leaves the gear rack.
Adhere to a minimum distance to the top of the mast end of
1.25 m
.
The hoist is stopped at this bar by the UP operating limit switch or
the EMERGENCY limit switch in case of an error.
Assembly
−
From the load platform, insert the
approach bar (1) between the
two rectangular mast tubes and
secure it to the rear, circular
mast end using the coupling.
The mast may be moved out over the last mast anchor during
operation to a max. of 4.5m (mast anchor to trolley upper edge).
The Emergency limit switch bar must be accordingly set low.
1
Summary of Contents for 14830
Page 2: ......
Page 3: ...Rack and pinion hoist Assembly and Operating Manual 3 92 BL054 GB Edition 08 2015...
Page 4: ...Rack and pinion hoist Assembly and Operating Manual 4 92 BL054 GB Edition 08 2015...
Page 36: ...Rack and pinion hoist Assembly and Operating Manual 36 92 BL054 GB Edition 08 2015...
Page 90: ...Rack and pinion hoist Assembly and Operating Manual 90 92 BL054 GB Edition 08 2015...
Page 91: ......