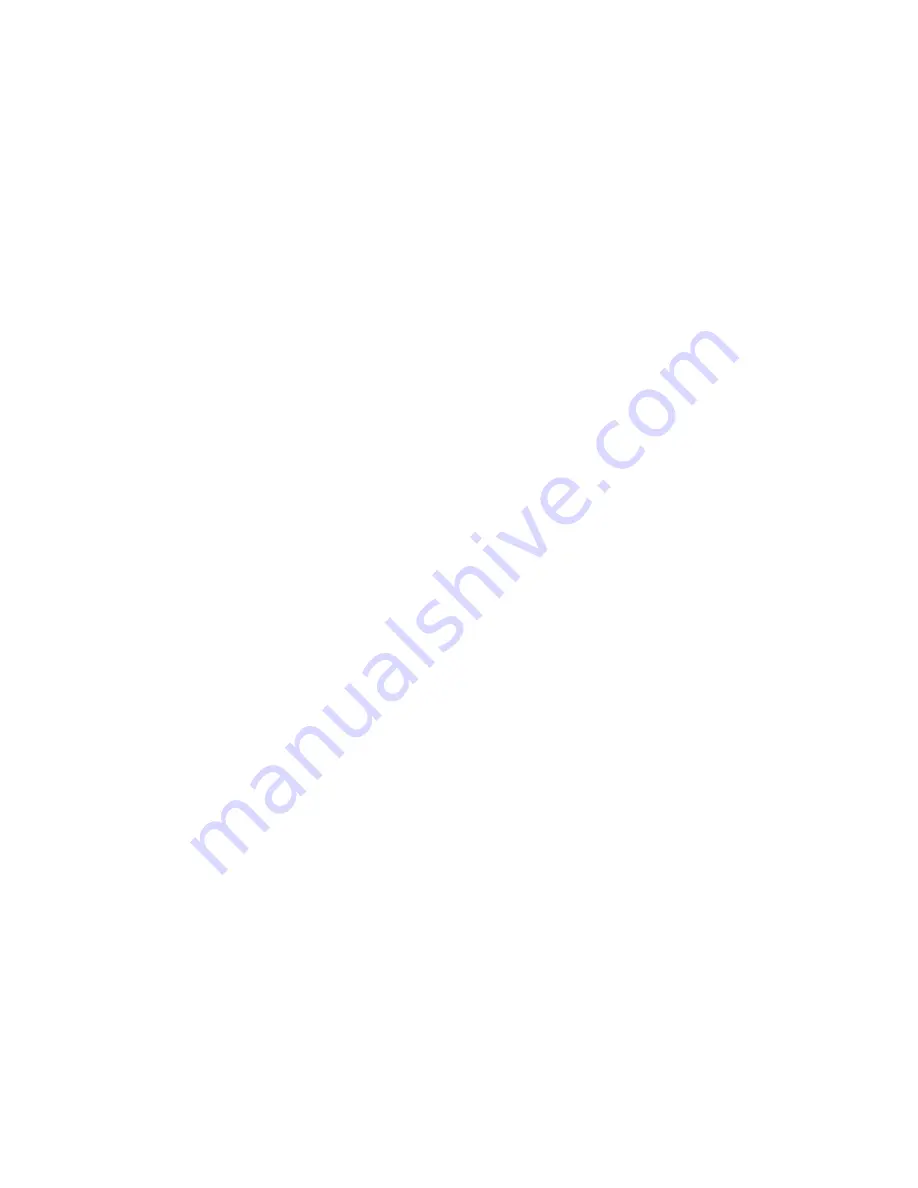
CHAPTER 5: SETPOINTS
CONTROL ELEMENTS
MM300 MOTOR MANAGEMENT SYSTEM – INSTRUCTION MANUAL
5–57
Test Manual Mode
Range: On, Off, Unaffected
Default: On
When the test switch is on, this setpoint determines if the manual mode is forced on,
forced off, or is unaffected.
Stop/start control
element
An external stop sequence has occurred if the relay detects that either contactor A or
contactor B has dropped out without receiving a stop command. If the
External Stop Action
setpoint is programmed as “Stop”, the relay will accept this as a stop control and display
the
External Stop
message. If this setpoint is set to “Trip”, the relay will treat this as an
emergency stop trip. This trip condition must be reset before the motor can be restarted.
Most protection and control elements in this relay are sensitive to whether the motor is
stopped, starting, or running. These include the jam, acceleration, undercurrent,
underpower, overvoltage, and undervoltage protection, the process interlocks, and the
thermal start inhibit and undervoltage restart elements.
Traditionally, the motor is deemed to have entered the starting state when the motor
current changes from zero to some measurable value, and to have entered the running
state when the current having increased above FLA then subsides below FLA. This
algorithm is satisfactory for most applications. The current profile of full voltage across-
the-line starters for instance typically goes from zero to 6 × FLA within a cycle of the
contactor closing, and then decays exponentially until it reaches 1 × FLA just before
reaching normal operating speed.
However, some starter types implemented in the MM300 have significantly different
current profiles. For instance, with an inverter starter, the inverter may ramp the motor
speed up so slowly that the current never exceeds FLA. Alternatively, the current may
initially exceed 1 × FLA, but subside well before reaching normal operating speed. The
traditional algorithm could either not declare the motor reaching the running state, or
declare it much too soon.
Another problem can develop when there is a brief supply interruption for which the
immediate undervoltage restart feature recloses the contactor so quickly that there is little
or no inrush current.
The traditional algorithm would detect the start (if it is fast enough), but may or may not
detect the running state that follows. Even if it does detect the running state, as it is an
atypical start, the learned values such as learned acceleration time would be corrupted.
The MM300 employs an improved starting and running state detection algorithm.
Normally, it declares starting when either contactor A or contactor B closes. Running is
declared when either contactor has been closed for one second, and then current is found
to be below 1 × FLA. This provides equivalent functionality to the traditional algorithm.
However, the advanced algorithm also accepts
Starting Status Block
and
Running Status
Block
signals. Most starter types leave these signals in their default off state, where they
have no effect on the starting and running declarations. Where required however, the
starters can manipulate these signals to correct the above described problems with the
traditional algorithm. The inverter starter for instance asserts the
Starting Status Block
signal when it powers up the inverter, and then allows the starting state to be declared by
turning it off only when the ramp up command is issued. The inverter starter also asserts
the
Running Status Block
signal and then allows the running state to be declared by
turning it off only when the inverter signals up-to-speed.
In addition, the advanced algorithm accepts a
UVR Short Dip
signal from the undervoltage
restart element. This signal will carry the running status through short dips followed by
immediate reclose.
If an A or B motor contactor is externally energized, the relay will treat this as a start A or B
control, and display an
External Start A Alarm
or an
External Start B Alarm
message.
The stop/start control element also consolidates the various start and stop signals for the
convenience of other elements.
Summary of Contents for Multilin MM300
Page 20: ...1 14 MM300 MOTOR MANAGEMENT SYSTEM INSTRUCTION MANUAL SPECIFICATIONS CHAPTER 1 INTRODUCTION ...
Page 184: ...6 8 MM300 MOTOR MANAGEMENT SYSTEM INSTRUCTION MANUAL COMMANDS CHAPTER 6 DIAGNOSTICS ...
Page 198: ...A 6 MM300 MOTOR MANAGEMENT SYSTEM INSTRUCTION MANUAL REPAIRS CHAPTER A APPENDIX A ...