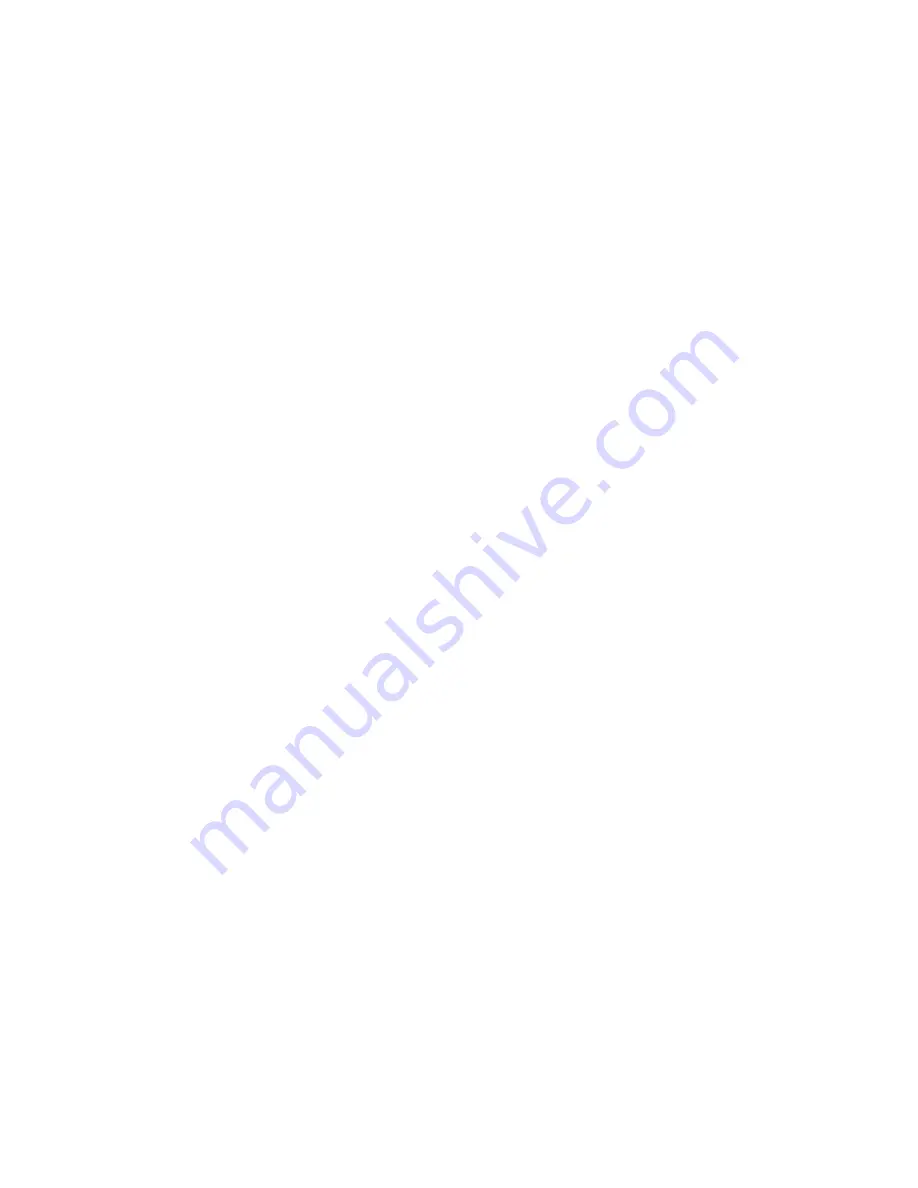
13
3. Use an adjustable wrench to remove the washer leveling legs.
Pedestal Prep
1. Pull the pedestal drawer out as far as it will go.
2. Remove screws from drawer slides. Slide drawer out of the base and set aside.
Install the pedestal to the washer
1. Place the pedestal against the bottom of the unit. Check to be sure the drawer front is at the front of
the washer.
2. Align the holes in the pedestal with the holes in the bottom of the unit. Use a 9/16 in. socket wrench to
install the 4 washer mounting bolts through the pedestal and into the unit – do not tighten.
3. Slide the pedestal toward the unit until it is aligned front to back. Use a 9/16 in. socket wrench to
securely tighten the bolts.
4. Stand the washer or upright. Move it close to its
fi
nal location.
5. Make sure that the washer is level by placing a level on top. Check side to side and front to back.
6. Use an open ended wrench to adjust the legs in and out. Tighten the lock nut against the bottom of the
pedestal. Note: To minimize vibration, the locking nuts must be tight.
7. Reinstall the drawer.
8. Remove the 4 shipping screws on the back side of the washer.