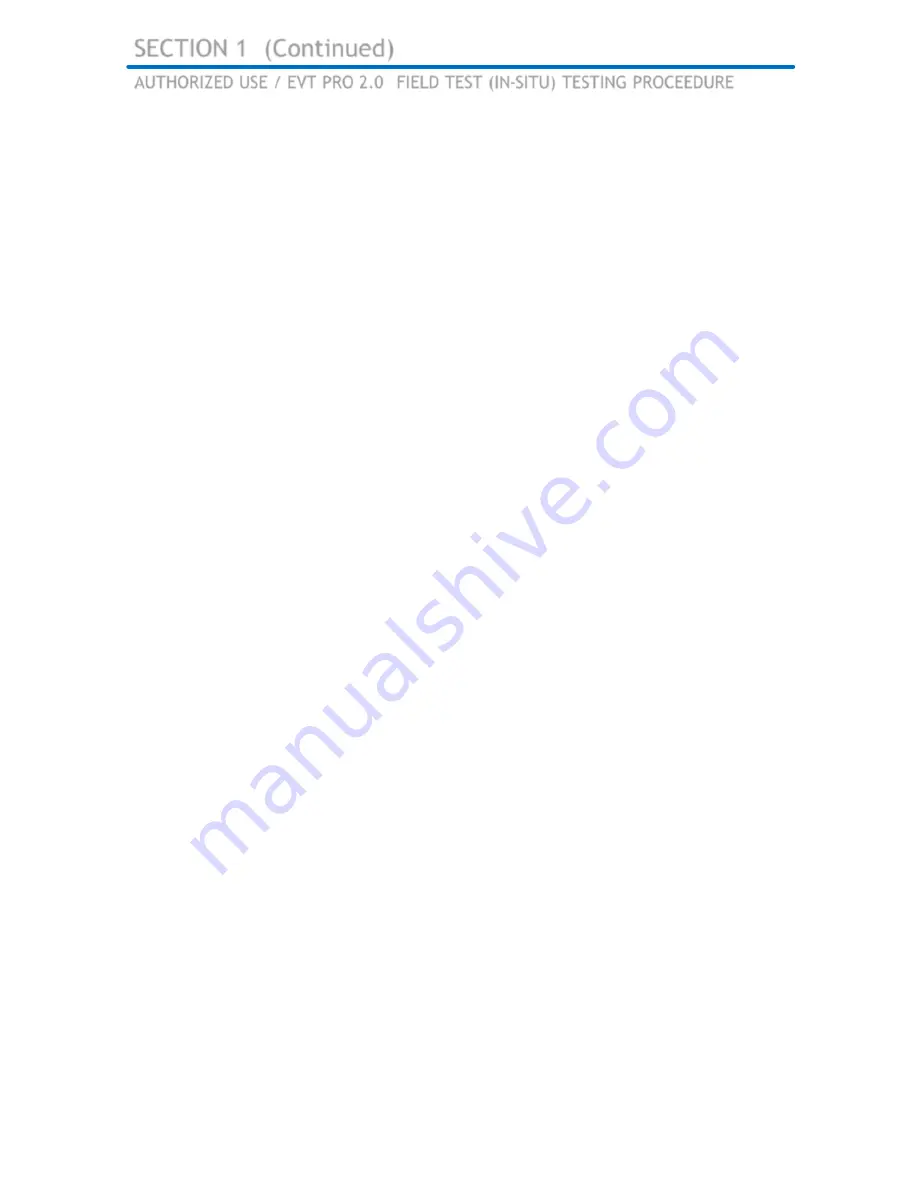
SECTION 1 (Continued)
AUTHORIZED USE / EVT PRO 2.0
®
FIELD TEST (IN-SITU) TESTING PROCEEDURE
8.
CAUTION: It is highly recommended when testing PRVs containing a bellows in a closed
system, steps must be taken to ensure that the bellows is intact and no pressure exists in the
bonnet area of the PRV. Non bellows PRVs exposed to built-up or superimposed back
pressure should not be tested unless the media contained in the discharge system poses no
threat to the environment or the technicians conducting the test.
V.
Recommended EVT PRO 2.0
®
Test Sequence:
9.
Remove cap and lift nut, if applicable. If necessary, remove cap gasket and install the spindle
adaptor on the spindle. Slowly lower the test bracket, onto the bonnet or yoke of the PRV as
outlined in this EVT PRO 2.0
®
User's Manual. Connect hydraulic lines to the cylinder and the
pump. Connect the color-coded leads to the load cell, lift sensor, and the acoustic sensor on
the test bracket and to the corresponding leads on the pump. Connect the pump to the EVT
PRO 2.0
®
computer using the Wi-Fi link-up.
10. Once the equipment is mounted and all connections are made, verify inlet pressure from either
the Control Room or through the use of a local gauge. Ensure that inlet pressure is between 50-
90% of PRV set pressure before starting the test. Communications should be maintained with
the Control Room throughout the EVT PRO 2.0
®
testing sequence.
NOTE: For dangers of
testing below 50% or above 90% of set pressure, see warning in Section 2 on page 3.
11. Using slow and deliberate pumping strokes increase the load on the PRV spindle to the pre
calculated value determined by the EVT PRO 2.0
®
computer until an audible or visual indication
of set point is reached. Once set point is reached, stop pumping and release the hydraulic
pressure. If the determined set point is within the popping pressure tolerance established by the
appropriate section of the ASME Code, conduct two additional tests and verify the same
standards are met.
12. If adjustments to set point are necessary, remove the test bracket and make the adjustments.
Use caution to prevent the spindle from rotating or causing the PRV to go into full lift. If it is
determined that ring adjustments are required, gag the valve before making any adjustments.
Once complete, resume testing as described in 11above.
13. Once testing is complete, restore the PRV to its operational condition ensuring both the cap and
lift nut are installed, if applicable. If reinstalling a lift-nut, ensure the proper gap is established
between the lift-nut and lift-lever per manufacturer's instructions. Seal all external adjustment
points, and tag the PRV per approved GTC procedures as outlined in the National Board
Inspection Code.
VI.
Job Completion:
14. It is recommended that technicians complete all required documentation, obtain customer
signature(s) as required, and provide customer with copies of documentation. Ensure final test
data is entered in ValvKeep as the GTC requires, either at the customer site or upon return to
base.
EVT PRO 2.0
®
Operations and Technical Manual (Rev 1.0
– 2016)
NOT FOR COPY OR DISTRIBUTION
Page 2
Summary of Contents for EVT-Pro 2.0
Page 10: ...EVT PRO 2 0 Operations and Technical Manual Rev 1 0 2016 NOT FOR COPY OR DISTRIBUTION Page 6 ...
Page 11: ...EVT PRO 2 0 Operations and Technical Manual Rev 1 0 2016 NOT FOR COPY OR DISTRIBUTION Page 7 ...
Page 57: ...APPENDIX INFORMATION EVT Pro 2 0 Operations and Technical Manual Rev 1 0 2016 ...