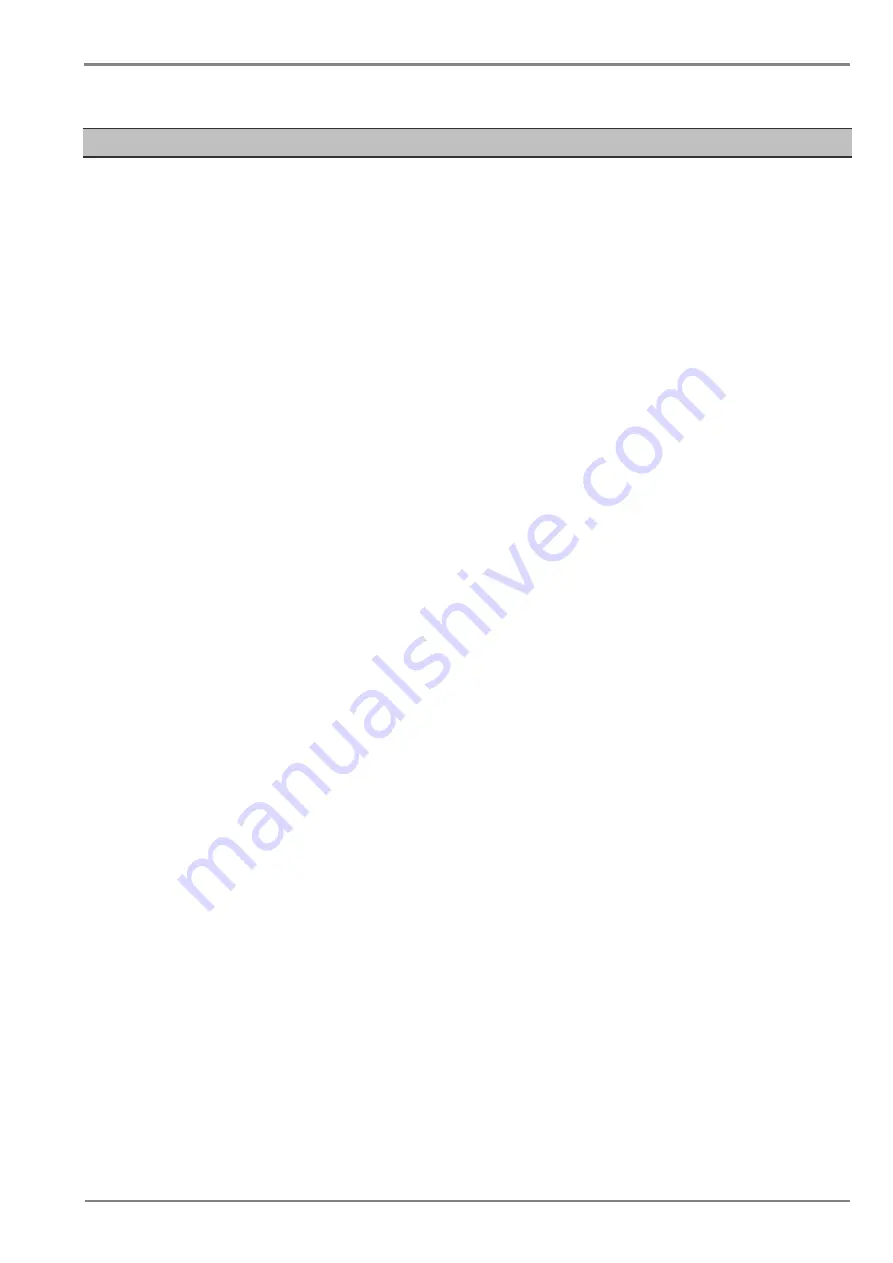
P50 Agile P153
7 Protection Parameter Settings
P153/EN M/B
7-3
1
CHAPTER OVERVIEW
This chapter consists of the following sections:
1
Chapter Overview
2
Protection Parameter Settings
2.1
System Data
2.2
CB CONTROL Settings
2.3
DATE AND TIME Settings
2.4
CONFIGURATION Settings
2.5
TRANS. RATIOS Settings
2.6
RECORD CONTROL Settings
2.7
COMMUNICATION Settings
2.8
IO CONFIGURATION Settings
2.9
O/P RELAY CONFIG Settings
2.10
DISTURBANCE RECORD Settings
2.11
COMMISSION TEST Settings
2.12
GROUP Settings
2.12.1
SYSTEM CONFIG SETTINGS
2.12.2
OVERCURRENT Settings
2.12.2.1
I>1 Function
2.12.2.2
I>2 Function
2.12.2.3
I>3 Function
2.12.3
EARTH FAULT 1 (Measured)
2.12.3.1
IN1>1 Function
2.12.3.2
IN1>2 Function
2.12.3.3
IN1>3 Function
2.12.4
EARTH FAULT 2 (Derived)
2.12.4.1
IN2>1 Function
2.12.4.2
IN2>2 Function
2.12.4.3
IN2>3 Function
2.12.5
THERMAL OVERLOAD Settings
2.12.6
UNDERCURRENT Settings
2.12.7
COLD LOAD PICKUP Settings
2.12.8
NEG SEQUENCE O/C Settings
2.12.8.1
I2>1 Function
2.12.8.2
I2>2 Function
2.12.8.3
I2>3 Function
2.12.9
BROKEN CONDUCTOR Settings
2.12.10
CB FAIL Settings
2.12.11
VIEW RECORDS
Summary of Contents for Agile P50 Series
Page 3: ...P50 Agile P153 1 Introduction P153 EN M B 1 1 INTRODUCTION CHAPTER 1...
Page 4: ...1 Introduction P50 Agile P153 1 2 P153 EN M B...
Page 10: ...1 Introduction P50 Agile P153 1 8 P153 EN M B...
Page 11: ...P50 Agile P153 2 Safety Information P153 EN M A 2 1 SAFETY INFORMATION CHAPTER 2...
Page 22: ...Chapter 2 Safety Information P50 Agile P153 2 12 P153 EN M A...
Page 23: ...P50 Agile P153 3 Hardware Design P153 EN M B 3 1 HARDWARE DESIGN CHAPTER 3...
Page 24: ...3 Hardware Design P50 Agile P153 3 2 P153 EN M B...
Page 32: ...3 Hardware Design P50 Agile P153 3 10 P153 EN M B...
Page 33: ...P50 Agile P153 4 Front Panel P153 EN M B 4 1 FRONT PANEL CHAPTER 4...
Page 34: ...4 Front Panel P50 Agile P153 4 2 P153 EN M B...
Page 39: ...P50 Agile P153 5 Configuration P153 EN M B 5 1 CONFIGURATION CHAPTER 5...
Page 40: ...P50 Agile P153 5 Configuration P153 EN M B 5 2...
Page 150: ...P50 Agile P153 5 Configuration P153 EN M B 5 112...
Page 151: ...P50 Agile P153 6 Protection Functions P153 EN M B 6 1 PROTECTION FUNCTIONS CHAPTER 6...
Page 152: ...6 Protection Functions P50 Agile P153 6 2 P153 EN M B...
Page 168: ...7 Protection Parameter Settings P50 Agile P153 7 2 P153 EN M B...
Page 189: ...P50 Agile P153 8 Monitoring Control P153 EN M B 8 1 MONITORING CONTROL CHAPTER 8...
Page 190: ...8 Monitoring Control P50 Agile P153 8 2 P153 EN M B...
Page 207: ...P50 Agile P153 9 SCADA Communications P153 EN M B 9 1 SCADA COMMUNICATIONS CHAPTER 9...
Page 208: ...12 SCADA Communications P50 Agile P153 9 2 P153 EN M B...
Page 220: ...12 SCADA Communications P50 Agile P153 9 14 P153 EN M B...
Page 221: ...P50 Agile P153 10 Installation P153 EN M B 10 1 INSTALLATION CHAPTER 10...
Page 222: ...10 Installation P50 Agile P153 10 2 P153 EN M B...
Page 234: ...13 Commissioning Instructions P50 Agile P153 13 2 P153 EN M B...
Page 242: ...12 Maintenance and Troubleshooting P50 Agile P153 12 2 P153 EN M B...
Page 250: ...12 Maintenance and Troubleshooting P50 Agile P153 12 10 P153 EN M B...
Page 252: ...13 Technical Specifications P50 Agile P153 13 2 P153 EN M B...
Page 263: ...P50 Agile P153 14 Wiring Diagrams P153 EN M B 14 1 WIRING DIAGRAMS CHAPTER 14...
Page 264: ...14 Wiring Diagrams P50 Agile P153 14 2 P153 EN M B...
Page 267: ......