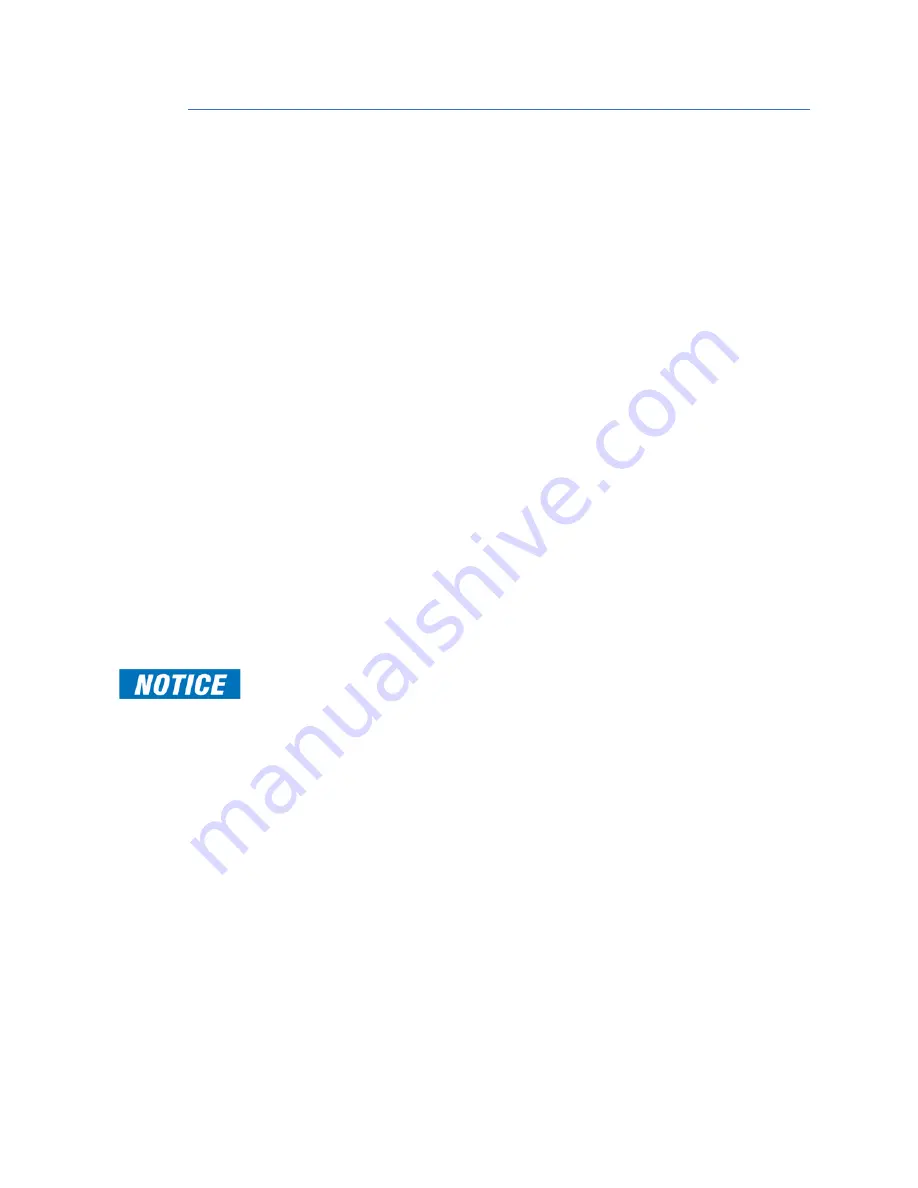
7–20
350 FEEDER PROTECTION SYSTEM – INSTRUCTION MANUAL
GENERAL MAINTENANCE
CHAPTER 7: MAINTENANCE
General maintenance
The 350 requires minimal maintenance. As a microprocessor-based relay, its
characteristics do not change over time. The expected service life of a 350 is 20 years
when the environment and electrical conditions are within stated specifications.
While the 350 performs continual self-tests, it is recommended that maintenance be
scheduled with other system maintenance. This maintenance can involve in-service, out-
of-service, or unscheduled maintenance.
In-service maintenance
1.
Visual verification of the analog values integrity, such as voltage and current (in
comparison to other devices on the corresponding system).
2.
Visual verification of active alarms, relay display messages, and LED indications.
3.
Visual inspection for any damage, corrosion, dust, or loose wires.
4.
Event recorder file download with further events analysis.
Out-of-service maintenance
1.
Check wiring connections for firmness.
2.
Analog values (currents, voltages, RTDs, analog inputs) injection test and metering
accuracy verification. Calibrated test equipment is required.
3.
Protection elements setting verification (analog values injection or visual verification
of setting file entries against relay settings schedule).
4.
Contact inputs and outputs verification. This test can be conducted by direct change
of state forcing or as part of the system functional testing.
5.
Visual inspection for any damage, corrosion, or dust.
6.
Event recorder file download with further events analysis.
FASTPATH:
To avoid deterioration of electrolytic capacitors, power up units that are stored in a de-
energized state once per year, for one hour continuously.
Unscheduled maintenance (system interruption)
•
View the event recorder and oscillography for correct operation of inputs, outputs,
and elements.