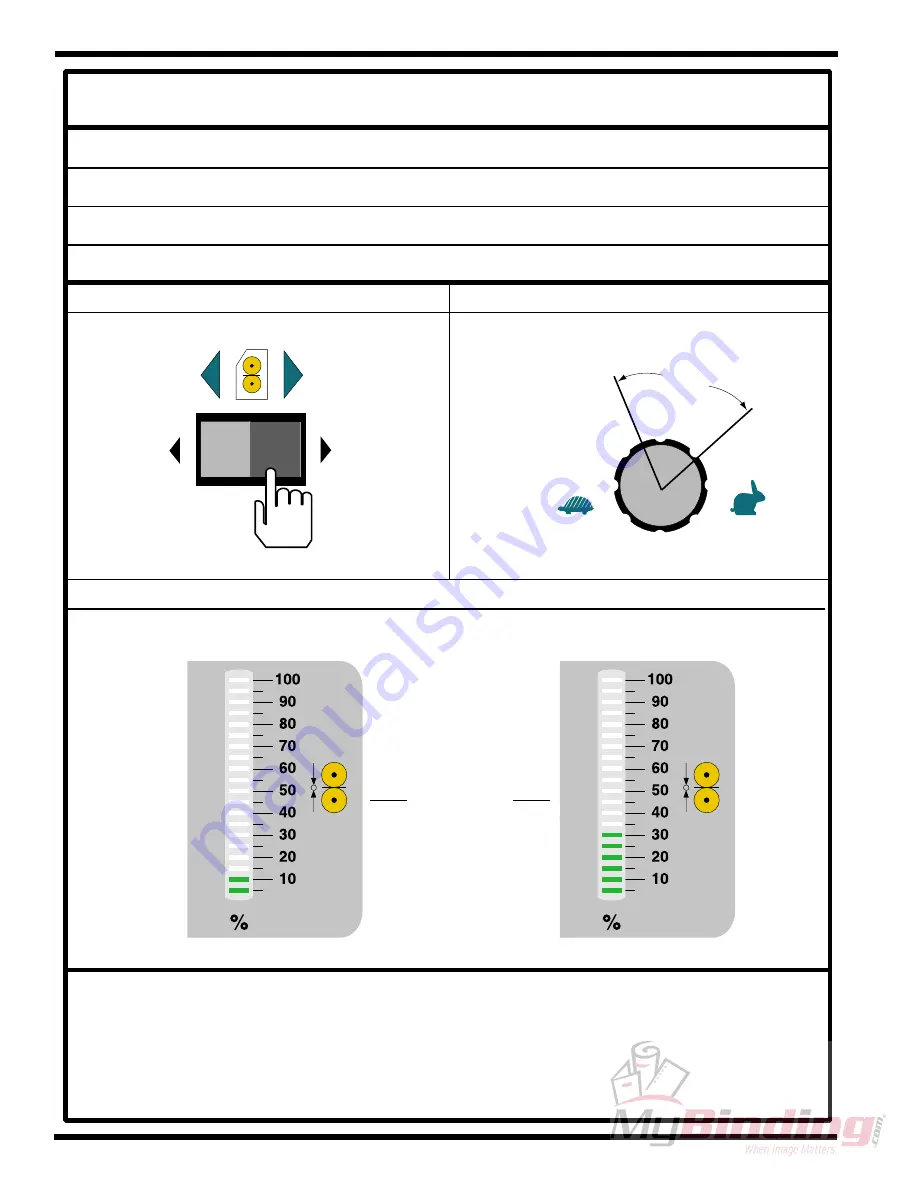
Page 6 - 8
© April 2001 General Binding Corporation
Applications
F 60 C Operation and Maintenance Manual
PROCESS CONTROL CHART
Materials - Pre-coating substrates
Top material : Roll of pressure sensitive mount adhesive
Bottom material : N/A
Other material (s) : Substrates, leader board and trailer board
Motor Direction
Motor Speed
1
2
3
4
5
6
7
8
9
10
range
Roller Pressure
RANGE
Notes : The roll of mount adhesive should not exceed the substrate by more than 1 in.
(2.54 cm). Speed will be determined by what is comfortable for the operator. Pressure is
dependent on the substrate. Do not crush the substrate. Use a leader board to start the
run and stop the run when the trailer board is in the nip of the rollers. Stopping on a
subtsrate will leave an impression on the board. Refer to helpful hints for pressure
sensitive materials and mounting.