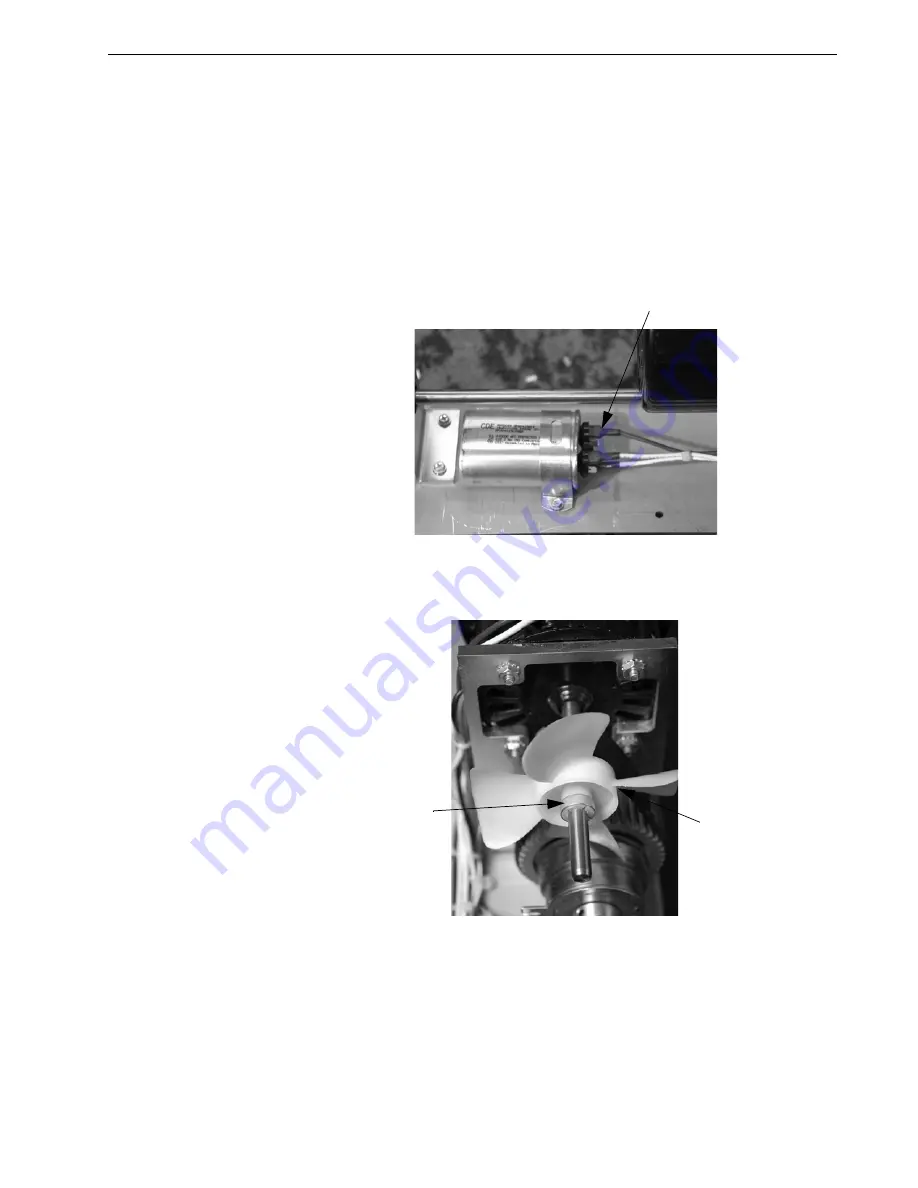
Repair and Adjustment Procedures
Advanced Punch Service Manual
© Copyright 2009 GBC. All rights reserved.
4-63
4.9.5 Punch Module Motor Replacement
Procedure
Replace motor when it malfunctions.
To replace the Punch Module motor:
1. Cut any wire ties as necessary to release the motor wires.
2. Unplug motor wire connections from the capacitor [1].
Figure 4.71 Punch Capacitor.
3. Remove the metal spring clip [1] from the fan and slide the fan [2] off the shaft.
Figure 4.72 Punch Fan and Spring Clip.
Installation Note:
When installing the fan, be sure to align the flat of the fan hub
with the flat on the shaft. Also, make sure the hub and spring clip are facing away
from the motor.
[3]
[1]
[2]
Summary of Contents for AdvancedPunch
Page 1: ...Document 7712571 Rev C1 23 08 2013 AdvancedPunch Technical Service Manual ...
Page 143: ...Section 5 5 4 Copyright 2009 GBC All rights reserved Advanced Punch Service Manual ...
Page 144: ...Parts List Advanced Punch Service Manual Copyright 2009 GBC All rights reserved 5 5 ...
Page 149: ...Section 5 5 10 Copyright 2009 GBC All rights reserved Advanced Punch Service Manual ...
Page 150: ...Parts List Advanced Punch Service Manual Copyright 2009 GBC All rights reserved 5 11 ...
Page 199: ...Section 8 8 4 Copyright 2009 GBC All rights reserved Advanced Punch Service Manual 2 1 ...
Page 201: ...Section 8 8 6 Copyright 2009 GBC All rights reserved Advanced Punch Service Manual 2 1 2 1 2x ...