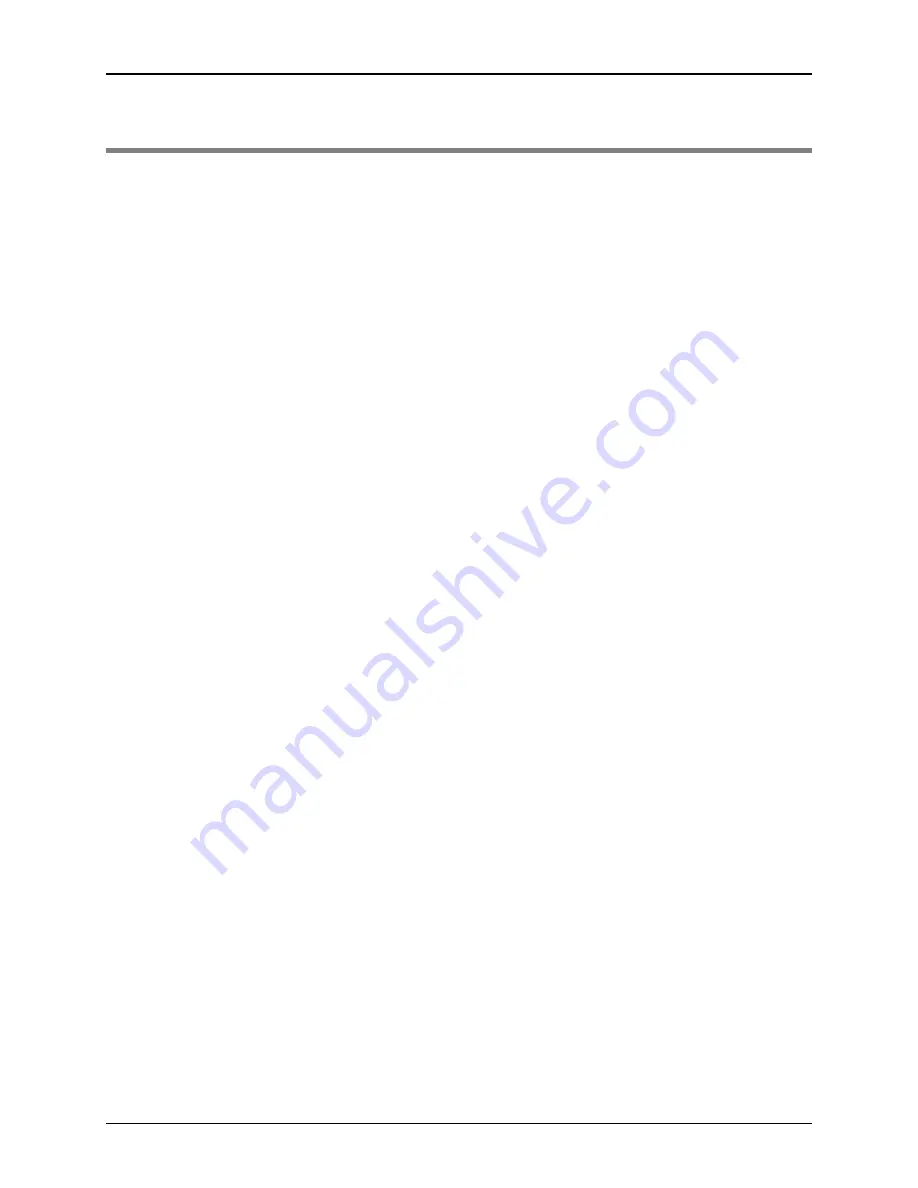
Installation
MDE-4339 9820Q ASTRA Installation/Operation • July 2004
3
2. Installation
Installation Precautions
All installations must conform with all building/fire codes, all Federal, State, and Local codes,
National Electrical Code, (NFPA 70), NFPA 30, and Automotive and Marine Service Station Code
(NFPA 30A) codes and regulations. Canadian users must also comply with the Canadian
Electrical Code.
Plan your installation carefully. A pump cannot be expected to work satisfactorily unless the
installation is correct. Dispensing troubles, which seem to be pump-related, are frequently traced
to faulty installation. Review the following list of installation
DO's
and
DON'T's
to avoid
potential problems:
1.
DO
read the
WARNINGS
page at the front of this manual, preceding the Table of Contents.
It contains important information regarding the safe use of your dispensing equipment.
2.
DO
install an emergency power cutoff. In addition to circuit breaker requirements of NFPA
70 and NFPA 30A, a single control which simultaneously removes AC power from all site
dispensing equipment is recommended. This control must be readily accessible, clearly
labeled, and in accordance with all local codes.
In a fuel management system application, the EMERGENCY STOP and STOP keys on the
console and/or the optional EMERGENCY STOP button on the Island Card Reader do not
remove AC power from equipment and under certain conditions, will not stop product flow.
In order to provide the highest level of safety to you, your employees, and customers, we
recommend that all employees be trained as to the location and procedure for turning off
power to the entire system.
3.
DO
have the pump installed by a competent installer/electrician.
4.
DO
install breakaway coupling on discharge hose. If using a high hose retriver, install
breakaway approximately 12" downstream of hose clamp on nozzle side of clamp.
5.
DO NOT
experiment with a pump if you are not sure the installation is correct.
6.
DO NOT
overload sub- or main breaker panels.
7.
DO NOT
use power line wiring of inadequate capacity. (Use gauge specified by the wiring
diagram or wire chart provided in Section 4).
8.
DO NOT
use a circuit breaker of improper size. (See Section 4).
9.
DO NOT
use the GASBOY fuel dispensing equipment to remove water ballast from the
storage tank.
10.
DO NOT
use gaskets on covers of explosion-proof type boxes. The sealing compound found
around wires at various locations within conduit is a requirement of the National Electrical
Code and should not be disturbed. Ensure that the mating surfaces between the junction box
and cover are free of dirt, debris, nicks and scratches. Tighten junction box covers before
replacing panels.
11.
DO NOT
use knock-out boxes or flexible conduit for installing this unit. All power wires
should be run in threaded, rigid, metal conduit. All threaded connections must be drawn up
tight. All but one opening in the power junction box are provided with plugs at the factory.
At completion of the installation, it is the installer's responsibility to ensure that any unused
openings are plugged.
Summary of Contents for 9822Q
Page 1: ...Series 9820Q ASTRA Installation Operation Manual MDE 4339 formerly 035090...
Page 18: ...GASBOY Series 9820Q 12 MDE 4339 9820Q ASTRA Installation Operation July 2004...
Page 22: ...GASBOY Series 9820Q 16 MDE 4339 9820Q ASTRA Installation Operation July 2004...
Page 32: ...GASBOY Series 9820Q 26 MDE 4339 9820Q ASTRA Installation Operation July 2004...