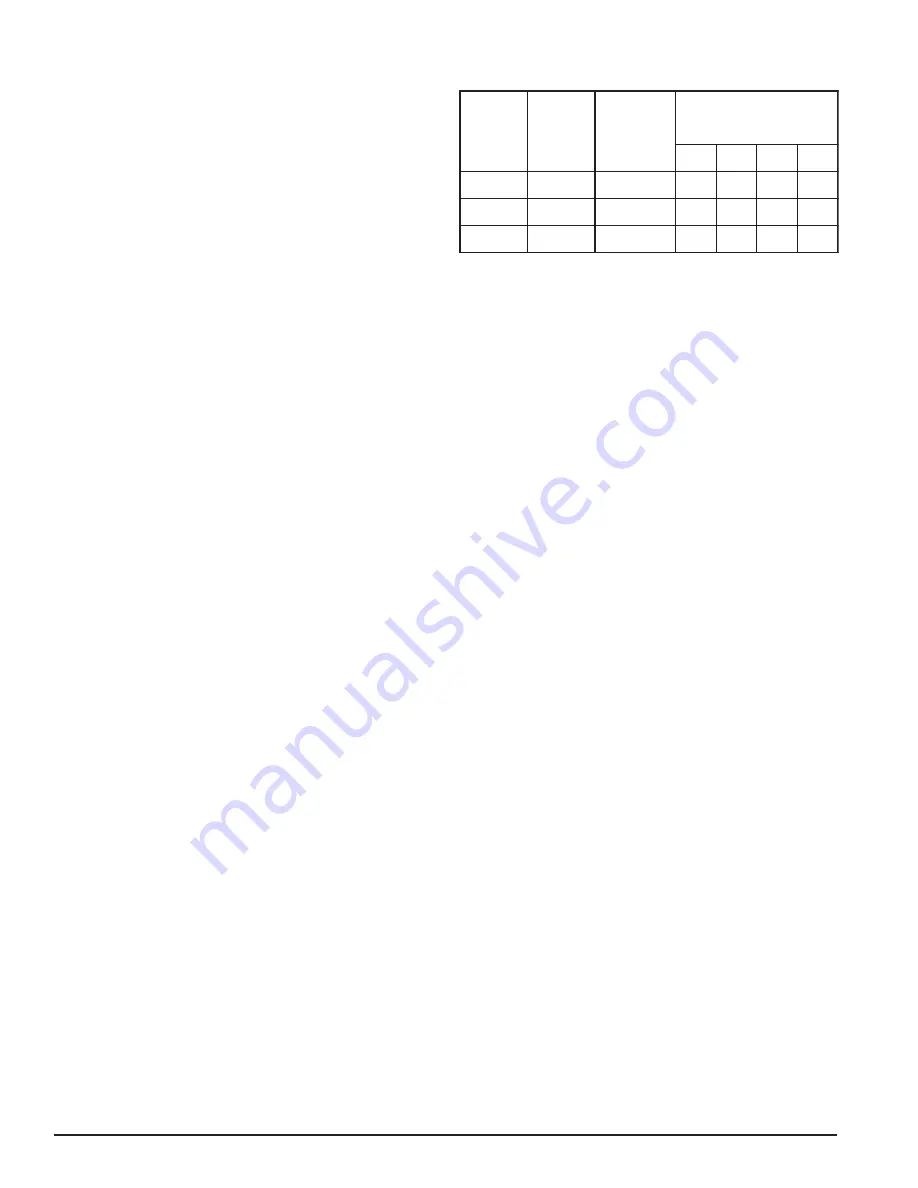
4
and depressurized for servicing. Bypass piping may be in-
stalled around the dryer for uninterrupted airflow when the
dryer is serviced. If the compressed air operation cannot
tolerate undried air for short periods, install a second dryer
in the bypass line.
Compressed air systems commonly require filters to re-
move compressor oils, particulates, condensed liquids and
other contaminants. When an oil-removal filter is used, in-
stall the filter downstream of the refrigerated dryer. At this
location, the life of the replaceable filter element is pro-
longed since some of the entrained oil is removed by the
dryer and drained through the separator.
Ammonia contamination may cause problems within the
dryer heat exchanger. If ammonia is present in the air-
stream, consult your local distributor for recommendations.
Piping and Connections
Piping must be furnished by the user unless otherwise
specified. Connections and fittings must be rated for the
maximum operating pressure given on the dryer data plate
and must be in accordance with applicable codes. Support
all piping; do not allow the weight of any piping to stress the
connections of the dryer or filters. Piping should be at least
the size of the inlet and outlet connections to minimize pres-
sure drop in the air system. See Table I for dryer inlet and
outlet connections.
Drains
Condensate must be drained from the dryer to prevent its
reentrainment. The dryer is equipped with an automatic
drain valve.
The user must install a discharge line for the drain valve
and run the line to an environmentally-approved conden-
sate collection/disposal system. Pipe or copper tubing ½-
inch or larger is recommended for condensate discharge
line. Do not use ¼-inch or -inch O.D. flexible tubing unless
the discharge line is shorter than 10 feet. Install the dis-
charge lines so that condensate can be seen as it drains.
Cooling Water
Cooling water is required for water-cooled refrigerant con-
densers. The user is responsible for piping the water to
and from the condenser. A factory-installed water regulat-
ing valve in the condenser inlet connection is standard.
The required water flow rate depends on the water tem-
perature (refer to Table II). A valve supplied with the dryer
automatically adjusts the flow to compensate for variations
in water temperature, water pressure and dryer air load.
Operating the dryer with inadequate condenser cooling wa-
ter (temperatures above or pressures below those in Table
II) will cause a rise in dew point unless the dryer inlet air-
flow is reduced. The refrigerant discharge pressure control
will shut down the refrigerant compressor if cooling water
is inadequate.
Table 2
COOLING WATER REQUIREMENTS
a
R
E
Y
R
D
L
E
D
O
M
N
N
O
C
S
E
Z
I
S
s
e
h
c
n
i
(
)
T
P
N
b
T
A
E
H
N
O
I
T
C
E
J
E
R
)
r
h
/
U
T
B
(
D
E
R
I
U
Q
E
R
R
E
T
A
W
G
N
I
L
O
O
C
)
m
p
g
(
W
O
L
F
c
F
°
0
7
F
°
0
8
F
°
5
8
F
°
0
9
W
0
0
8
¾
5
8
0
,
1
4
—
—
0
.
4
0
.
6
W
0
0
0
1
¾
9
8
2
,
0
5
—
—
5
.
5
0
.
9
W
0
0
2
1
¾
4
4
1
,
9
9
—
—
5
.
5
5
.
8
a
Minimum water pressure is 25 psig for city water and 35 psig for tower
water. Maximum water pressure is 150 psig. Temperature rise across
the condenser is approximately 10°F.
b
Inlet and outlet connections are the same size NPT.
c
Contact factory if available cooling water is higher than 90°F.
Note:
Cooling water pressures below or temperatures above those listed
in Table II may reduce drying capacity. The refrigerant discharge pres-
sure control will shut down the refrigerant compressor if cooling is inad-
equate.
Water Quality Recommendations
Water quality is often overlooked when the cooling system
of a water-cooled dryer is examined. Water quality deter-
mines how effective the heat transfer rate and flow rate will
remain during the dryer’s use. The quality of water used in
any cooling system does not remain constant during the
operation of the system. The water makeup is affected by
evaporation, corrosion, chemical and temperature changes,
aeration, scale and biological formations. Most problems
in a cooling system show up first in a reduction in the heat
transfer rate, then in a reduced flow rate and, finally, with
damage to the system.
If the cooling water is dirty, install a strainer ahead of the
condenser inlet. Install shutoff valves so that the strainer
can be drained and cleaned at regular intervals. There are
many constituents in the water system that must be bal-
anced to have a good stable system. The following are the
major components that should be monitored:
Corrosion
Corrosion problems may be caused by: chlorides, low pH
levels and high levels of dissolved oxygen. These condi-
tions should be monitored and treated as necessary to pre-
vent corrosion.
Scale
Scale formation will help to prevent corrosion. Therefore, a
thin uniform coating of calcium carbonate is desired on the
inner surfaces of the cooling system. However, in excess,
scale formation will inhibit effective heat transfer.
One of the largest contributors to scale formation is the
precipitation of calcium carbonate out of the water. This is
dependent on temperature and pH. The higher the pH value,
the greater the chance of scale formation. Scale can be
controlled with water treatment.
Summary of Contents for RCD800
Page 27: ...27 NOTES...