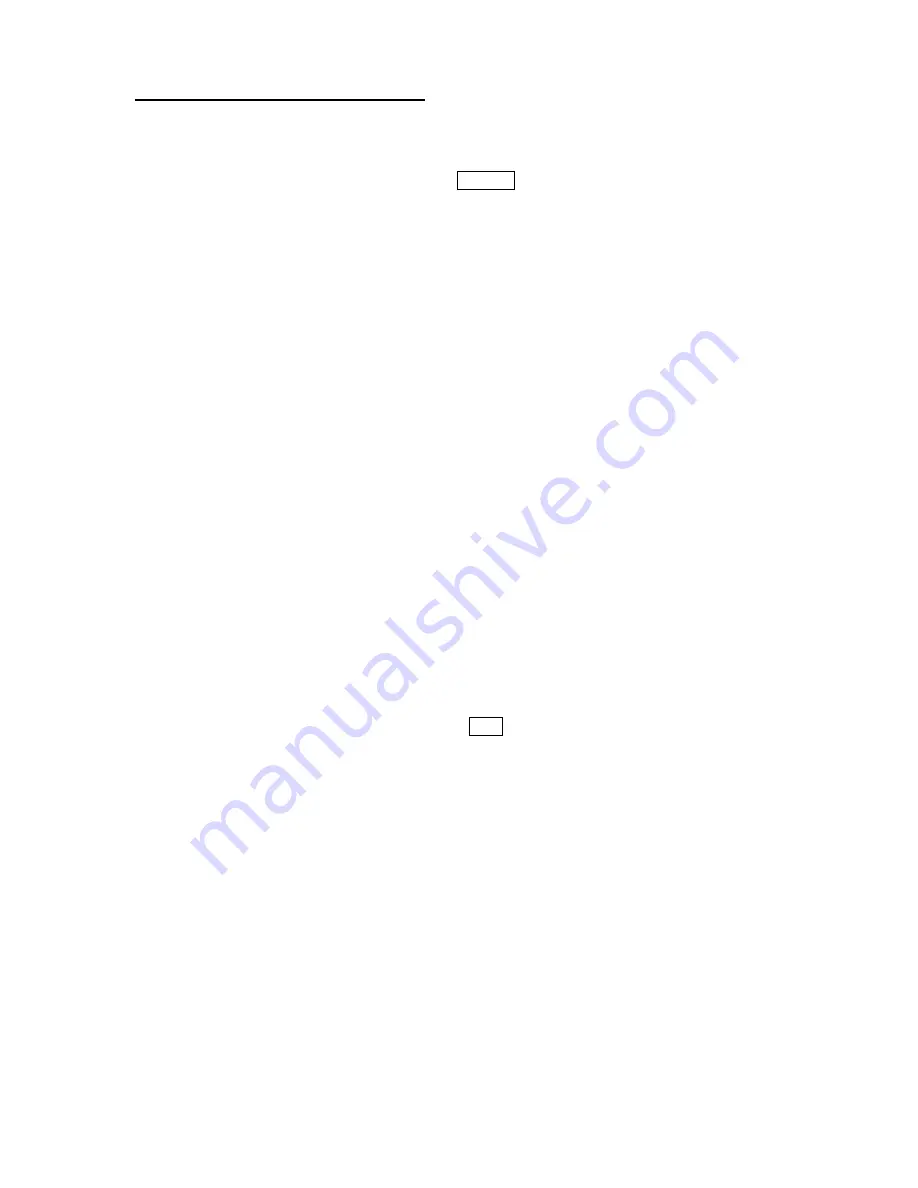
Fulton Heating Solutions, Inc. -- PHW Manual -- 2010-0713
Page 55
Section 3 – Operation
Post these instructions in an appropriate place near the boiler and maintain in good legible
condition.
Warning
If you do not follow these instructions exactly, a fire or explosion may result causing property
damage, personal injury, or loss of life.
Fulton Pulse combustion boilers do not have a pilot. They are equipped with an ignition device which
automatically lights the boiler. Do not try to light the boiler by hand.
BEFORE OPERATING
smell all around the boiler area for gas. Be sure to smell next to the floor as some
gas is heavier than air and will settle.
IF YOU SMELL GAS:
- Do not light any appliance.
- Do not touch any electric switch.
- Do not use any phone in your building.
- Immediately call your gas supplier from a neighbor’s phone, and then follow your gas supplier’s
instructions. If you cannot reach your gas supplier, call the fire department.
Use only your hand to turn the gas cock knob. Never use tools. If the knob will not turn by hand, don’t try
to repair it. Call a qualified service technician.
FORCE OR ATTEMPTED REPAIR MAY RESULT IN A
FIRE OR EXPLOSION.
Note
DO NOT use this boiler if any part has been under water. Immediately call a qualified service
technician to inspect the boiler and to replace any part of the control system and/or gas control(s)
which has been under water.
1. Before Operating Your Fulton Pulse Boiler
a) Stop! Make sure you have read and followed all previous safety information.
b) Turn off all electric power to the boiler.
c) Turn gas cock knob clockwise to “OFF”. Figure 18. (This gas cock knob is also the
emergency shut-off device.)
Summary of Contents for PHW 1000
Page 2: ...Fulton Heating Solutions Inc PHW Manual 2010 0713 Page 2...
Page 6: ...Fulton Heating Solutions Inc PHW Manual 2010 0713 Page 6...
Page 7: ...Fulton Heating Solutions Inc PHW Manual 2010 0713 Page 7 Section 1...
Page 8: ...Fulton Heating Solutions Inc PHW Manual 2010 0713 Page 8...
Page 17: ...Fulton Heating Solutions Inc PHW Manual 2010 0713 Page 17 Section 2...
Page 18: ...Fulton Heating Solutions Inc PHW Manual 2010 0713 Page 18...
Page 42: ...Fulton Heating Solutions Inc PHW Manual 2010 0713 Page 42 Figure 8...
Page 43: ...Fulton Heating Solutions Inc PHW Manual 2010 0713 Page 43 Figure 9 Figure 10 Figure 11...
Page 53: ...Fulton Heating Solutions Inc PHW Manual 2010 0713 Page 53 Section 3...
Page 54: ...Fulton Heating Solutions Inc PHW Manual 2010 0713 Page 54...
Page 71: ...Fulton Heating Solutions Inc PHW Manual 2010 0713 Page 71 Section 4...
Page 72: ...Fulton Heating Solutions Inc PHW Manual 2010 0713 Page 72...
Page 80: ...Fulton Heating Solutions Inc PHW Manual 2010 0713 Page 80...
Page 81: ...Fulton Heating Solutions Inc PHW Manual 2010 0713 Page 81 Section 5...
Page 82: ...Fulton Heating Solutions Inc PHW Manual 2010 0713 Page 82...
Page 90: ...Fulton Heating Solutions Inc PHW Manual 2010 0713 Page 90...
Page 92: ...Fulton Heating Solutions Inc PHW Manual 2010 0713 Page 92...
Page 93: ...Fulton Heating Solutions Inc PHW Manual 2010 0713 Page 93...