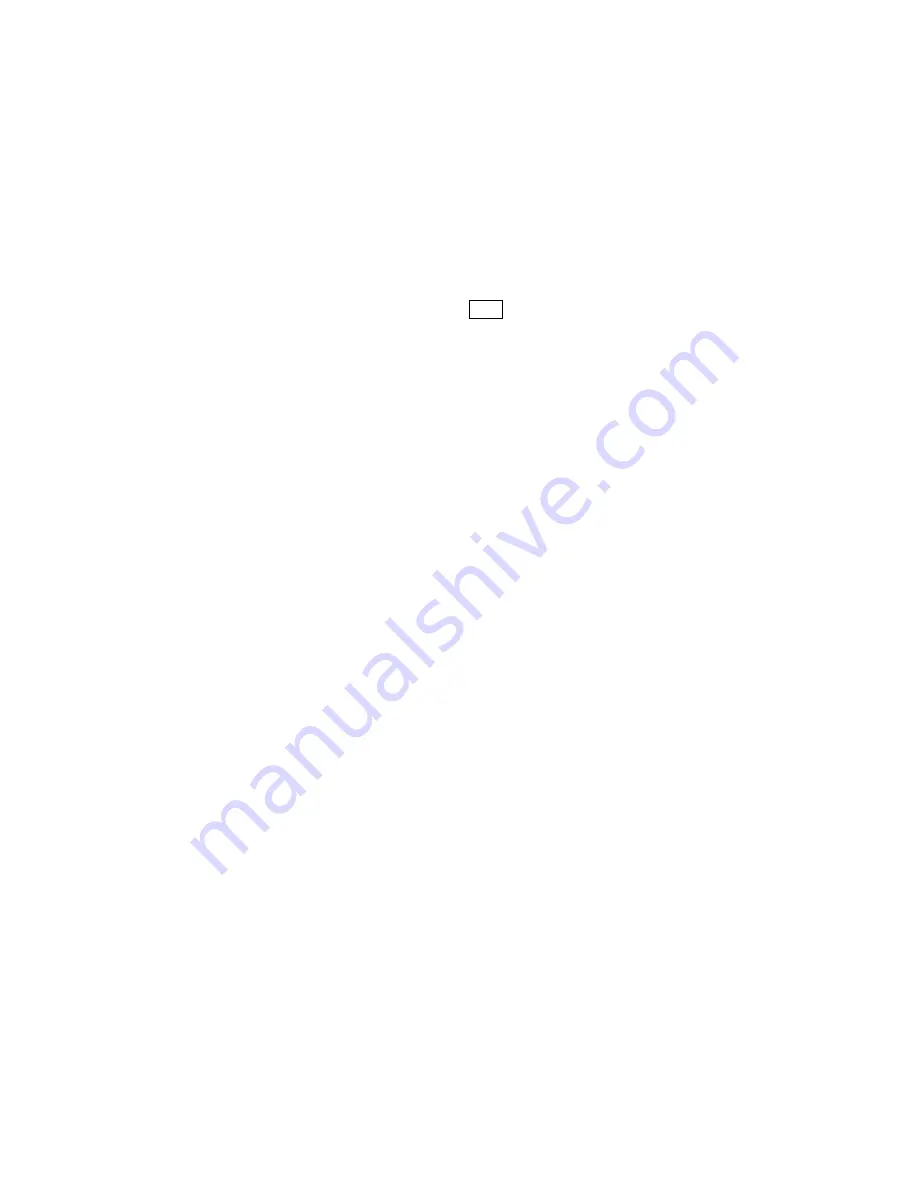
Fulton Heating Solutions, Inc. -- PHW Manual -- 2010-0713
Page 40
3. Apply a bead of sealant, about 1/2“in diameter, completely around the male
(without tabs) end of each conduit section or elbow, between 1/4” and 3/8” from
the end of the section. Also run a similar sized bead down the seam weld of each
section, from the edge of the pipe to the top of the bulge.
4. Fully insert the male end of the section into the female fitting of the section
below. Attach the sections together. Inspect the joint to ensure that flue gases
will not escape. If necessary, apply additional sealant to any voids. Allow the
sealant 24 hours to cure before operating the boiler.
Note
See specific manufacturers instructions for complete installation details.
20. Exhaust Muffler Installation
a) For muffler drain installation:
1. For mufflers installed in the vertical configuration the drain can be
plugged.
2. For mufflers installed in the horizontal configuration, the drain opening
should be at the down slope “6 o’clock” position and should be piped to
the drain line between the boiler and the condensate drain.
For best
noise attenuation, the muffler should be installed as close to the
boiler as possible
.
21. Air Intake & Exhaust Piping Requirements for the Pulse Boiler
a) For both intake and exhaust piping, using piping that matches the inlet/outlet connection
sizes for the first 35 feet and 4 elbows closest to the boiler is acceptable.
b) The piping can be extended to 100 feet and 6 elbows by increasing the pipe size to 6” for
the PHW300 - PHW1000, and to 8” for the PHW2000.
c) Regarding the PHW1400, the air intake and exhaust piping must be 4” for the first 10 feet
and then piping must be upsized to 6” for up to 40 feet. If going beyond 40 feet, instead of
upsizing to 6” after the first 10 feet, upsize to 8” and it is acceptable to extend the piping
up to 100 feet and 6 elbows.
d) It is important to note that the 10 feet of piping is required as a minimum on the air intake
(even if taking combustion air from the boiler room) or exhaust. This creates the
appropriate amount of backpressure for pulse combustion to operate properly.
e) If air intake or exhaust layouts require upsizing, it is important to keep the first 10 feel
closest to the boiler matching the outlet connection size of the boiler.
Summary of Contents for PHW 1000
Page 2: ...Fulton Heating Solutions Inc PHW Manual 2010 0713 Page 2...
Page 6: ...Fulton Heating Solutions Inc PHW Manual 2010 0713 Page 6...
Page 7: ...Fulton Heating Solutions Inc PHW Manual 2010 0713 Page 7 Section 1...
Page 8: ...Fulton Heating Solutions Inc PHW Manual 2010 0713 Page 8...
Page 17: ...Fulton Heating Solutions Inc PHW Manual 2010 0713 Page 17 Section 2...
Page 18: ...Fulton Heating Solutions Inc PHW Manual 2010 0713 Page 18...
Page 42: ...Fulton Heating Solutions Inc PHW Manual 2010 0713 Page 42 Figure 8...
Page 43: ...Fulton Heating Solutions Inc PHW Manual 2010 0713 Page 43 Figure 9 Figure 10 Figure 11...
Page 53: ...Fulton Heating Solutions Inc PHW Manual 2010 0713 Page 53 Section 3...
Page 54: ...Fulton Heating Solutions Inc PHW Manual 2010 0713 Page 54...
Page 71: ...Fulton Heating Solutions Inc PHW Manual 2010 0713 Page 71 Section 4...
Page 72: ...Fulton Heating Solutions Inc PHW Manual 2010 0713 Page 72...
Page 80: ...Fulton Heating Solutions Inc PHW Manual 2010 0713 Page 80...
Page 81: ...Fulton Heating Solutions Inc PHW Manual 2010 0713 Page 81 Section 5...
Page 82: ...Fulton Heating Solutions Inc PHW Manual 2010 0713 Page 82...
Page 90: ...Fulton Heating Solutions Inc PHW Manual 2010 0713 Page 90...
Page 92: ...Fulton Heating Solutions Inc PHW Manual 2010 0713 Page 92...
Page 93: ...Fulton Heating Solutions Inc PHW Manual 2010 0713 Page 93...