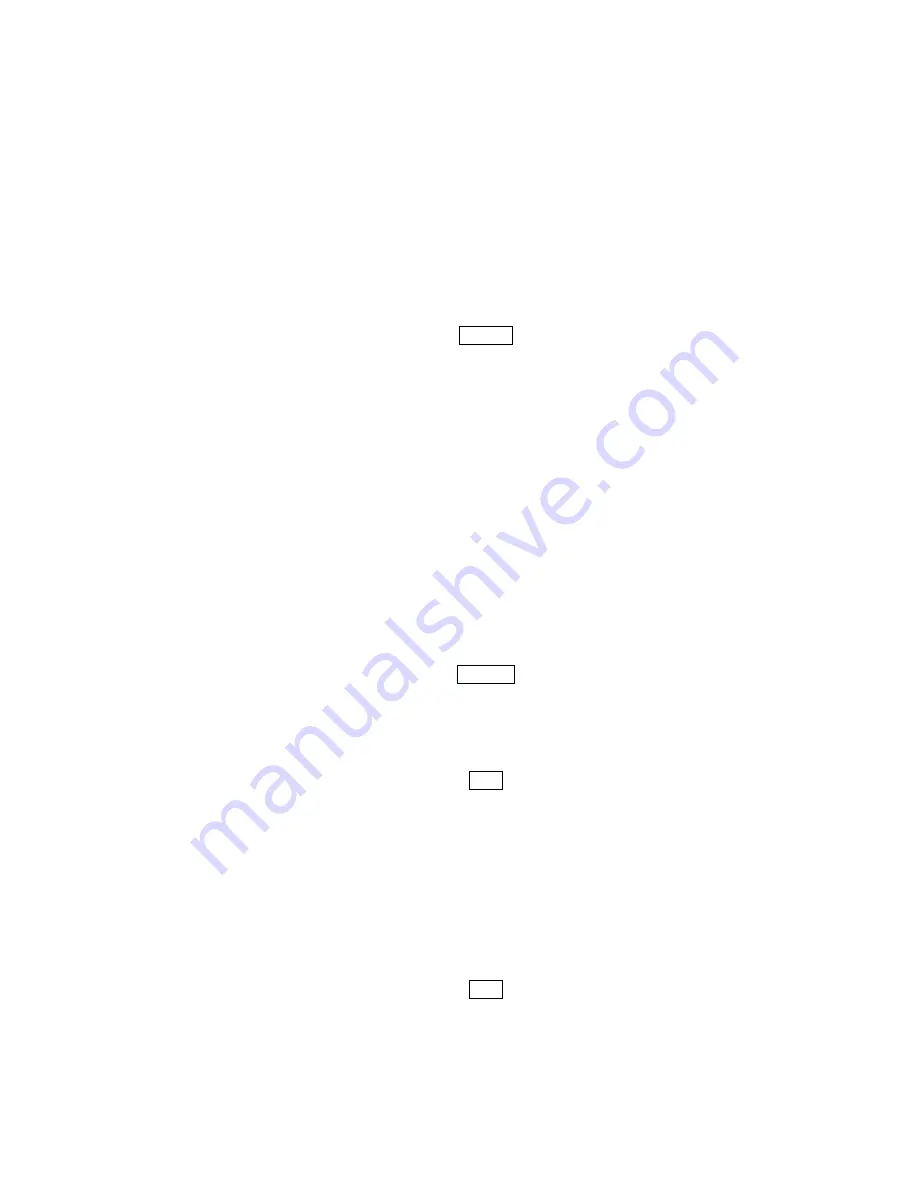
Fulton Heating Solutions, Inc. -- PHW Manual -- 2010-0713
Page 30
b) The pipe and the fittings used should be new and free of dirt or other deposits. Piping
must be of the proper size to insure adequate gas supply.
c) Gas pressure to inlet of gas train should be 7" WC for natural gas and 11" WC for
propane. Connect gas supply line to the open end of the tee on which the drip leg is
installed.
d) When making gas piping joints, use a sealing compound resistant to the action of
liquefied petroleum gases. Do not use Teflon tape on gas line threads.
e) After gas piping is completed and before wiring installation is started, carefully check all
piping connections, (factory and field), for gas leaks. Use a soap and water solution.
Caution
Some soaps used for leak testing are corrosive to certain types of metals. Rinse all
piping thoroughly with clean water after leak check has been completed.
f) The boiler must be disconnected at the boiler shut off valve from the gas supply piping
system during any pressure testing of the system at pressure in excess of 1/2 psig (14"
WC / 3.5 kPa).
g) The boiler must be isolated from the gas supply piping system by closing its individual
manual shut off valve during any pressure testing of the gas supply system at test
pressures equal or less than 1/2psi (3.5kPa).
h) Gas vents to outdoor air must be provided for the gas pressure regulator and the high
gas pressure switches. Restricting orifices or bleed orifices should not be used at
anytime.
Warning
Do not use matches, candles, flame or other sources of ignition to check for gas
Ieaks.
Note
The vent line connection on the gas pressure regulator and high gas pressure
switches must be piped to outdoor air by installer in accordance with the National
Fuel Gas Code, ANSI Z223- 1-1991 or latest addenda.
In Canada gas installations must be in accordance with the current CAN/CGA
B149.1 and .2 and/or local codes.
Note
Gas Pressure Switches: Low pressure switch should not be set less than 50% of
manifold pressure. High pressure switch should not be set any more than 150% of
the manifold pressure.
Summary of Contents for PHW 1000
Page 2: ...Fulton Heating Solutions Inc PHW Manual 2010 0713 Page 2...
Page 6: ...Fulton Heating Solutions Inc PHW Manual 2010 0713 Page 6...
Page 7: ...Fulton Heating Solutions Inc PHW Manual 2010 0713 Page 7 Section 1...
Page 8: ...Fulton Heating Solutions Inc PHW Manual 2010 0713 Page 8...
Page 17: ...Fulton Heating Solutions Inc PHW Manual 2010 0713 Page 17 Section 2...
Page 18: ...Fulton Heating Solutions Inc PHW Manual 2010 0713 Page 18...
Page 42: ...Fulton Heating Solutions Inc PHW Manual 2010 0713 Page 42 Figure 8...
Page 43: ...Fulton Heating Solutions Inc PHW Manual 2010 0713 Page 43 Figure 9 Figure 10 Figure 11...
Page 53: ...Fulton Heating Solutions Inc PHW Manual 2010 0713 Page 53 Section 3...
Page 54: ...Fulton Heating Solutions Inc PHW Manual 2010 0713 Page 54...
Page 71: ...Fulton Heating Solutions Inc PHW Manual 2010 0713 Page 71 Section 4...
Page 72: ...Fulton Heating Solutions Inc PHW Manual 2010 0713 Page 72...
Page 80: ...Fulton Heating Solutions Inc PHW Manual 2010 0713 Page 80...
Page 81: ...Fulton Heating Solutions Inc PHW Manual 2010 0713 Page 81 Section 5...
Page 82: ...Fulton Heating Solutions Inc PHW Manual 2010 0713 Page 82...
Page 90: ...Fulton Heating Solutions Inc PHW Manual 2010 0713 Page 90...
Page 92: ...Fulton Heating Solutions Inc PHW Manual 2010 0713 Page 92...
Page 93: ...Fulton Heating Solutions Inc PHW Manual 2010 0713 Page 93...