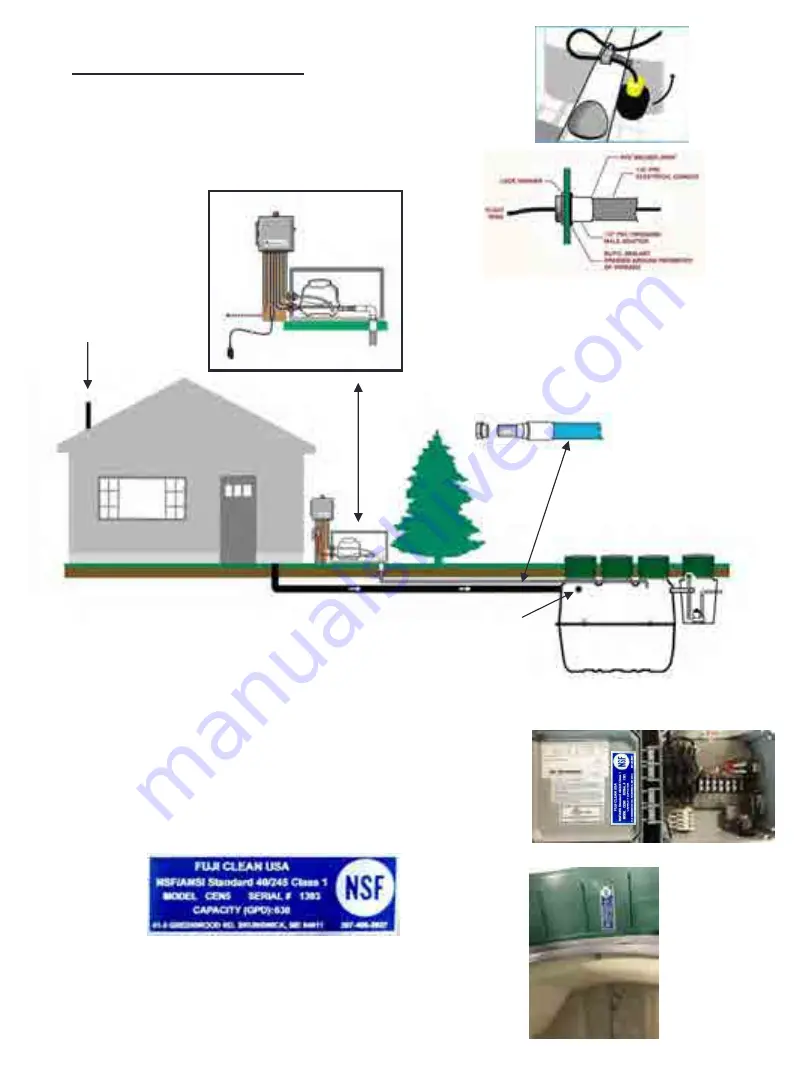
Installation Overview
For connection of SJE Rhombus Signalmaster float switch cord to alarm panel,
drill hole in riser and use male fitting and electrical conduit. Plug fitting with
sealant standard that meets ASTM C990-96 to assure water-tight seal and to
prevent septic gas transmission into control panel. Install on the pumpback line
using the provided hose clamp and mounting fixture in the center of
Chamber 2, (Anaerobic Contact Filtration Chamber) with 3-
/
of
electrical cord tether.
Fuji Clean USA
Treatment Tank
Please Note:
1.
Fuji Clean systems are designed to accept straight septic wastewater
and do not require a preceding septic or settling tank
2.
Clear ater ater softe er a k ash should e dis harged dire tl
to a separate drywell or leaching pool.
Using grommets or a waterproof adhesive, labels meeting NSF standards (supplied by
Fuji Clean USA) shall be affixed in two locations, inside the inlet riser and on the
inside of the controller.
PVC
inlet and outlet pipe
Pump Station
(if site conditions or
design dictates)
System Controller/Alarm
(supplied by Fuji Clean USA)
Suffolk County requires
FujiMACRII series blower
power connection to be
hardwired to control panel.
Sample Label
Ma Riser Height
For connection air line to tank,
use Fuji Clean supplied tank
adaptor a d either ¾ or
conduit or flexible pipe. Air
li e should e less tha
’
a d ha e or fe er el o s.
(If site conditions will not
allow, please contact Fuji Clean
for blower upsize calculation.
System vents through
house vent system. For
houses with house traps
installed, vent system
separately through vent
hole.
Hardwired power
connection
e t hole for s ste s ith
house traps or otherwise
encumbered access house vent
Air Line
2
Summary of Contents for CE Series
Page 8: ...6 ...
Page 11: ...Co troller A Wiri g Diagram 9 ...
Page 12: ...Co troller C Wiri g Diagram 10 ...
Page 14: ...12 ...
Page 22: ... 20 ...
Page 37: ......
Page 38: ......
Page 39: ......
Page 41: ... PAGE 1 OF 7 PAGES ...
Page 42: ... 30 ELBOW 120 WYE 45 ELBOW 45 BEND PAGE 2 OF 7 PAGES ...
Page 46: ...PAGE 7 OF 7 PAGES ...