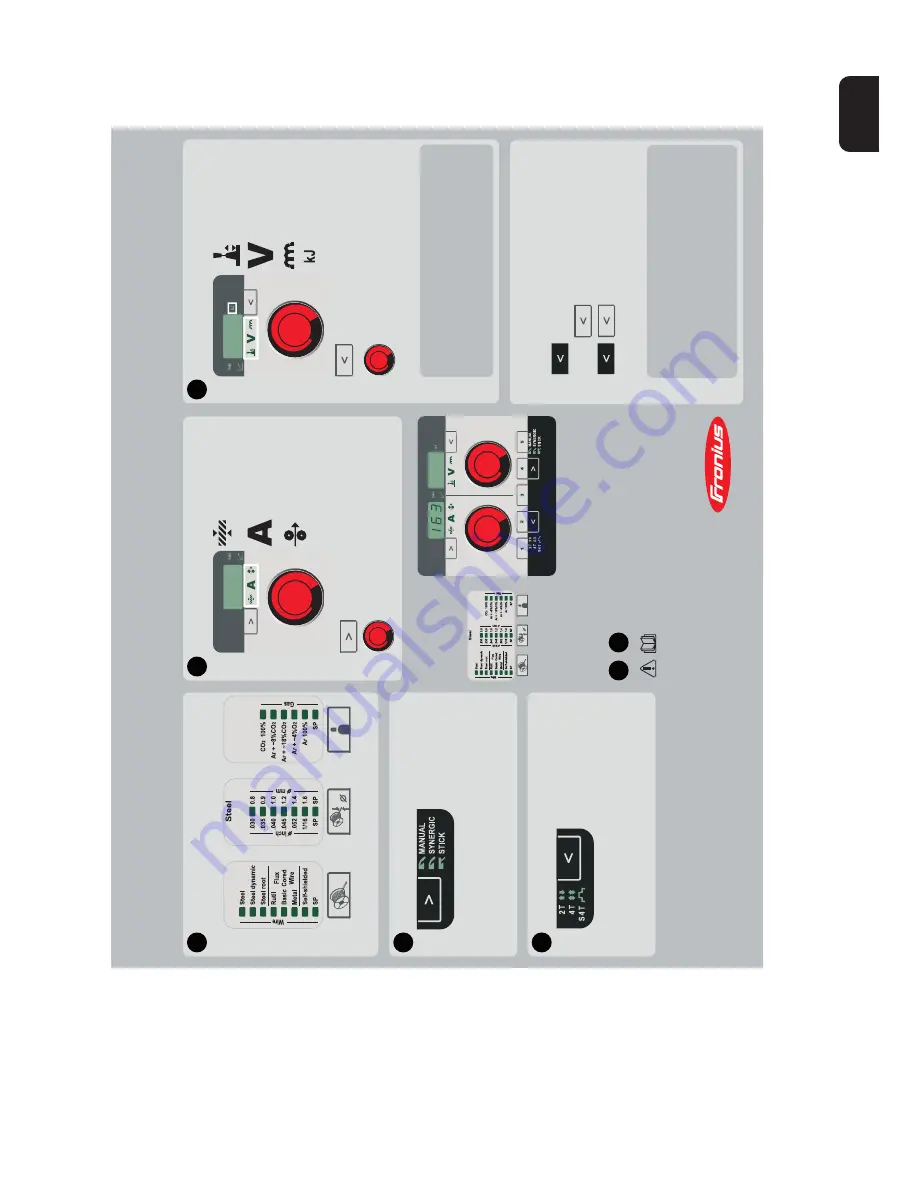
97
EN
Quick reference
4
1
3
2
5
Fronius International GmbH, www
.fronius.com
Keylock
Important!
If the keylock is activated, only the
parameter settings can be retrieved, as well
as any assigned “Save“ button provided that
an assigned “Save“ button was selected when
the keylock was enabled.
-
press and hold
- press
- release
activate / deactivate:
activated: „CLO | SEd“ display
deactivated: „OP
| En“ display
Quick Reference: English
Setting the welding power
Selecting the fi
ller metal and
shielding gas
2 T
2-step
mode
4 T
4-step
mode
S 4
T
Special 4-step mode
Selecting the process
Setting the mode
MANUAL
MIG/MAG standard manual
SYNERGIC Standard
synergic
STICK
Manual metal arc welding
Correcting parameters
Important
If external system components
are connected, some parameters can be
modifi
ed on those components.
The power
source control panel is only for display
purposes.
01/2013
Start-up sequence
Follow operating instructions
-
1
5
T
ransSteel Synergic
SP
... Special Program
-
select desired parameter
- set desired parameter
Sheet thickness
W
elding current
Wire feed speed
Arc length
correction
W
elding voltage
Dynamic
-
select desired parameter
- set desired parameter
Real Energy Input
Summary of Contents for TransSteel 3500 Rob
Page 2: ...2...
Page 4: ...4...
Page 8: ...8...
Page 20: ...20...
Page 21: ...General information...
Page 22: ......
Page 27: ...Control elements and connections...
Page 28: ......
Page 35: ...Installation and commissioning...
Page 36: ......
Page 46: ...46...
Page 47: ...Welding...
Page 48: ......
Page 61: ...61 EN Number 3 Number 4 Number 5...
Page 62: ...62...
Page 63: ...Setup settings...
Page 64: ......
Page 76: ...76...
Page 77: ...Troubleshooting and maintenance...
Page 78: ......
Page 99: ...Appendix...
Page 100: ...100 Spare parts list TSt 3500 Rob TSt 5000 Rob...
Page 102: ...102...
Page 103: ...103...