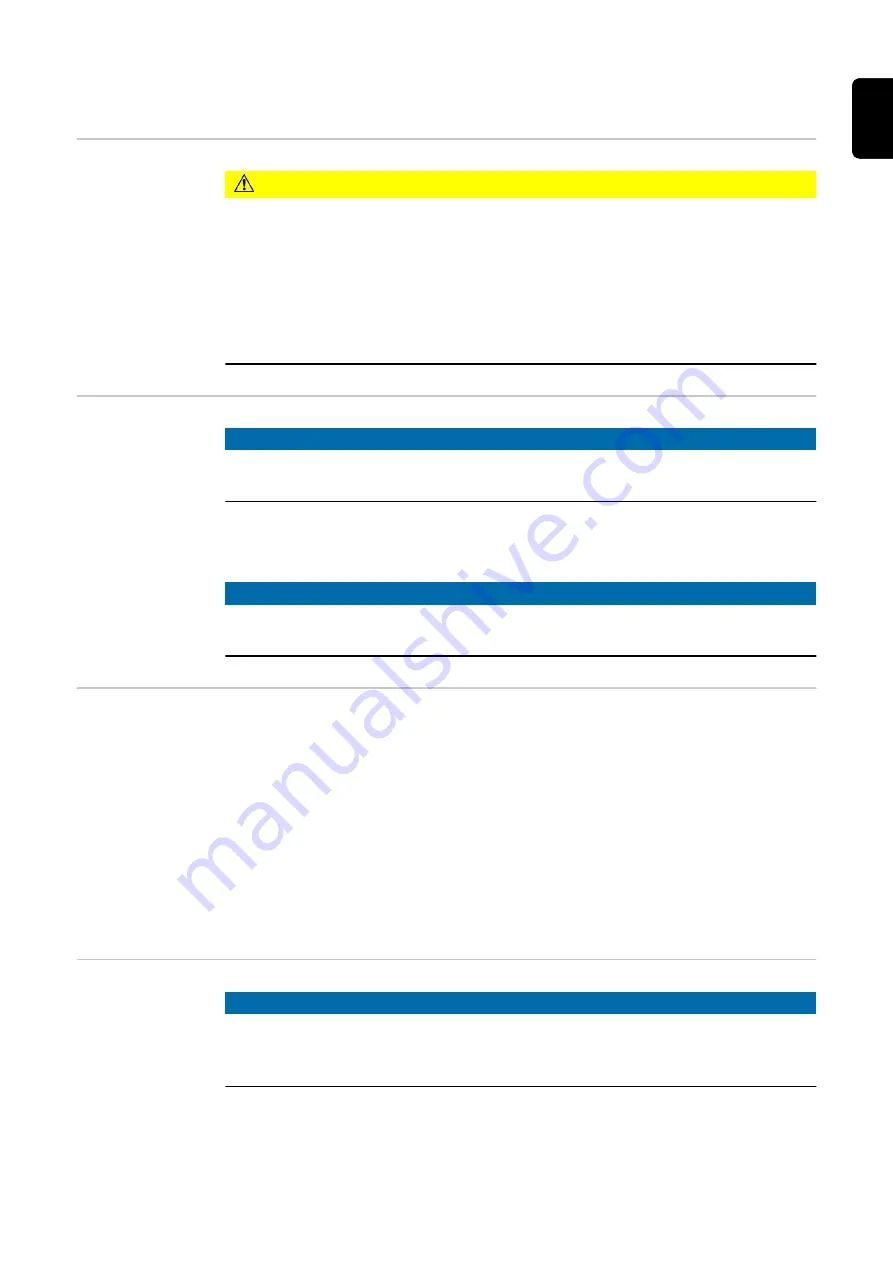
Fitting the OPT / i MHP WireBrake and torch body
Safety
CAUTION!
Risk of burns from hot torch body, hot torch body coupling and other hot welding
torch components.
Before starting work on the torch body, the torch body coupling and all other welding
torch components:
▶
Allow the torch body, torch body coupling and all other welding torch components to
cool down to room temperature (+25 °C, +77 °F)
▶
Wear electrically insulated and heat protective gloves
▶
Use a suitable tool
Prerequisites for
operation
NOTE!
OPT/i MHP WireBrake only secures a wire electrode if a torch body is correctly fit-
ted to the OPT/i MHP WireBrake.
System requirements: The wirefeeder of the WF 15i/25i/30i R (PAP) series with the
"16 bar gas purging" option.
NOTE!
To ensure that the WireBrake option functions correctly, wait for 4 seconds after
deactivating the "WireBrake on" signal before activating another signal.
Compressed air
supply specifica-
tions
The compressed air supply of the OPT/i MHP WireBrake is provided through the hosep-
ack.
Observe the following specifications:
-
Compressed air supply of at least 5 bar (72 psi)
-
Compressed air supply for aluminium max. 7 bar (102 psi), for all other materials
max. 16 bar (232 psi)
-
Compressed air is free of oil
-
Compressed air is free of dust – no dirt particles larger than 5 mm
-
Compressed air is free of water
Recommendation: use a filter unit with a pressure regulator.
Remedying the
clamping marks
on the wire elec-
trode
NOTE!
When securing the wire electrode in the OPT/i MHP WireBrake, small clamping
marks can occur on the wire electrode.
▶
To remedy the clamping marks, cut off the wire electrode after securing.
Calculation of the cut-off point = torch body 50 mm (1.97 in.)
81
EN
Summary of Contents for TPS/i Push
Page 2: ......
Page 20: ...20...
Page 21: ...System configurations 21...
Page 22: ...22...
Page 29: ...System components 29...
Page 30: ...30...
Page 43: ...Controls connections and mechan ical components 43...
Page 44: ...44...
Page 58: ...58...
Page 59: ...Installation conventional robot 59...
Page 60: ...60...
Page 66: ...3 3 Nm 2 43 lb ft 2 6 Nm 4 43 lb ft 3 66...
Page 74: ...2 74...
Page 79: ...WF 15i 30i R 2 WF 25i R 2 WF 25i 30i R L 1 WF 30i R L 2 WF 25i R L 2 79 EN...
Page 83: ...For steel inner liners 5 6 For plastic inner liners 5 6 83 EN...
Page 86: ...86...
Page 87: ...Installation PAP 87...
Page 88: ...88...
Page 91: ...Fitting the wire feed unit Fitting the WF 15i 25i 30i R PAP 1 2 3 4 91 EN...
Page 94: ...3 3 Nm 2 43 lb ft 2 3 Nm 2 21 lb ft 3 94...
Page 105: ...Connecting the interconnecting hosepack 105 EN...
Page 107: ...3 4 107 EN...
Page 108: ...108...
Page 109: ...Start up 109...
Page 110: ...110...
Page 114: ...3 8 6 7 9 3 1 2 2 5 4 4 3 4 5 5 6 1 2 3 4 114...
Page 119: ...Troubleshooting maintenance and disposal 119...
Page 120: ...120...
Page 129: ...5 6 7 8 9 10 129 EN...
Page 130: ...11 Removing the CrashBox PAP from the robot with mounting key 1 2 3 4 130...
Page 131: ...5 6 7 8 1 9 10 131 EN...
Page 134: ...134...
Page 135: ...Technical data 135...
Page 136: ...136...
Page 151: ...151 EN...