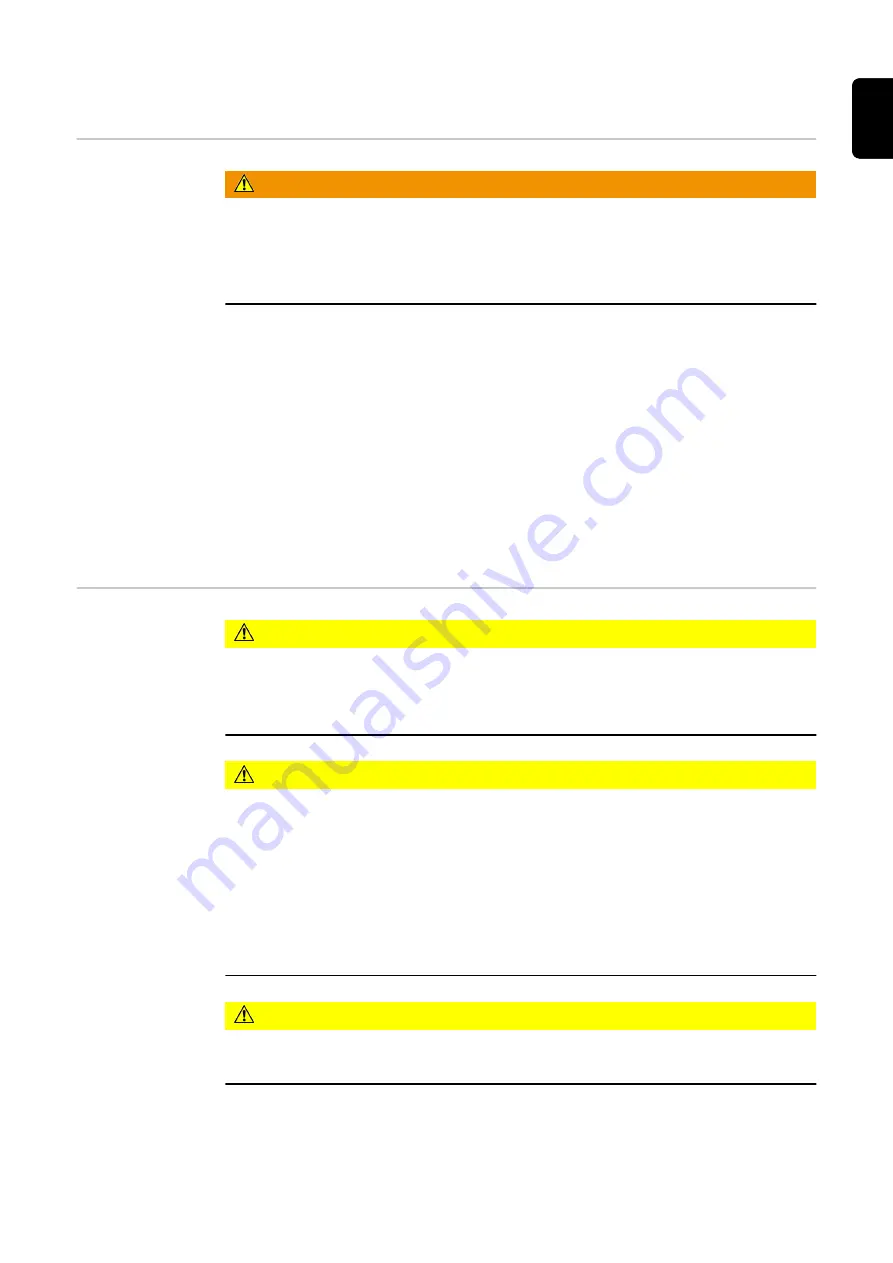
Feeding in the wire electrode
Insulated routing
of wire electrode
to wirefeeder
WARNING!
Risk of serious injury and damage or an inferior weld as a result of earth contact
or short-circuit of a non-insulated wire electrode.
▶
In the case of automated applications, ensure that only an insulated wire electrode is
routed from the welding wire drum, large wirefeeder spool or wirespool to the
wirefeeder (e.g. by using a wirefeeding hose).
An earth contact or short-circuit can be caused by:
-
a non-insulated, exposed length of wire electrode coming into contact with a con-
ductive object during the welding process
-
missing insulation between the wire electrode and the earthed enclosure of a robot
cell
-
chafed wirefeeding hoses, exposing the wire electrode
To avoid earth contact or short-circuit:
-
Use wirefeeding hoses for insulated routing of wire electrode to wirefeeder
-
To prevent chafing, do not route the wirefeeding hoses over sharp edges
-
Use hose holders or hose protectors where necessary
-
Coupling pieces and hoods for welding wire drums are recommended to ensure safe
transport of the wire electrode
Feeding in the
wire electrode
CAUTION!
Risk of injury and damage from the welding current and accidental ignition of an
arc.
▶
Before starting work, disconnect the ground earth connection between the welding
system and the workpiece.
CAUTION!
Risk of injury and damage from wire electrode emerging.
While working:
▶
Hold the welding torch with the end directed away from the face and body
▶
Wear suitable protective goggles
▶
Do not point the welding torch at people
▶
Make sure that the wire electrode does not touch any conductive or earthed parts
(e.g. housing)
▶
Ensure that all covers are closed, all side panels are in place and that all safety
devices are intact and in their proper place (e.g. protection devices).
CAUTION!
Risk of damage to the welding torch from sharp end of wire electrode.
▶
Deburr the end of the wire electrode well before threading in.
115
EN
Summary of Contents for TPS/i Push
Page 2: ......
Page 20: ...20...
Page 21: ...System configurations 21...
Page 22: ...22...
Page 29: ...System components 29...
Page 30: ...30...
Page 43: ...Controls connections and mechan ical components 43...
Page 44: ...44...
Page 58: ...58...
Page 59: ...Installation conventional robot 59...
Page 60: ...60...
Page 66: ...3 3 Nm 2 43 lb ft 2 6 Nm 4 43 lb ft 3 66...
Page 74: ...2 74...
Page 79: ...WF 15i 30i R 2 WF 25i R 2 WF 25i 30i R L 1 WF 30i R L 2 WF 25i R L 2 79 EN...
Page 83: ...For steel inner liners 5 6 For plastic inner liners 5 6 83 EN...
Page 86: ...86...
Page 87: ...Installation PAP 87...
Page 88: ...88...
Page 91: ...Fitting the wire feed unit Fitting the WF 15i 25i 30i R PAP 1 2 3 4 91 EN...
Page 94: ...3 3 Nm 2 43 lb ft 2 3 Nm 2 21 lb ft 3 94...
Page 105: ...Connecting the interconnecting hosepack 105 EN...
Page 107: ...3 4 107 EN...
Page 108: ...108...
Page 109: ...Start up 109...
Page 110: ...110...
Page 114: ...3 8 6 7 9 3 1 2 2 5 4 4 3 4 5 5 6 1 2 3 4 114...
Page 119: ...Troubleshooting maintenance and disposal 119...
Page 120: ...120...
Page 129: ...5 6 7 8 9 10 129 EN...
Page 130: ...11 Removing the CrashBox PAP from the robot with mounting key 1 2 3 4 130...
Page 131: ...5 6 7 8 1 9 10 131 EN...
Page 134: ...134...
Page 135: ...Technical data 135...
Page 136: ...136...
Page 151: ...151 EN...