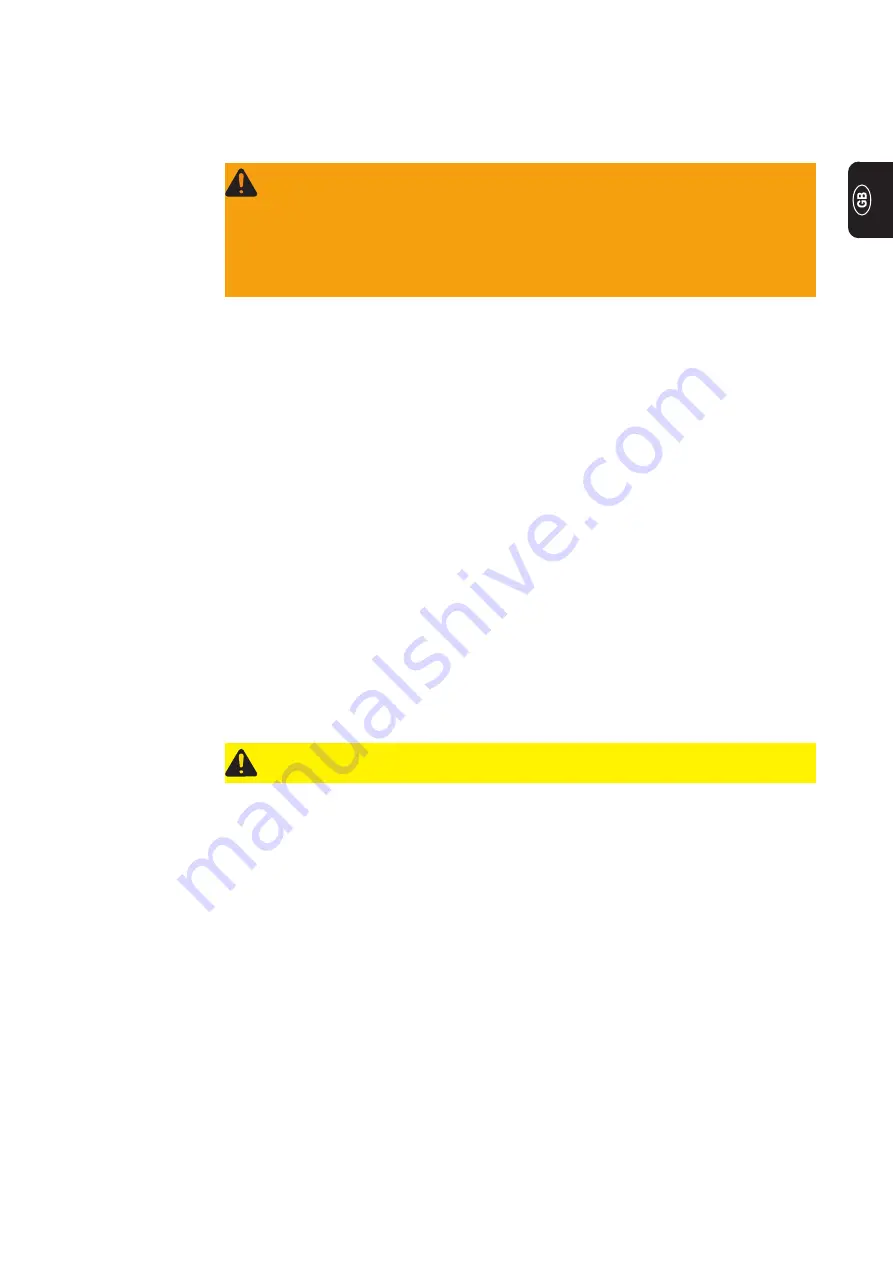
73
Care and maintenance
Before opening
up the power
source
Power source
maintenance
Maintenance of
water-cooled
welding torches
In order to keep your power source operational for years to come, you should observe
the following points:
-
Carry out safety inspections at the stipulated intervals (see the section headed
“Safety rules”)
-
Depending on the machine location, but no less often than twice a year, remove the
side panels from the machine and blow the inside of the power source clean with
dry, reduced-blow compressed air. Do not aim air-jets at electronic components
from too close a range.
-
If a lot of dust has accumulated, clean the cooling-air ducts.
On water-cooled welding torches
-
Check that the torch connections are watertight
-
Check the volume and quality of the coolant water (only top up with clean coolant)
-
Keep an eye on the flow-rate of the coolant returning to the coolant reservoir
Warning!
Electric shock can be fatal. Before opening up the auto-transformer,
shift the mains switch into the “0” position, unplug it from the mains and put up a
clearly legible and easy-to-understand warning sign to stop anybody inadvertently
switching the machine back on again. The housing screws provide a suitable PE
conductor connection for earthing (grounding) the housing. These screws must
NOT be replaced by any other screws which do not provide a reliable PE
conductor connection.
Maintenance of
cooling unit
Before starting to use the cooling unit, always check the level and the cleanliness of the
coolant.
Caution!
Danger of scalding from hot coolant fluid. Do not inspect the coolant
until it has been allowed to cool.
Note!
During welding, check the coolant circulation at regular intervals - it must be
possible to see (in the filler neck) that coolant is flowing back properly.
Where water-cooled welding torches are being used, check the torch connections to
ensure that these are watertight.
Explanation of the symbols on the cooling unit
The following symbols are affixed to the front of the cooling unit. They give the user
information on:
-
the maintenance jobs needing doing, and
-
at what intervals the maintenance jobs need to be performed
Summary of Contents for MagicWave 1700
Page 2: ......
Page 4: ......
Page 16: ...XII ud_fr_st_sv_00466 022002...
Page 96: ......
Page 108: ...XII ud_fr_st_sv_00467 052002...
Page 188: ......
Page 200: ...XII ud_fr_st_sv_00468 042002...
Page 283: ...TransTIG 2200...
Page 284: ...MagicWave 1700...
Page 285: ...MagicWave 2200...
Page 286: ...FK 2200...