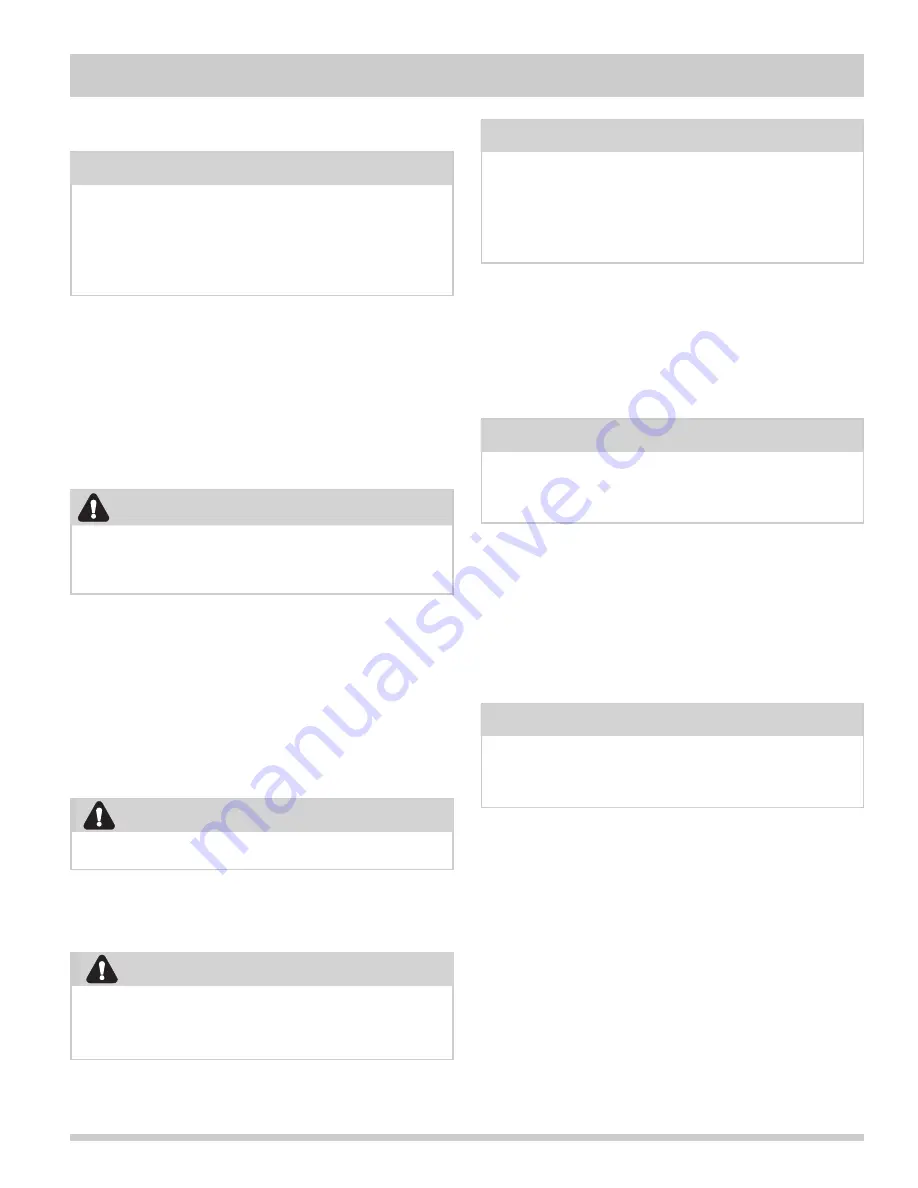
Section 4 Refrigeration
4-5
A new compressor which is cold (e.g. after having been
kept in a cold service van) should be left to warm to the
surrounding temperature before the plugs on the
compressor connections are removed. This will help
prevent condensation from forming in the oil and the
compressor. Also, avoid opening the system when any
of the components or lines are cold.
1. Disconnect electrical supply to refrigerator.
2. Remove compressor access panel.
3. Remove all components needed to pull the
compressor assembly from the unit.
4. Pull compressor assembly straight out.
5. Recover refrigerant by using EPA approved
recovery system.
6. Remove leads from compressor motor terminals.
7. Remove mounting clips and washers.
8. After refrigerant is completely recovered, cut
suction and discharge lines as close to compressor
as possible. Leave only enough tubing to pinch off
and seal defective compressor. Plug or tape any
open system tubing to avoid entrance of moisture
and air into system. Remove inoperable
compressor and transfer mounting parts to new
compressor.
9. Install new compressor in exact same manner as
original compressor.
Installing a New Compressor
Replacement of compressor and installation of filter-drier
must be done in a continuous sequence so system is
exposed to atmosphere no longer than necessary.
All replacement compressors are shipped with
rubber plugs in the suction, discharge and process tubes
and contain the correct oil charge and a holding charge
of inert gas. Compressors have a low-side process tube
attached to the compressor shell. A high-side process
tube is attached to the filter-drier.
Replacement compressors for refrigerators may have an
oil cooler even if the original compressor did not. If the
product is not equipped for an oil cooler, leave the
plastic caps in place and install the compressor
connecting only to the suction and discharge lines of the
new compressor.
Before installing the replacement compressor remove the
discharge plug and check for the pop sound of the inert
gas leaving the compressor.
If the compressor checks OK, reinstall the plug. Do not
remove any of the plugs again until the compressor is in
position and you are ready to braze the lines.
DO NOT use compressor if you do not hear this sound.
CAUTION
Release holding charge (release slowly to avoid oil
discharge) on new compressor to ensure there is no
leak in seam or tubing. Reinstall rubber plug.
NOTE
If low-side process tube is too short, silver solder
four inch piece of tubing onto process tube at this
time.
NOTE
Entirely new compressors have been developed or use
with R-134a and Ester oil refrigeration systems. Both
compressor and electric motor have been modified.
Old compressors intended for R-12 refrigerant must
not be used for new systems charged with R-134a.
NOTE
On R-134a systems, compressor must NOT be left
open to atmosphere for more than 10 minutes to
prevent moisture contamination of oil.
CAUTION
The following instructions are generalized to help the
technician understand the procedures of sealed
system repairs. See Section 5 Component Teardown
on the exact steps of accessing the components of
the refrigeration system.
NOTE
Do not operate reciprocating compressor when
charging liquid refrigerant into system through its
process tube.
WARNING
Summary of Contents for FFH17F8HW0
Page 2: ......
Page 14: ...Section 2 Installation Information 2 6 Notes ...
Page 18: ...Section 3 Electronic Control 3 4 Notes ...
Page 33: ...Section 4 Refrigeration 4 15 HFC 134a CFC 12 Pressure Temperature Chart ...
Page 36: ...Section 4 Refrigeration 4 18 Notes ...
Page 48: ...Section 5 Component Teardown 5 12 Notes ...
Page 53: ...Section 7 Wiring Diagram 7 1 ...