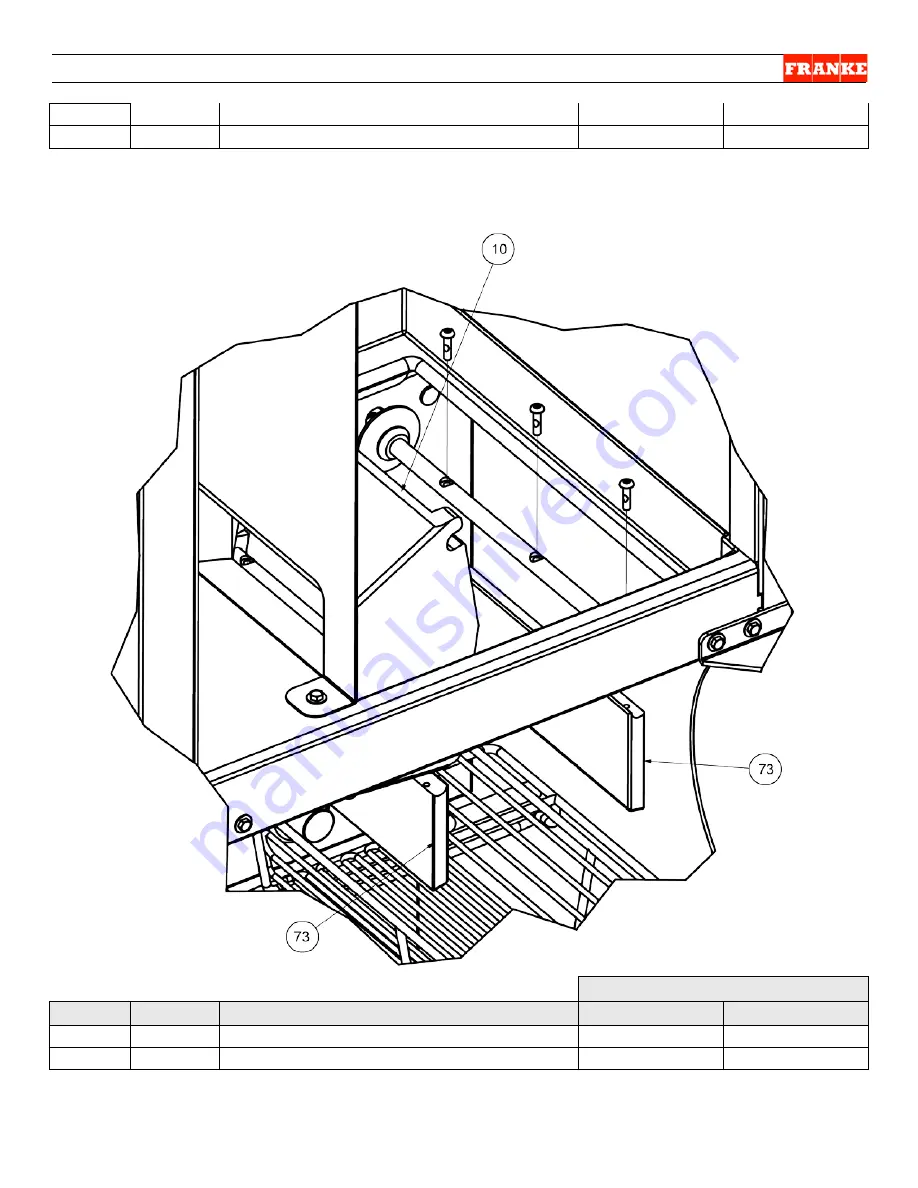
F3D3 Series Service Manual Parts List & Component Diagrams / Section 1.5
Questions? Call Franke Technical Support Group For Your Area.
Page
10
Copyright
2011 Franke, Inc. All rights reserved.
71
2 ea.
Screw, Motor Mounting – M5 35 mm long
19002766
19002766
72
1 ea.
Door Lift Shaft
19000198
19000198
Dispense Doors & Bucket (All F3D3 Versions)
Part Numbers
Key No.
Quantity
Description
120-Volt/60 Hz
230-Volt/50 Hz
10
1 ea.
Bucket, Silicone (fries)
19002725
19002725
73
2 ea.
Doors, Product Dispensing w/screws
19003534
19003534